The picture shows the filling state diagram of the gearbox case at different times, of which yellow is metal liquid. From the temperature contrast diagram on the right side, the temperature of the metal liquid can be roughly judged according to the color of the metal liquid, and the gray pattern is a foam pattern. From the diagram, it can be seen that when the 1.2s is in, the gate cup and the runner are filled up and the time used is shorter, because the gate cup and the runner are hollow. Without foam appearance, there is no resistance like the cavity in sand casting, so the metal liquid has good fluidity and fast filling. At 17.8s, the molten metal is just filled with the inner runner. It can be seen that the existence of the foam pattern will reduce the fluidity of the molten metal. When the foam pattern and metal liquid react, it will take away the heat of the molten metal and reduce the temperature of the molten metal, thereby reducing the fluidity of the molten metal and increasing the filling time. The mold filling of the whole lost foam casting casting was completed at 34.8s.
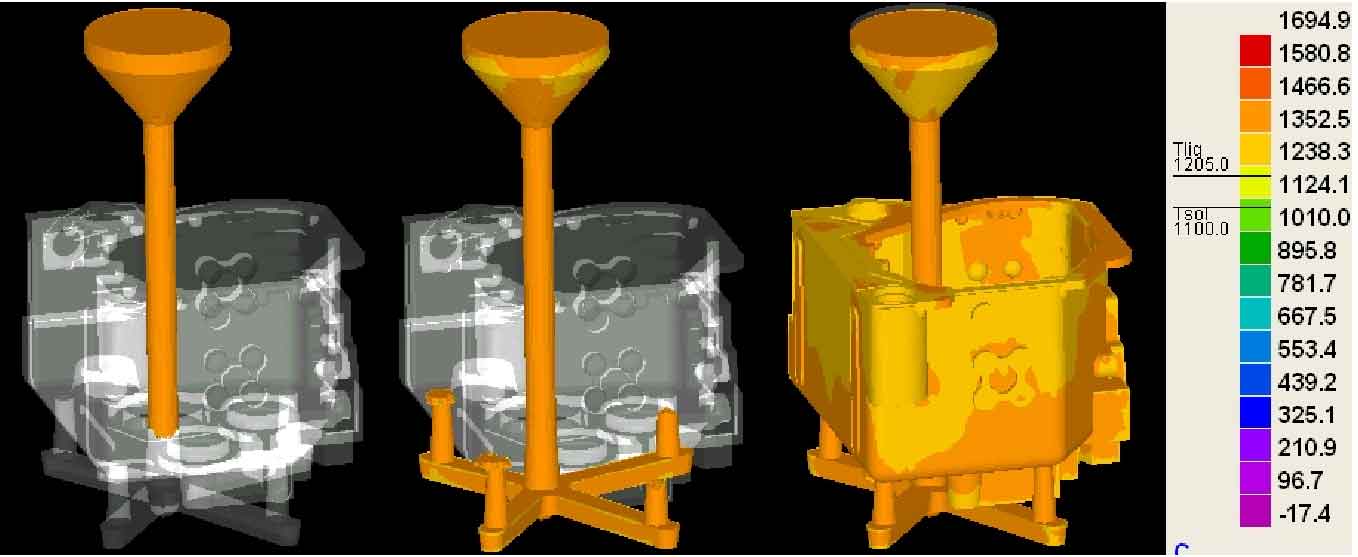
As it is a bottom casting gating system, it can be seen from the figure that after filling the sprue, the molten metal will fill the mold evenly to the surrounding transverse sprue, and then fill the mold to the inner sprue. It can be seen from the diagram that the inner gate is evenly distributed around the bottom of the box, so the metal liquid is filled from the bottom of the box and filled with the whole lost foam casting from bottom to top. The temperature of lost foam casting is low and high, which is conducive to sequential solidification. The filling time of the whole lost foam casting is 34.8s.