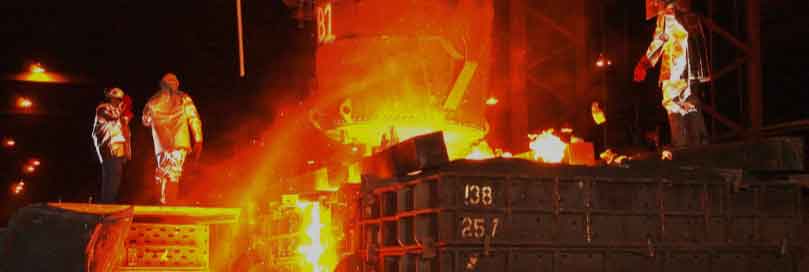
From sand to steel, advanced foundry technology plays a crucial role in the transformation of raw materials into high-quality metal components. Let’s delve into the secrets behind these innovative techniques that have revolutionized the foundry industry.
Pattern and Mold Making:
The process begins with the creation of patterns, which are replicas of the final component. Traditionally made of wood, patterns are now often produced using advanced materials like plastic or metal. Computer-aided design (CAD) and computer-aided manufacturing (CAM) technologies enable precise pattern design and machining. These patterns are used to create molds, which can be made of sand, ceramic, or even 3D-printed materials. Molds serve as the negative impression of the component and determine the final shape and surface finish.
Sand Casting and Core Making:
Sand casting is one of the most widely used casting techniques. It involves packing sand around the pattern to form a mold cavity. Advanced foundry technology has brought significant improvements to sand casting, such as the use of automated molding machines that streamline the process and ensure consistent mold quality. Core making, the creation of internal cavities within the casting, has also benefited from innovations like 3D-printed sand cores. These cores enable the production of complex geometries and hollow structures that were once challenging to achieve.
Melting and Metal Treatment:
Melting the metal is a critical step in foundry technology. Furnaces equipped with advanced controls and sensors ensure precise temperature control and optimize energy efficiency. Induction furnaces, electric arc furnaces, and other technologies provide the heat required to melt the metal. Once molten, the metal may undergo treatments like alloying, degassing, desulfurization, and refining to achieve the desired chemical composition and purity.
Pouring and Solidification:
The molten metal is poured into the mold cavity through carefully designed gating systems to ensure proper filling without defects. Advanced techniques such as computer-controlled pouring systems and robotics enhance accuracy and repeatability. The solidification process is critical for obtaining sound and defect-free castings. Innovations like the use of chills (metal inserts that facilitate rapid cooling) and optimized cooling channels in the mold help control the solidification rate and minimize defects like shrinkage or porosity.
Finishing and Inspection:
Once the metal solidifies and the mold is removed, the casting undergoes various finishing operations. These may include removing excess material, cleaning, grinding, heat treatment, and surface treatments like shot blasting or painting. Advanced robotics and automation have made these processes more efficient, reducing manual labor and improving consistency. Additionally, non-destructive testing techniques like X-ray, ultrasound, and visual inspection ensure the quality and integrity of the final product.
Continuous Improvement and Quality Control:
Foundries rely on continuous improvement methodologies to enhance their processes and maintain high-quality standards. Statistical process control (SPC), Six Sigma, and lean manufacturing principles are employed to monitor and optimize process parameters, reduce variability, and minimize defects. Data analytics and real-time monitoring systems enable quick detection of deviations and facilitate timely corrective actions.
By combining these secrets of advanced foundry technology, manufacturers can produce components of superior quality, with complex geometries and precise specifications. As the industry progresses, further innovations are anticipated, including the integration of artificial intelligence, machine learning, and advanced robotics, enabling even greater efficiency, accuracy, and sustainability in foundry operations.