introduction
The wheel is the core part that ensures smooth driving of the vehicle, and the stability of the wheel structure will directly affect the safety of vehicle operation.
When driving, the wheel rims will experience radial load impact due to their contact with the road surface. At this time, if the vehicle body turns or deviates from a straight line, the body will exert axial stress on the wheel rims.casting defects If there are defects in the casting of the wheels, it will affect the stability of the wheels. Therefore, during wheel casting, it is necessary to strictly inspect for casting defects and take effective measures to repair them in a timely manner to ensure vehicle driving safety.
Taking the train wheel as the research object, after in-depth analysis of the folding defects of wide rim wheels, the method of modifying the pre-forming mold and forging die is adopted to solve the folding defects of wide rim wheels. Although this method can effectively control the folding defects of the outer rim surface of the wheel, it does not effectively clean the defective surface during the repair of the folding defects of the wheel. If the repair is not done properly, it will cause air holes to appear in the repaired defective position.
Analysis of the causes of weld cracking in steel wheels suggests that the mismatch between welding process and welding material resulted in weld cracking. This research has played a good role in enlightening the research in this paper, but this method needs to adjust the process parameters in the wheel manufacturing process to optimize the wheel casting quality when dealing with the wheel weld cracking. casting defects The pressure sealing method is currently a commonly used method for repairing pipeline material defects, and its advantages are mainly reflected in its ability to repair pipeline defects in dynamic environments. The production cost of high-strength steel wheels is very high, and an effective later stage can be adopted for casting wheels with defects The welding repair method can greatly save the casting cost by repairing the casting defects of the wheel in the later stage. Therefore, the pressure leaking method is applied to the welding repair of the casting defects of the high-strength steel wheel in this paper, and the effect of pressure leaking is analyzed by numerical simulation, providing a theoretical basis for practical application.
Welding repair method for casting defects
The main steel used for high-strength steel wheels is 40CrMnMo ultra-high-strength steel, with a yield strength of 926MPa. The chemical composition is shown in the table.
C | Mn | Si | Cr | O |
0.41 | 1.10 | 0.26 | 1.10 | 0.26 |
The method of applying pressure to plug the leak is as follows: First, based on the specific conditions of the high-strength steel wheel casting defects, the high-strength steel wheel casting defect test piece is partially tightened under the action of welding rod compressive stress. During the leak plugging process, only the part where the welding defect is located needs to be tightened, and a section of repair welding needs to be done. After a section of repair welding, casting defects another section of tightening is required, and the operation is repeated in a cyclic manner. After all defects are plugged, the repair can be stopped. This method of welding repair belongs to a segmented repair mode, which is particularly suitable for crack defects shown in the figure. The schematic diagram of the repair process is shown in the figure.
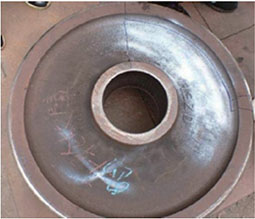
Welding rod design
High-strength steel wheel casting materials belong to metal materials, which are prone to thermal effects during pressure application and leakage blocking, resulting in regional softening and affecting the repair effect. Therefore, in this article,casting defects based on realistic standards, J107Cr welding electrodes with a tensile strength slightly lower than that of high-strength steel wheel casting materials are used as welding repair materials. Their chemical composition is shown in the table.
C | Mn | Si | Cr | Mo | V | S | P |
0.08 | 2.03 | 0.47 | 1.71 | 0.59 | 0.097 | 0.011 | 0.021 |
The schematic diagram of the preheating method is shown in the figure. The contour of the high-strength steel wheel casting defect test piece is circular, so the circular preheating tube is used in this article. After placing the test piece horizontally,casting defects the distance between the preheating tube and the test piece is controlled based on the size of the preheating flame. Generally, 40mm is the optimal distance between the two.
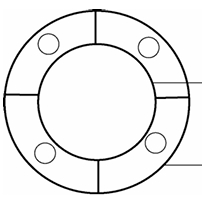
After welding repair, it is necessary to immediately use the BYH23-LCD-42 crawler heater to perform post-heat treatment on the test piece after pressure leaking is stopped. The temperature for post-heat treatment is set to 450°C,casting defects and the holding time is set to 3 hours, and then slowly reduced to room temperature. The temperature control for post-heat treatment is shown in the figure. When the temperature is consistent with room temperature, it is necessary to perform surface grinding operation on the repair position to reduce surface roughness.
Technological parameters of pressure leakage stoppage
The setting of pressure leak stoppage process parameters directly affects the effect of welding repair. Therefore, the process scheme in Table 5 is set, and the JSM-IT300 scanning electron microscope is used to analyze the changes in the surface morphology of the test piece. Combined with GB 2650-1989 and GB 2652-1989 standards, a microcomputer-based tensile testing machine is used to analyze the mechanical properties of the repaired test piece. The welder used is Shanghai Electric Welding Machine Double IGBT Module Industrial Argon Arc Welder ZX7-315S/T,casting defects with parameters such as heat input and interpass temperature of the welder.
When the content of O in the chemical elements on the surface of the casting is high, it will lead to the presence of oxidative contaminants on the surface, which will affect the welding effect. After laser cleaning, the content of O on the surface of the test piece decreases, indicating that the oxide layer on the surface of the test piece has been effectively cleaned, and the residual amount of oxide is very small,casting defects which is more conducive to welding repair.
The critical fracture stress variation diagram of the repaired position of the test specimen after pressure welding and leak repair of the high-strength steel wheel casting defects at different preheating temperatures. When the preheating temperature increases, the fracture stress at the welding repair position of the high-strength steel wheel casting defects increases. casting defects When the preheating temperature is 120°C, the fracture stress at the welding repair position is consistent with the yield strength of the steel, indicating that the preheating temperature of 120°C is the most reasonable, casting defects which can avoid welding cold cracks during the pressure welding and leak repair process of the test specimen. After performing pressure welding and leak repair on the high-strength steel wheel casting defects, the defects are effectively repaired, and there are no cracks or pores at the defect location.
conclusion
After microscopic inspection, the repaired wheel with pressure leak stoppage did not have any problems such as pores or cracks, meeting the repair standards, indicating that it is feasible to use J107Cr welding rods to repair cracks in high-strength steel wheels. The surface structure of the repaired wheel did not show any obvious abnormalities, proving that the method proposed in this article can effectively strengthen the stability of the wheel. During practical welding repair work, the following points should be noted when using the pressure leak stoppage method:
(1) When welding the defects of high-strength steel wheel casting, the pressure sealing method is feasible under the conditions set in the article, but
There are certain safety hazards in practical operation, and operators must wear protective clothing and use protective tools;
(2) The pressure sealing method requires experienced and highly skilled workers to perform, and cannot be operated by beginners to avoid causing accidents.
The welding defects become larger, which not only takes time and effort, but also increases the repair cost;
(3) Before using the pressure plugging method, it is necessary to analyze the safety and weldability of the wheel casting material to avoid unnecessary efforts.