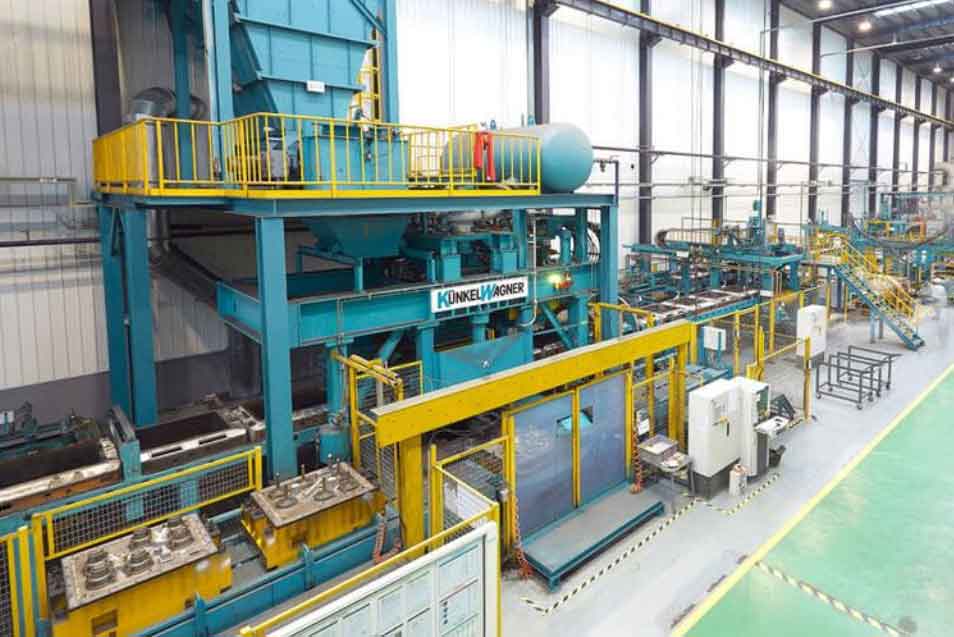
Navigating regulatory compliance is a critical challenge for ZHY Casting, particularly in the sand casting industry, where environmental and safety standards are stringent and vary significantly across different markets. Compliance not only ensures legal operations but also enhances the company’s reputation and customer trust. Here are key steps ZHY Casting can take to effectively manage regulatory compliance:
1. Understanding and Monitoring Regulatory Requirements
- Global and Local Laws: Stay informed about both international and local regulations that affect sand casting operations. This includes environmental protection laws, workplace safety regulations, and industry-specific standards.
- Continuous Monitoring: Establish a dedicated team or hire a compliance officer whose responsibilities include keeping up-to-date with regulatory changes and analyzing their impact on the company’s operations.
2. Implementing Compliance Management Systems
- Comprehensive System: Develop and implement a compliance management system that includes policy documentation, procedures, and controls designed to ensure all aspects of operations adhere to legal standards.
- Technology Integration: Utilize compliance software to track and manage requirements, document compliance activities, and trigger alerts for regulatory changes or non-compliance issues.
3. Employee Training and Engagement
- Regular Training: Conduct regular training sessions for employees at all levels to ensure they understand their roles in compliance and are aware of the latest regulations and practices.
- Culture of Compliance: Foster a corporate culture that prioritizes compliance and ethical behavior. Encourage employees to report non-compliance issues without fear of retaliation.
4. Auditing and Reporting
- Internal Audits: Perform regular internal audits to assess compliance with regulatory requirements and identify areas for improvement.
- External Audits: Engage external auditors periodically to validate compliance efforts and provide an unbiased view of the company’s adherence to legal obligations.
- Transparent Reporting: Maintain transparency by reporting compliance activities and outcomes to stakeholders, including regulatory bodies, customers, and shareholders.
5. Managing Supply Chain Compliance
- Supplier Standards: Ensure that suppliers and contractors also comply with relevant environmental and safety regulations. Incorporate compliance requirements into contracts and conduct regular supplier audits.
- Collaboration and Training: Work closely with suppliers to provide training and resources necessary to meet compliance standards.
6. Investing in Cleaner Technologies
- Eco-Friendly Materials: Invest in research and development to find eco-friendly alternatives to traditional sand and chemical binders used in sand casting that may be harmful or are heavily regulated.
- Waste Management Technologies: Improve waste management technologies to minimize environmental impact, focusing on recycling sand and reducing emissions from foundry operations.
7. Engaging with Regulatory Bodies and Industry Groups
- Proactive Engagement: Maintain an open dialogue with regulatory authorities and participate in industry forums. This can provide insights into regulatory trends and influence policy development.
- Compliance Advocacy: Participate in lobbying efforts to advocate for reasonable regulations that protect the environment and public health without imposing undue burdens on the industry.
By taking these steps, ZHY Casting can ensure that it not only complies with current regulations but is also well-prepared for future regulatory changes. Effective compliance management can enhance operational efficiencies, reduce legal risks, and improve the company’s market position by building trust with customers and the wider community.