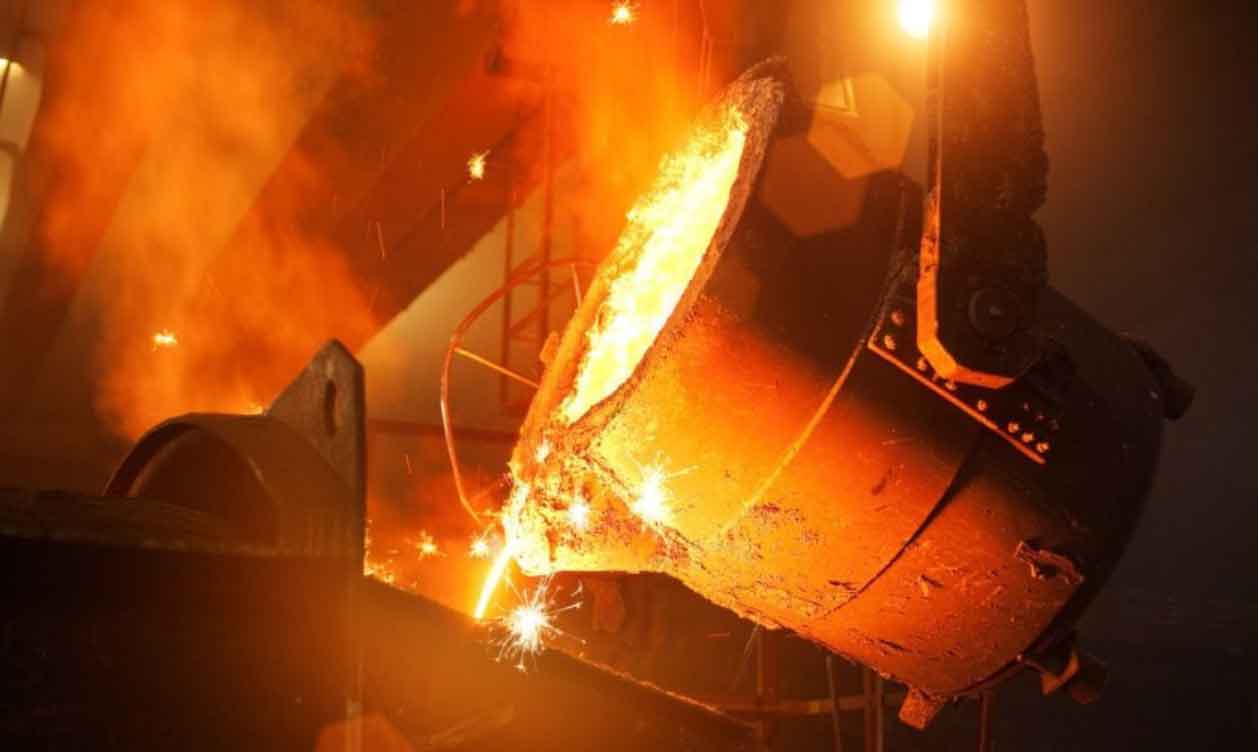
Steel casting offers several advantages that contribute to efficiency and cost-effectiveness in metal production. Let’s explore how steel casting ensures efficiency and cost-effectiveness:
1. Design Flexibility and Complex Geometries:
Steel casting allows for the production of complex shapes and intricate geometries that may be difficult or costly to achieve through other manufacturing processes. This design flexibility reduces the need for additional machining or assembly operations, streamlining the production process and minimizing material waste.
2. High Production Rates:
Steel casting processes, such as investment casting or continuous casting, enable high production rates and large-scale manufacturing. This efficiency in production helps meet high demand and reduces unit costs associated with longer production times.
3. Material Efficiency:
Steel casting processes utilize the precise amount of molten metal required for each casting, minimizing material waste. The ability to create near-net shape components reduces the need for excessive material removal through machining, resulting in cost savings and improved material utilization.
4. Cost-Effective Tooling:
Compared to other manufacturing methods, steel casting often involves lower tooling costs. Once the initial tooling, such as patterns or molds, is created, it can be used repeatedly to produce multiple castings. This cost-effective tooling reduces the per-unit cost of castings over time.
5. Material Properties and Performance:
Steel castings offer exceptional mechanical properties, including high strength, toughness, and wear resistance. By selecting the appropriate steel alloy for the intended application, manufacturers can achieve optimized performance, reducing the risk of premature component failure and associated costs.
6. Weight Reduction and Consolidation:
Steel castings allow for weight reduction and part consolidation. By creating complex shapes and integrating multiple components into a single casting, manufacturers can reduce the overall weight of an assembly, minimize the number of individual parts, and simplify assembly processes. This reduces material costs and improves overall efficiency.
7. Efficient Production of Large Components:
Steel casting is well-suited for the production of large and heavy components, such as turbine blades, pump casings, or industrial machinery parts. The ability to produce such components as a single casting eliminates the need for costly fabrication or welding of multiple smaller parts, resulting in cost savings and improved efficiency.
8. Consistent Quality and Dimensional Accuracy:
Steel casting processes enable the production of castings with consistent quality and high dimensional accuracy. This reduces the need for extensive post-casting machining and inspection, saving time and costs associated with additional operations.
9. Process Control and Automation:
Advancements in process control and automation technologies have improved the efficiency and cost-effectiveness of steel casting. Automated systems for mold handling, pouring, and finishing operations minimize manual labor and enhance productivity. Advanced monitoring and control systems ensure consistent process parameters, reducing variability and improving casting quality.
By leveraging the efficiency and cost-effectiveness of steel casting, manufacturers can achieve significant savings in production costs while maintaining high-quality metal components. The ability to produce complex shapes, optimize material usage, and streamline production processes makes steel casting an attractive choice for various industries seeking efficient and cost-effective metal production solutions.