The shell of the water ring vacuum pump used by ZHY Casting is welded with steel plates and processed into shape. It is washed by water and sand for a long time in the process of use. The shell of the water ring vacuum pump leaks, causing the low pressure of the whole vacuum system, affecting the production efficiency and quality of the vacuum pump shell castings. Therefore, it is decided to use nodular cast iron to produce vacuum pump shell castings to improve the service life of vacuum pump shell.
The overall dimension of the vacuum pump shell casting is large, and the maximum overall dimension of the casting is φ 864 mm × 637 mm, the wall thickness of the casting barrel is 35mm, the single weight of the casting is 425 kg, the outline structure diagram is shown in Figure 1, the material brand is QT600-3, and the technical requirements are that the vacuum pump shell casting shall not leak. The size of sand box is 1200 mm × 1 000 mm × 1300 mm, one piece for one box, casting the vacuum pump shell with a box weight of 560 kg, using 700kg spheroidizing ladle to cast the molten iron, and using the wire feeding method for spheroidizing treatment. The pouring temperature of molten iron is set at 1430~1450 ℃, and the vacuum negative pressure is controlled at -0.05~-0.06 MPa. In order to prevent the deformation of the vacuum pump shell casting, the pressure holding time after molten iron pouring is set at 1 h.
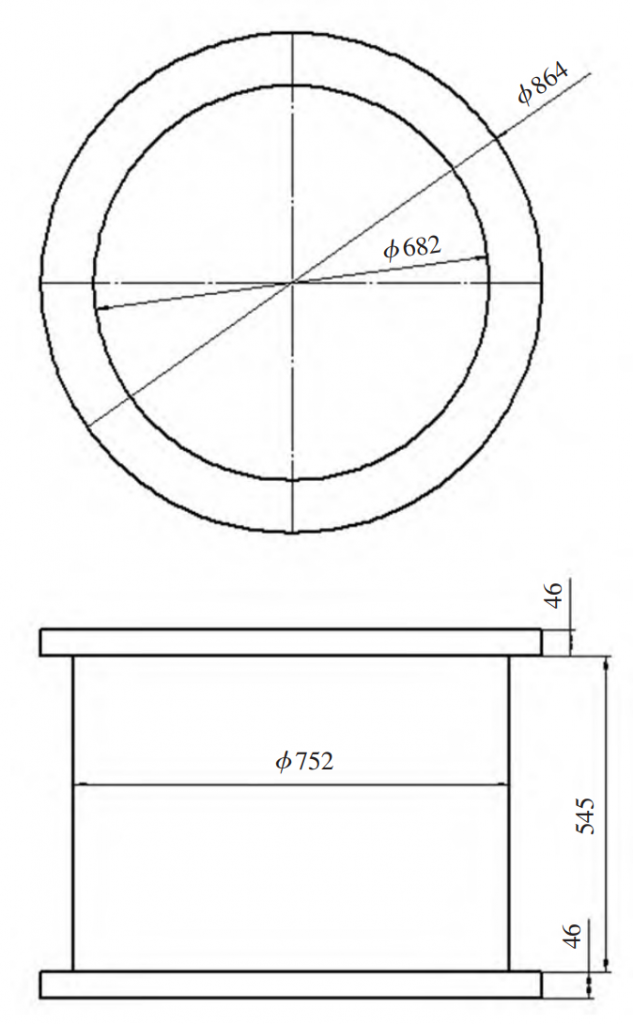
The top pouring and semi open pouring system is adopted, and the sprue ratio is Σ F straight: Σ F horizontal: Σ F inside =1:1.4:1.2, sprue section size φ 50 mm, cross section size of runner 75 mm × 75 mm, the section size of the ingate is 40 mm × 140 mm, riser Size 120 mm × 120 mm × 14mm, the risers are evenly distributed on the top of the vacuum pump shell casting. The lost foam casting process is shown in Figure 2. Because the external chill is inconvenient to be arranged in the lost foam casting process, and the internal chill will cause poor fusion, the riser feeding process is used to eliminate the shrinkage cavity or porosity of the vacuum pump shell casting. Six risers are placed on the top of the vacuum pump shell casting, of which two are hot risers, and the molten iron enters the mold cavity from the hot risers, First fall into the bottom of the cavity, and then the liquid iron level rises. When the liquid iron is filled to the top of the cavity, the front liquid iron enters the other four risers. After the liquid iron is filled, the six risers jointly feed the vacuum pump shell casting.
(1) It is feasible to produce thick nodular cast iron vacuum pump shell by lost foam casting process. The white mold is cut and divided by numerical control and bonded by manual combination. The vacuum pump shell casting has high dimensional accuracy and is suitable for small batch production.
(2) The molten iron adopts the double wire feeding spheroidization process of cover and package, which ensures the wire feeding quality of molten iron and realizes the material requirements of vacuum pump shell castings.
(3) The lost foam casting process adopts the top pouring and riser feeding process, which realizes the stable and orderly solidification of the mold filling process. The vacuum pump shell casting is dense without shrinkage and leakage, which meets the requirements of customers.