During the experiment, four alloys with different compositions were designed, and their compositions are shown in the table.
C | Si | Mn | S | P | Mg | Re | |
Ductile iron | 3.6-3.8 | 2.5-2.9 | <0.6 | <0.08 | <0.025 | 0.03-0.05 | 0.03-0.05 |
Grey cast iron | 3.2-3.6 | 1.9-2.2 | 0.6-0.9 | ≤0.12 | ≤0.15 | — | — |
Vermicular graphite cast iron | 3.4-3.6 | 2.4-3.0 | 0.4-0.6 | <0.06 | <0.07 | 0.03-0.05 | 0.03-0.05 |
White cast iron | 3.5-4.5 | 1.2-1.8 | 0.3-0.6 | <0.1 | <0.2 | — | — |
1.Preparation of foam model
Two kinds of samples were designed. One was a stepped sample, which was used to study the effect of sample wall thickness on the microstructure of cast iron castings; The other is a Y-shaped sample. The purpose is to study the effects of liquid iron treatment temperature, the amount of nodulizer and vibration parameters on the microstructure and properties of cast iron. The structure and dimensions of the stepped and Y-shaped samples are shown in Figure.
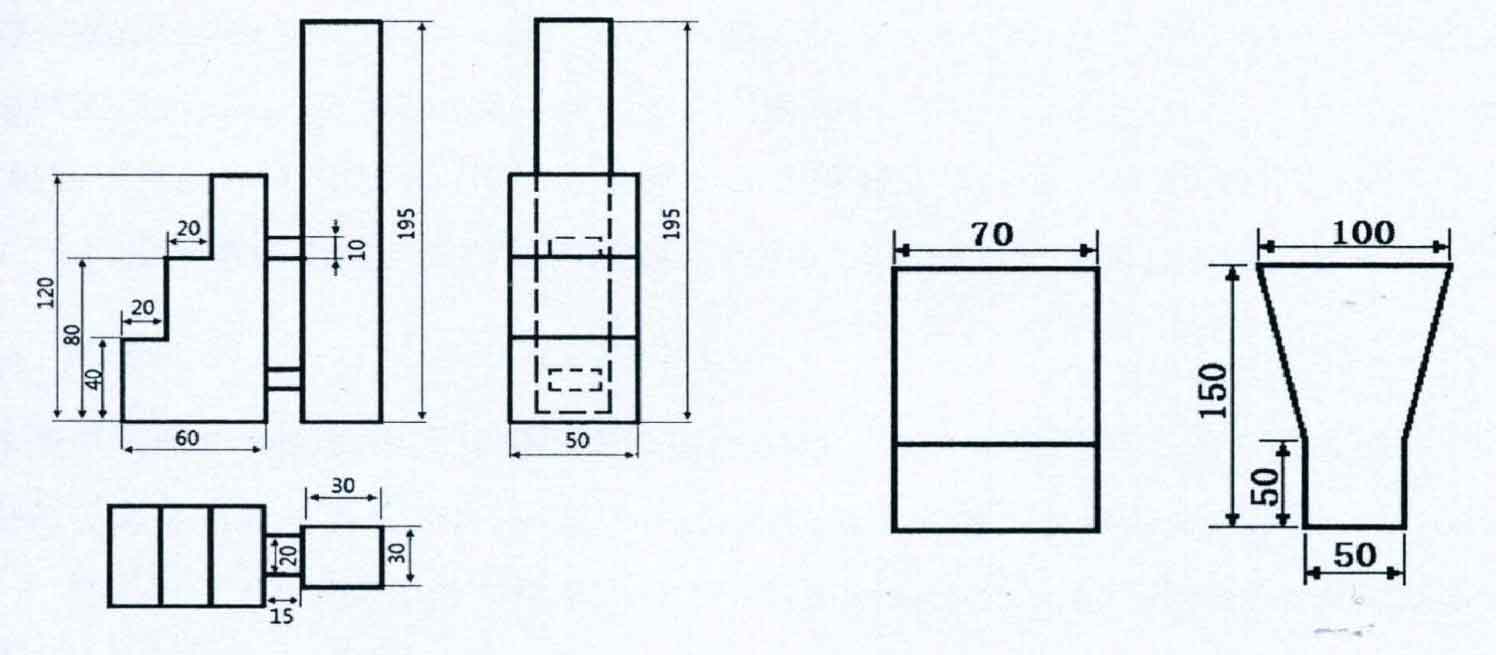
Firstly, according to the sample structure designed in the experiment, the foam plastic pattern is made by resistance wire cutting, and the pattern is bonded with hot-melt adhesive. The process includes: foam plastic plate – resistance wire cutting – bonding model.
The surface of the bonded foam plastic model is coated with a certain thickness of water-based fire-resistant coating to form a mold shell on the model surface. The water-based fire-resistant coating applied on the surface of the model can improve the strength and rigidity of the model, improve the ability of the model surface to resist the scouring of molding sand, prevent the damage of the model surface during the molding, prevent the deformation of the model during the vibration molding and negative pressure molding, and improve the accuracy of the casting.
When painting the coating, first weigh the water and coating according to m water: m fire-resistant coating powder =1.2-1.5, then put the water into the coating mixer, start the mixer, add the fire-resistant coating while searching and mixing, so as to obtain the appropriate viscosity. After the coating is mixed, it is poured into a container, and the coating is coated by dipping. Put the coated foam model into a drying room with a temperature of 50-60 ° C for drying for 24h, then apply the second coat of coating, and dry it again for standby. The thickness of the coating is about 1.0-1.5mm.
2.Modeling process
EPC adopts vibration molding, and its process includes: preparation of sand bed, placing of model, sand filling, sealing and finalization.
Lost foam casting uses dry sand without binder. Before molding, dry the sand for standby. The sand box used for the test is equipped with a special air extraction chamber and fixed on the vibration table. During molding, the bottom of the sand box shall be filled with a certain thickness of bottom sand, about 50-100mm thick, and vibrated and compacted. After vibration, the EPS model is placed on the sand bed and fixed by sand culture. Continue to add dry sand and apply vibration at the same time. The time is about 30-60s, so that all parts of the foam pattern are filled with molding sand. Finally, the surface of the sand box is covered with a layer of plastic film to seal the sand box, the vacuum pump is used to vacuum the sand box, and the pressure difference between the atmospheric pressure and the molding sand in the sand box is used to finalize the shape.
3.Melting process
Put pig iron, reheating material, steel scrap and carburizing agent for casting into the medium frequency induction furnace according to a certain proportion, heat it to 1500 ° C, and use the carbon silicon analyzer in front of the furnace to measure the carbon and silicon content in the molten iron in the furnace. Adjust the chemical composition of molten iron in the furnace according to the test results of carbon GUI rapid analyzer, and regulate the carbon and silicon content of molten iron in the furnace.
4.Pouring process
The hot metal with regulated composition is heated to the designed temperature and discharged from the furnace, inoculated and spheroidized in the ladle, and poured under the conditions of vibration and no vibration after slag removal.
Two aspects of preparation shall be done before the molten iron is discharged:
(1) Preparation before hot metal discharging
① Adjust and control the composition of molten iron in front of furnace according to the analysis and test results of carbon silicon analyzer in front of furnace;
② Pour a certain amount of molten iron into Xiao Bao for scalding;
③ Add an appropriate amount of inoculant, spheroidizing agent and creeping agent, or inoculant and spheroidizing agent into the ladle, and cover the ladle with plant ash;
④ Raise the temperature of the metal chamber in the furnace to a predetermined temperature;
⑤ The molten iron is discharged from the furnace, and the lost foam casting and vibrating lost foam casting are carried out after slag removal.
(2) Preparation for vibration bypass injection
① Modeling;
② According to the process design parameters, the vibration process parameters of the shaking table are adjusted. The parameters adjusted during the test include vibration frequency and amplitude;
③ Before the molten iron is discharged from the furnace, start the vacuum system and check the negative pressure value of the vacuum gauge. If it is different from the design parameters, it needs to be adjusted;
④ Open the vibrating table for pouring.
When the temperature of the tested part of the casting drops to 1000 ° C, stop the vibration of the shaking table, close the vacuum negative pressure system, open the box for sand removal 1h after pouring, and wait for inspection after cleaning the casting.