The figure below shows the simulation results of the pressure field distribution of molten metal at the completion of pouring. In the process of horizontal centrifugal casting, the distribution of pressure field is basically concentric when the molten metal just fills the mold. The magnitude of pressure is directly related to the diameter of the inner hole of the mold, the wall thickness of the horizontal centrifugal casting of cylinder liner and the centrifugal speed. Centrifugal speed is very important to the mold filling process of castings. Theoretically, even if the rotational speed of the die is relatively low, a uniform cylinder can be obtained finally. But in fact, only when the mold speed reaches the critical value, the molten metal will be collected. At the optimal rotation speed, the liquid metal is firmly attached to the inner wall of the mold to form a liquid column with uniform thickness, which rotates with the mold and finally solidifies:
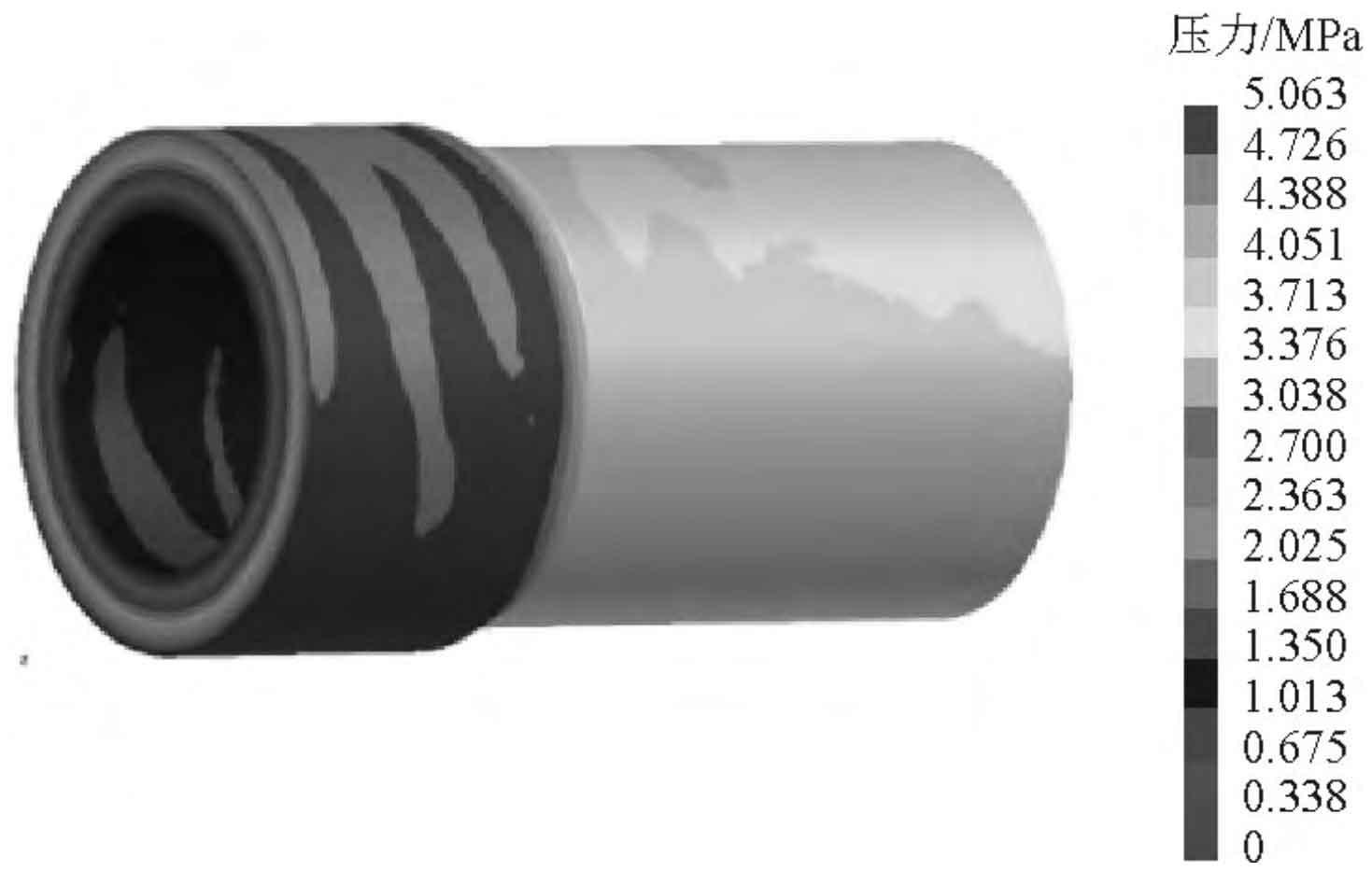
Where, f is centrifugal force, N; M is the mass, G; W is the angular velocity, w = 2 π NR; R is the radius.
It can be seen that the rotating speed w directly affects the centrifugal force of molten metal. When the rotating speed is too low, the centrifugal force generated is insufficient, which is not conducive to the normal mold filling flow of molten metal. When the speed is too high, it will also have many adverse effects. On the one hand, the higher the rotating speed is, the greater the viscosity of the liquid metal is, and the alloy elements with different quality in the liquid metal will produce serious segregation, and the metal with higher quality will be closer to the outer surface of the horizontal centrifugal casting of the cylinder liner; On the other hand, too high rotating speed will produce high tensile stress on the periphery of the horizontal centrifugal casting of the cylinder liner, and eventually lead to longitudinal cracks. From the perspective of energy consumption, the higher the speed is, the more kinetic energy needs to be provided by the centrifuge. When the speed exceeds the speed range where the liquid metal can be normally filled, it will lead to a waste of energy.
In addition, the pressure of molten metal at different thickness parts is different, and the pressure on the outer surface is always greater than that on the inner surface, which is related to the wall thickness of the horizontal centrifugal casting of the cylinder liner. The pressure is distributed in a gradient in the radial direction, and the maximum pressure difference can reach 0.317mpa; The pressure at the thick wall of the horizontal centrifugal casting of the cylinder liner is also greater than that at the thin wall. The pressure difference between the thick wall and the outer surface of the thin wall is 0.097mpa. This is because the centrifugal force increases with the increase of the radius. The radius of the outer surface is greater than that of the inner surface, and the radius of the thick wall is greater than that of the thin wall. However, due to the influence of the front and rear baffles of the mold, the pressure distribution of the molten metal in the axial direction is not uniform. Under the combined action of centrifugal force and mold constraint, the liquid metal will move to the front and rear cover plates. Because the inlet position is closer to the left side of the mold, the liquid metal first contacts the left end of the mold, resulting in greater pressure on the liquid metal at the left end than on the right end. It can be found that if the rotating speed is too high, the liquid metal is easy to gather at both ends of the mold, resulting in defects such as insufficient filling and internal surface depression in the middle of the horizontal centrifugal casting of the cylinder liner. Therefore, the centrifugal speed should be selected within a reasonable range. In the radial direction, due to the influence of gravity, the pressure field presents an irregular concentric circle, and the liquid metal above the horizontal centrifugal casting of the cylinder liner will produce pressure on the liquid metal below. Therefore, the pressure at the lower part of the horizontal centrifugal casting of the cylinder liner is slightly greater than the pressure at the upper part, and the pressure difference is 0.023mpa. Under the condition of low-speed rotation of the mold, this effect can not be ignored. This effect is small under the condition of high-speed rotation of the mold. From the distribution of pressure field, it can be seen that the pressure of molten metal in centrifugal casting process is very high, up to 0.5063mpa, which makes the feeding capacity of molten metal stronger. Centrifugal force has the greatest influence on the pressure field distribution of horizontal centrifugal casting of cylinder liner. The farther away from the rotation center, the greater the centrifugal feeding pressure, the higher the density of horizontal centrifugal casting of cylinder liner, and the better the mechanical properties.