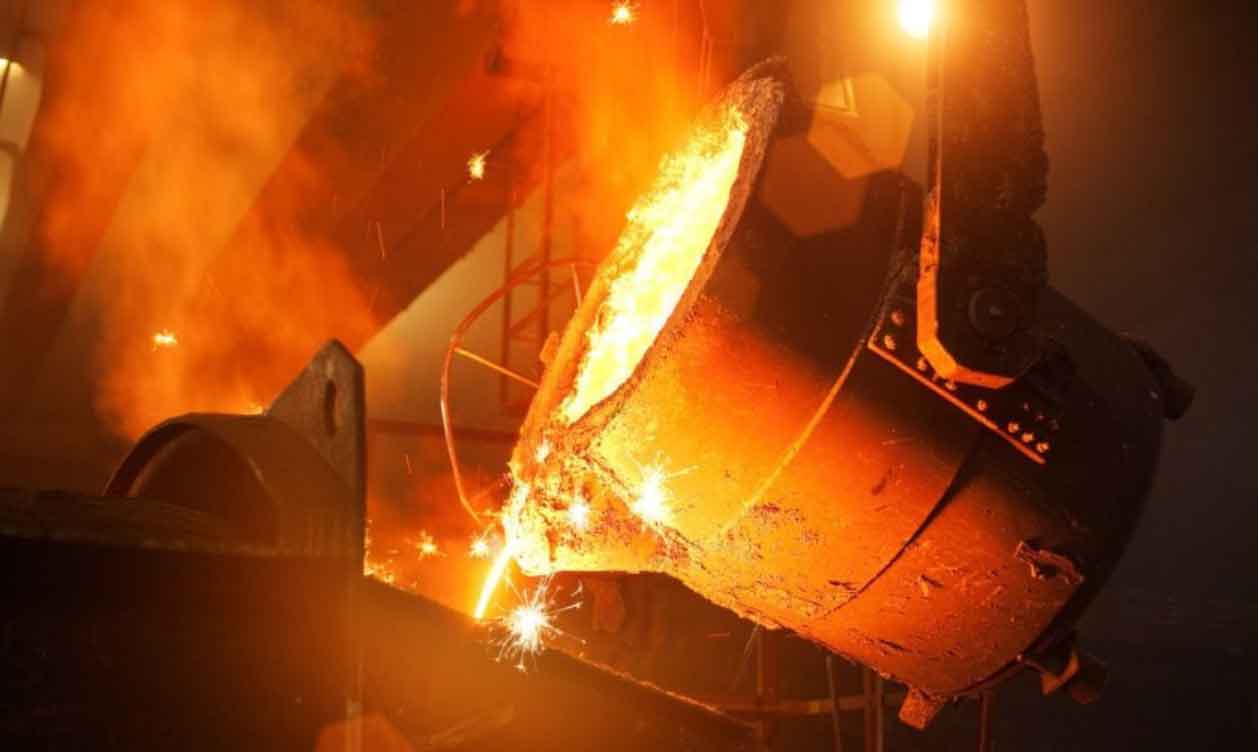
Sand casting and investment casting are two widely used casting processes in manufacturing. While both methods are used to create complex metal parts, they differ in terms of process, cost, surface finish, and dimensional accuracy. Let’s compare sand casting and investment casting in detail:
- Process:
- Sand Casting: In sand casting, a pattern of the desired part is made from wood, metal, or plastic. The pattern is pressed into a specially prepared sand mixture, creating a mold cavity. Molten metal is then poured into the mold, and after cooling, the sand is removed to reveal the solidified casting.
- Investment Casting: Investment casting, also known as lost-wax casting, involves creating a wax pattern of the part. The wax pattern is then coated with a ceramic material to form a ceramic shell mold. The wax is melted out, leaving a cavity in the mold. Molten metal is poured into the mold, and once solidified, the ceramic shell is broken away to obtain the casting.
- Complexity and Design Flexibility:
- Sand Casting: Sand casting is well-suited for large and heavy parts with complex shapes and intricate details. It allows for more design flexibility, as the sand molds can be easily modified or repaired during the process.
- Investment Casting: Investment casting is suitable for both small and large parts and can achieve excellent surface finish and dimensional accuracy. It is particularly advantageous for parts with intricate details, fine features, and thin walls, where tight tolerances are required.
- Surface Finish and Dimensional Accuracy:
- Sand Casting: Sand casting typically produces rougher surface finishes compared to investment casting. The texture and quality of the sand can affect the final surface appearance. Dimensional accuracy is generally lower due to the possibility of sand shifting or mold expansion.
- Investment Casting: Investment casting results in smoother and more precise surface finishes. The ceramic shell molds provide better dimensional control and can achieve tighter tolerances. It allows for intricate details and excellent reproduction of the wax pattern.
- Cost and Production Volume:
- Sand Casting: Sand casting is a cost-effective method for low to medium production volumes. The initial tooling costs are relatively lower compared to investment casting. However, as the complexity of the part increases, the cost of the sand mold may rise.
- Investment Casting: Investment casting is generally more expensive than sand casting, primarily due to the additional steps involved in creating the wax patterns and ceramic molds. It is more suitable for high-value parts or low to medium production volumes.
- Material Selection:
- Sand Casting: Sand casting can accommodate a wide range of metals and alloys, including cast iron, steel, aluminum, bronze, and brass. It is versatile in terms of material selection.
- Investment Casting: Investment casting is compatible with a variety of metals and alloys, such as stainless steel, carbon steel, aluminum, bronze, and nickel-based alloys. It is particularly suitable for casting high-performance alloys.
Sand casting and investment casting each have their advantages and are suited for different applications. Sand casting is preferred for larger, less complex parts with lower dimensional accuracy requirements and moderate production volumes. On the other hand, investment casting is well-suited for smaller, more intricate parts with high precision, superior surface finish, and tighter tolerances, but at a higher cost. The choice between the two processes depends on factors such as part complexity, required surface finish, dimensional accuracy, production volume, and budget.