The graphite of ball milled cast iron exists in the form of spheroid, which reduces the cleavage effect on the matrix, and the utilization rate of the matrix can reach 70-90%. Compared with other cast iron, ball milled cast iron has high strength, plasticity and toughness, high yield strength, yield strength ratio of 0.7-0.8, twice as high as steel, fatigue strength of nearly half of medium carbon steel, better wear resistance than non alloy steel, better castability than cast steel, and processing performance almost comparable to gray cast iron, so ball milled cast iron is more and more widely used in production. When casting ball milled iron castings, various defects such as sand holes, air holes and cracks will appear, and ball milled iron castings may also have defects such as wear and cracks in use. However, these defects can continue to be used after welding repair, avoiding waste, saving time and processing cost, so the welding repair of ball milled iron castings has higher economic benefits.
This paper analyzes the weldability of the ball milled cast iron, introduces the welding method of the ball milled cast iron, and discusses the welding process and operation points of the ball milled cast iron through the welding repair of the cracks (located on the cylinder wall between the cylinder body and the cooling water layer, the length of the cracks is about 300 mm) on the cylinder with QT600-3 material, 2.5 t weight and 28 mm wall thickness.
1、 Weldability analysis
The spheroidizing agent used in the melting of ball milled cast iron can hinder the graphitization and improve the hardenability of nodular cast iron. When welding nodular cast iron, the weld and semi fusion zone are more likely to form white structure, austenite is more likely to form martensite, the white tendency and hardening tendency of ball milled cast iron are larger than that of gray cast iron; the strength of nodular cast iron is higher, the plasticity and toughness are better, the properties of welded joint need to match with the base metal, and the mechanical properties of welded joint need to be higher than that of cast iron. Therefore, the weldability of ball milled cast iron is poor. When welding repair, it is not only necessary to select reasonable welding method and appropriate welding materials, but also to formulate reasonable welding process measures and operation measures.
2、 Selection of welding method
The common welding methods for repairing ball milled cast iron are homogeneous weld arc welding, heterogeneous weld arc welding and gas welding. Heterogeneous weld arc welding is mostly used for arc cold welding. Before welding, there is no need to preheat the weldment, which simplifies the welding process, reduces the welding cost, and improves the working conditions of the welding operator. Therefore, heterogeneous weld arc welding is used for the defects of the ball milled cast iron cylinder. Under the condition of arc cold welding, due to the large cooling rate of the welded joint, it is easy to produce white structure and the tendency of cracks. The main method of heterogenous weld arc welding is to improve the structure and performance of the joint by adjusting the chemical composition of the weld. Therefore, proper welding process and operation measures are needed to avoid welding cracks.
3、 Welding process
3.1 Preparation before welding
Before welding, sand, oil, rust and other impurities around the defect shall be removed to prevent the formation of air holes.
Try to find out the direction, branch and end point of the crack without omission. Drill a crack stopping hole about 0-6mm in front of the crack end to prevent the crack from continuing to expand when the groove is opened. Hole diameter of crack stop hole is φ 4-φ 6mm [2]. On the premise of smooth strip transportation and slag floating, narrow groove should be used to reduce weld metal and crack. The crack groove shall be processed with grinding wheel, chisel, air gouging gun and other tools as shown in Figure 1 (groove width is 20mm, depth is 15mm), and the groove surface shall be as smooth as possible.
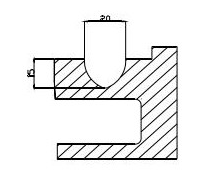
3.2 Welding materials and welding process parameters
Considering the strength requirements for welding materials and the processing requirements after welding, ezni Fe (Z408) is selected as the welding rod.
Use a small welding current. The low welding current can reduce the penetration, and the amount of carbon, sulfur, phosphorus and other impurities in the base metal entering the weld pool is less, so the tendency of hot cracking of the weld is reduced; because the carbon content in the weld is reduced, the tendency of hardening is reduced, and the tendency of cold cracking is reduced. The small welding current can also reduce the heat input of the joint, reduce the stress of the welded joint, reduce the width of the heat affected zone and the semi fusion zone, and improve the processing performance of the welded joint. Therefore, the electrode diameter is φ 3.2mm, the welding current is 90-100a, and the ezni Fe electrode is AC power.
4、 Key points of operation
First, adopt fast welding speed and short arc welding.
Second, short section, intermittent and scattered welding shall be adopted, and the weld shall be hammered immediately after welding.
With the growth of the weld, the tensile stress of the weld increases, and the tendency of the weld cracking increases accordingly, so the short section welding should be used. Short section refers to the short length of each weld. The length of the weld for thin-walled parts is 10-20 mm at a time, and the length of the weld for thick-walled parts is 30-40 mm at a time. Intermittent welding (when the welding joint is cooled to not hot (50-60 ℃), and then the next welding seam) can avoid the local high temperature and stress increase at the repair welding position. After welding, when the temperature of the weld is high and the plasticity is good, use a small hammer with round corner to hammer the weld rapidly until there are densely distributed pockmarks (the depth of pockmarks is about 0.5mm), so as to make the weld metal plastic deformation and reduce the weld stress. After each layer of welding, the slag shall be removed thoroughly. To avoid large horizontal stress, the weld bead shall be narrow and horizontal swing is not suitable.
Firstly, weld the crack edge with the skip welding method, as shown in Fig. 2, each section is about 30mm long, and the crack can not be sealed to avoid being pulled and cracked. Hammer the first layer of weld overlay. Then seal the crack on the hardfacing bottom layer, seal the end with the method shown in Fig. 3, then weld to the other side of the crack, and return to the crack edge on the same side for arc stopping, then start arc from the crack, and weld to the other side. In Fig. 3, 2 and 3 weld beads press the crack, but there is a certain slope in the forward direction, the fourth weld bead is welded at the slope, and a certain height is obtained. Each welding section is 10 mm long and shall be hammered immediately after welding.
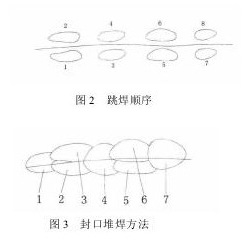
Third, Choose a reasonable welding sequence
In order to reduce the welding stress, a reasonable welding sequence is needed. Multi layer and multi pass welding adopts the welding sequence as shown in Figure 4.
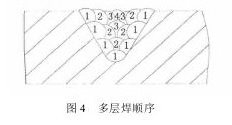