There are many types of gating system. For each kind of casting, it is necessary to design or select its mature type according to the casting requirements. Gating system can be divided into two categories according to the section proportion of each unit. Closed type: each section requires a cup > a straight > a cross > A, in this way, the liquid metal flow speed is faster, it is easy to fill the cavity, and the slag retaining capacity is stronger, but because of the fast speed, it is easy to splash. The scope of application is small wet cast iron parts and large and medium dry cast iron parts. Open type: each section requires a straight up > a straight down > a cross > a inside, which is a stable filling process and is not easy to fill the straight, cross and internal sprues, but it has little scouring on the inner wall of the cavity.
The casting schemes of nodular cast iron crankshaft can be roughly divided into four categories. By analyzing the advantages and disadvantages of different schemes, different casting schemes are selected to compare the results. In this paper, vertical pouring and horizontal cooling are selected for comparison.
(1) Vertical pouring and vertical cooling scheme: the rear end of the crankshaft is used as the internal gate, which is located at the highest point, and the riser is set at the same time. The internal gate passes through the riser, and then flows into the mold cavity from the riser. There are three types of vertical:
1) Top pouring type: the internal sprue is set at the top of the casting, the liquid metal flows into the cavity from the top, which is easy to fill the cavity, and it can well complete the sequential solidification from the bottom to the top, the feeding distance of the riser is far, and the pouring system is relatively simple and easy to clean. The crankshaft casting has many cranks and complex cavity. The top-down pouring method scours the inner wall seriously and is easy to splash. At the same time, slag inclusion, sand flushing, oxidation and other phenomena will occur.
2) Step type: set several more internal gates on the crankshaft. The filling process is relatively stable in this way, but the temperature of the upper part of the crankshaft will be higher than that of the lower part, the effect of feeding is not enough, and shrinkage will occur in the hot joint of the crankshaft.
3) Bottom pouring type: the inner gate is set at the lowest end of the crankshaft, and a slag collecting bag is set on the cross sprue of the pouring system. In this way, the liquid metal flow is relatively stable, which is good for discharging the gas in the mold cavity. However, the riser set at the upper end has a low temperature, which is not good for feeding, and it will produce shrinkage porosity at the hot spot.
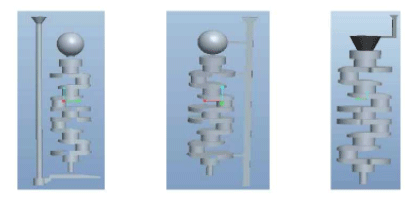
Conclusion: the advantage of vertical pouring and vertical cooling is that the riser is at the highest position and the pressure is relatively high, which is conducive to the casting feeding, but this way is difficult to mass production line, and the casting may have defects. Using this scheme to design pouring scheme one for simulation observation.
(2) Horizontal pouring and vertical cooling scheme: this port flows into the cavity again, which improves the temperature in the riser. When the pouring is finished, the gate is immediately blocked with sand, and then the mold is rotated 90 ° and cooled vertically. Because riser is higher than casting, it has better feeding effect. Some large-scale nodular cast iron crankshafts still adopt this scheme, but the operation is relatively heavy and the efficiency is low, so it is difficult to mass produce, so this scheme is not used.
(3) The disadvantages of this scheme are that the riser pressure is smaller than that of horizontal pouring and vertical cooling, and the feeding effect is general. But as long as we pay attention to control the composition of the original solution, pouring temperature, sand mold and mold hardness and other factors, we can eliminate the defects caused by shrinkage. Moreover, this scheme is simple in operation, high in production efficiency and suitable for mass production. Therefore, this paper chooses the horizontal pouring and horizontal cooling scheme,
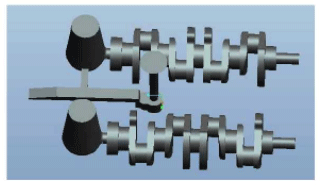