The process of resin sand casting involves several steps, starting from the creation of the mold to the solidification of the metal. Here is a step-by-step overview of the resin sand casting process:
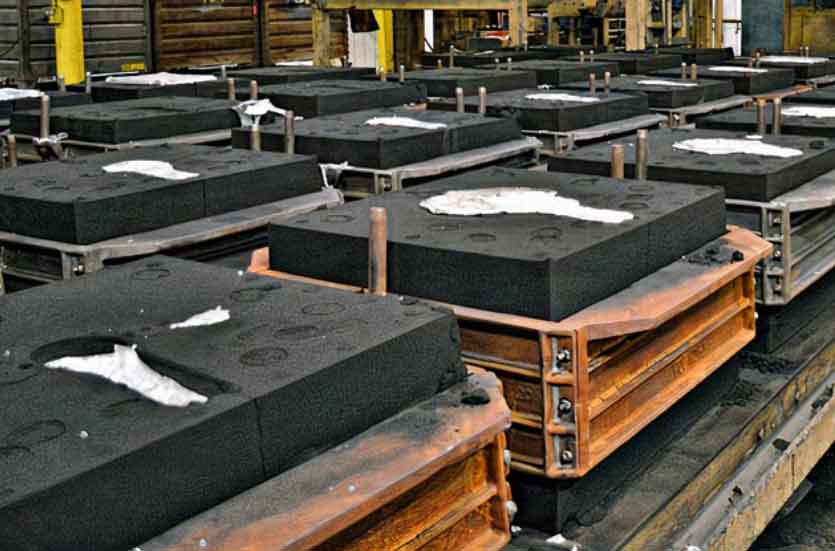
- Pattern creation: The first step is to create a pattern, which is a replica of the desired final product. The pattern is typically made from wood, plastic, or metal. It is shaped to match the desired part geometry, including any undercuts or intricate details.
- Mold preparation: The pattern is then placed in a flask, which is a box-like container that will hold the sand mold. The flask is divided into two halves, known as the cope (top) and the drag (bottom). The pattern is positioned in the drag, and a release agent may be applied to prevent the sand from sticking to the pattern.
- Sand mixture preparation: A mixture of sand and resin is prepared. The sand is usually silica sand, and the resin is a thermosetting resin, such as phenolic resin or furan resin. The sand is mixed with the resin and other additives to improve its strength, permeability, and collapsibility.
- Sand molding: The sand mixture is poured into the drag half of the flask, covering the pattern completely. The sand is compacted around the pattern using various methods, such as hand ramming, jolt-squeeze machines, or automated molding equipment. The cope half of the flask is then placed on top, and the two halves are securely clamped together.
- Pattern removal: The flask is inverted, and the drag half is separated from the cope half. This exposes the pattern, which is carefully removed from the sand mold. The pattern can be reused for subsequent molds.
- Core placement (if required): If the final product requires internal cavities or hollow sections, sand cores are inserted into the mold. Cores are made from a similar sand and resin mixture and are positioned in the mold before closing the flask. They provide the desired shape for the internal features of the casting.
- Metal pouring: The mold is closed, and molten metal is poured into the mold cavity through a sprue, which is a channel connected to the mold. The metal fills the mold, displacing the air and taking the shape of the mold cavity and the cores (if present).
- Solidification and cooling: Once the mold is filled with molten metal, it is allowed to cool and solidify. The solidification time depends on the type and size of the casting and the metal being used. During solidification, the metal takes on the shape of the mold and forms the final casting.
- Mold removal and cleaning: After the metal has solidified and cooled, the flask is opened, and the sand mold is broken away from the solidified casting. This process is called shakeout. The casting is then cleaned to remove any remaining sand, gating system, and surface imperfections.
- Finishing operations: Depending on the desired specifications and surface finish, the casting may undergo additional finishing operations, such as trimming excess material, grinding, machining, polishing, or heat treatment. These processes help achieve the final dimensions, surface quality, and mechanical properties required for the product.
The resin sand casting process is a versatile and widely used method for producing complex metal components. It allows for the production of detailed and dimensionally accurate castings in a cost-effective manner.