Automobile clutch pressure plate is an important part of clutch, which is of great significance to automobile driving safety. The pressure plate is connected to the flywheel through bolts, and the clutch plate is located between the pressure plate and the flywheel. When the vehicle needs engine power to drive, the pressure plate presses the clutch plate with force to transmit engine power to the transmission system to drive the vehicle. When the clutch pedal is depressed, the release bearing presses the pressure plate pressure lever to compress the spring. Therefore, there is a gap between the clutch plate and the pressure plate surface to separate them. Most of the pressure plates are made of vermicular cast iron. Due to the uneven temperature field during the casting process, the yield limit and elastic modulus of metal materials will be unevenly distributed, and the thermoplasticity at high temperature will also be unevenly distributed, which will produce residual stress, thus affecting the dimensional accuracy, service life and forming quality of the pressure plates [. Therefore, it is very important to study the forming quality of vermicular cast iron for automobile clutch pressure plates.
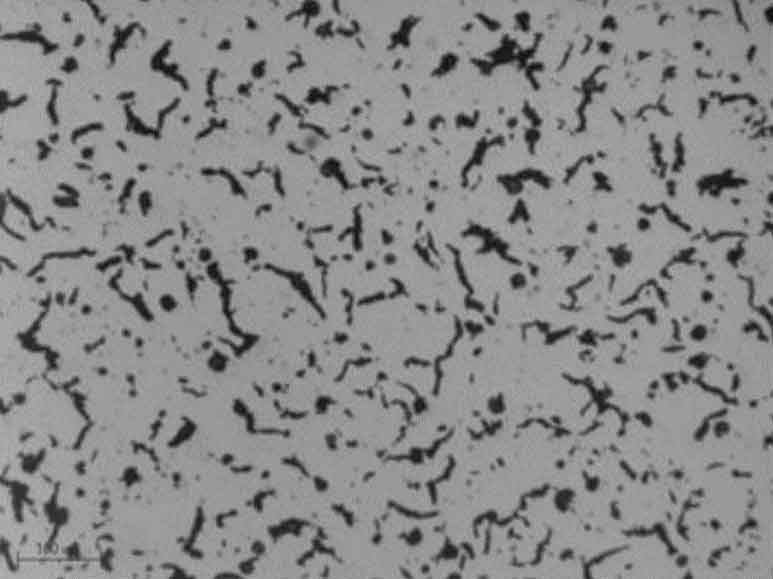
The original process of vermicular cast iron for automobile clutch pressure plate was simulated by the finite element software ProCAST. The temperature and stress changes during solidification of vermicular cast iron were analyzed, and the residual stress distribution and size of vermicular cast iron were obtained. By studying the casting process parameters, the basis for improving and optimizing the casting process scheme can be provided, and the product quality and production efficiency can be greatly improved.
The casting process of vermicular graphite cast iron pressure plate was numerically simulated. The results showed that the maximum temperature difference of the pressure plate was about 124 ℃ when the metal liquid filled the mold. Due to the setting of riser and the different wall thickness of pressure plate, there is uneven heat dissipation in different parts during solidification, and there is a temperature gradient during the cooling process of vermicular cast iron, which keeps the thermal stress of pressure plate and reduces the flatness accuracy of pressure plate.