Based on the simulation and optimization scheme under the virtual conditions, according to the process planning route, the mold is actually made. The core is made of coated sand, the sand core is solidified, dipped and dried, the static molding line is used for clay sand molding, and the molten iron smelting is made of medium frequency induction furnace. According to the preset pouring temperature of 1440 ℃~1400 ℃, the reverse spheroidization temperature is 1510 ℃~1520 ℃, and the flow inoculant is added during pouring 15%, the pouring time is controlled at about 10 s.
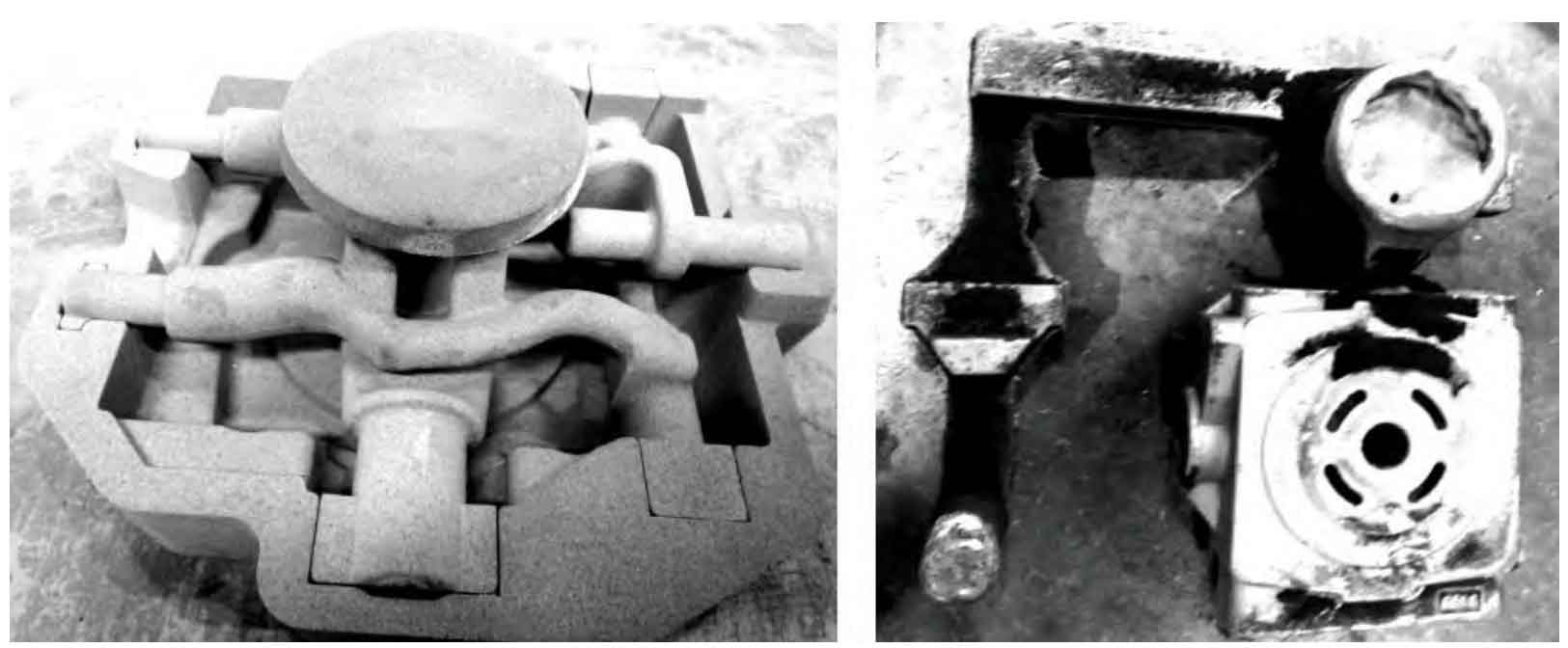
Fig. 1 The sand core of the pump cover and the cast ductile iron parts, due to the thin oil channel inside the pump cover, the slow cooling of the solidification and heat dissipation center, and the ductile iron parts are close to the solid, so the top surface of the riser shrinks greatly, and the riser has a good shrinkage effect. Photo 2 Inspection for ductile cast iron castings and sections of pump cover. The appearance of ductile cast iron castings of pump cover is smooth and clean after removal of riser, grinding and shot blasting after casting and cooling. The internal oil passages are clean through visual and endoscopic inspection. There are no defects exceeding the standard in UT flaw detection and no defects in sampling section detection. Through the actual pouring verification, the casting process is qualified, and the rejection rate of casting batch production can be controlled below 4%. The new type of pump cover ductile iron castings have been successfully developed at one time.
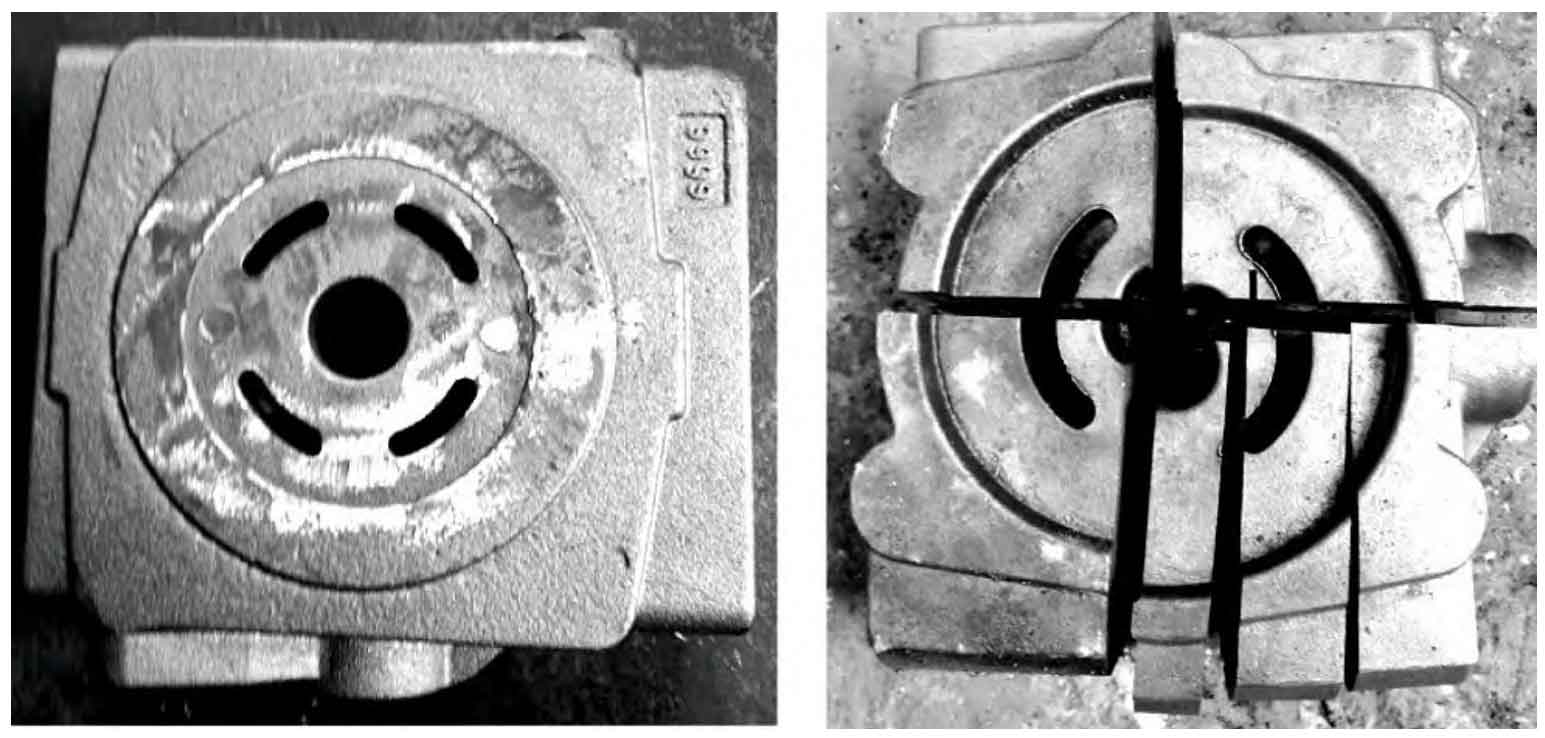
(1) Due to the special structure of the new pump cover ductile iron castings, a comprehensive casting feasibility analysis was carried out during the initial planning of the casting process to determine the process route;
(2) Based on the above comprehensive evaluation of the casting process plan, the casting simulation software is used for revalidation to effectively ensure the early process quality;
(3) The one-time process development of the actual pouring pump cover ductile iron castings is qualified, improving the efficiency of new casting research and development.