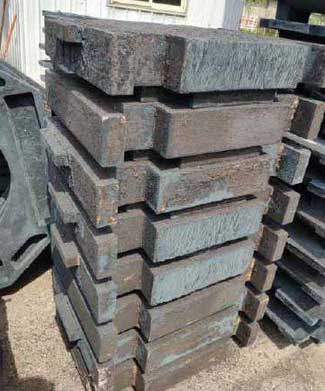
Using the process plan after the second optimization, the small batch production verification of steel and steel bearing was carried out in the production unit. A total of 50 pieces were produced. The casting blank is shown in Figure 1.
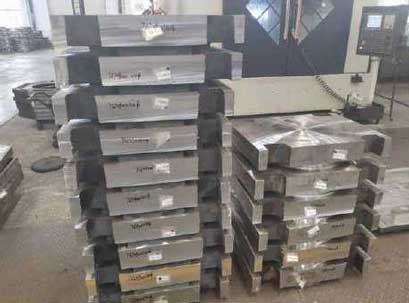
After the casting is machined, the surface quality is inspected by visual inspection and the internal quality is detected by ultrasonic flaw detector. The verification results show that 48 of the 50 bearings are qualified, and the qualified rate is 96%. The qualified products after processing are shown in Fig. 2. Two of them were scrapped due to the inclusion in molten steel soft into the mold cavity, resulting in slag porosity defects. See Fig. 3 for slag porosity defects of scrapped castings.
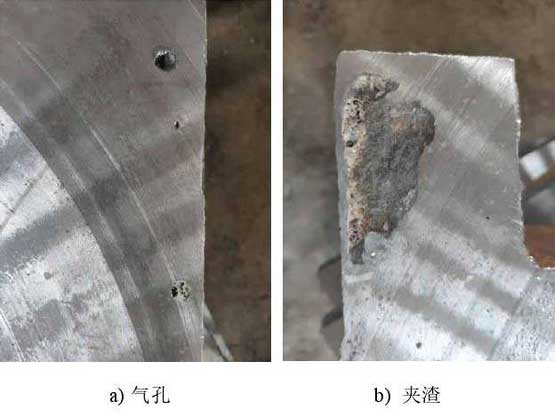
In order to further analyze the distribution of inclusions in molten steel in EPC mold, the “particle tracking” function of ProCAST simulation software was used to study and analyze. The simulation results of particle tracking are shown in Figure 4.
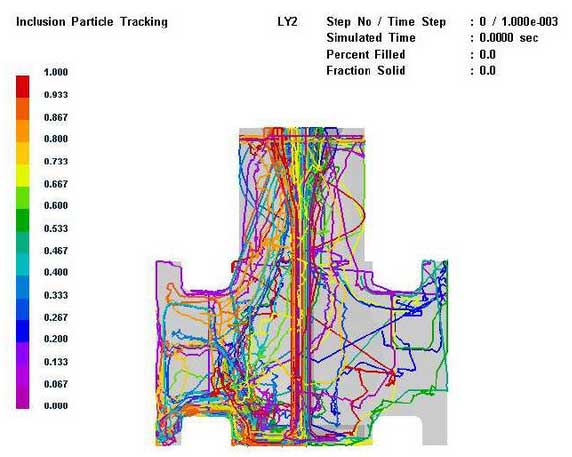
From Fig. 4, it can be seen that after the inclusions in molten steel are soft into the mold cavity, their soft moving directions are relatively disordered. Most of the inclusions are finally soft into the riser, but some inclusions still remain at the corner of the casting. The sources of molten steel inclusions include slag from molten steel smelting, residue from pyrolysis of foam pattern, gas and slag from molten steel. Because the chill is set at the corner of the casting, the cooling speed is fast. When the inclusions in the steel water are soft to the corner, they are easy to adsorb on the surface of the casting, and finally form slag inclusion, porosity and other defects. To solve these problems, it is necessary to control the quality of molten steel from the process of smelting and pouring to ensure the purity of molten steel.