Because the filling process of the curved blade of the impeller in investment casting is very unstable and easy to cause turbulence, the casting defects such as insufficient pouring, cold shut, air hole, shrinkage porosity and shrinkage cavity are generated. Therefore, it is very important to design the matching pouring system.
According to the structural characteristics of the impeller investment casting, the vertical top-pouring method is adopted, which is conducive to achieving smooth mold filling from bottom to top and sequential solidification from inside to outside. An annular riser is set at the center of the top, an open riser is set at the far end of each blade, and five internal gates are set at the same time to improve the floating speed of the alloy liquid in the mold cavity, so that the impurities in the molten liquid and the gas in the model can quickly gather in the degassing riser, so as to obtain the impeller investment casting with excellent internal quality.
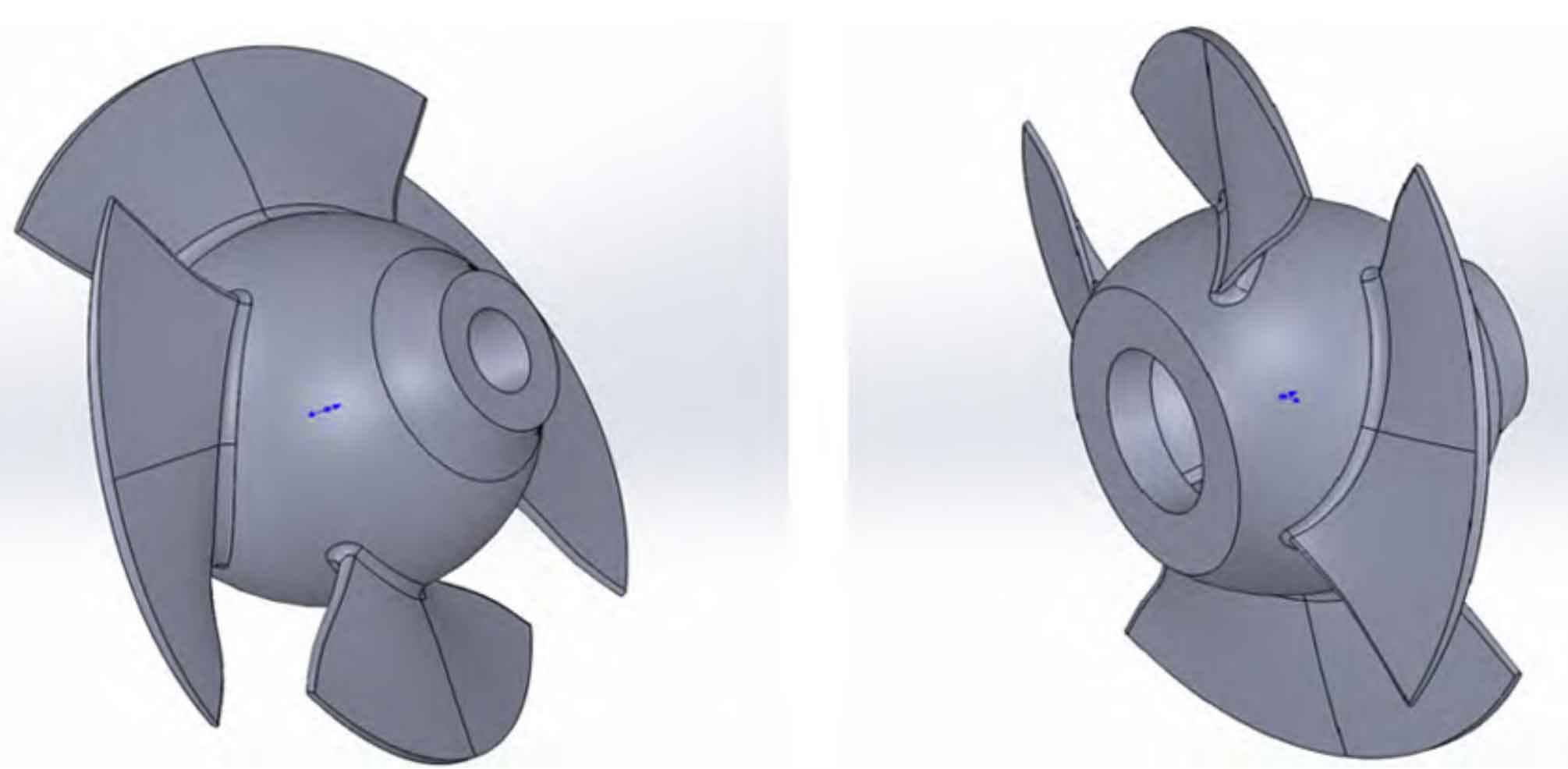
From the near end of the blade to the far end of the blade, vent holes are opened in order to enhance the exhaust of the mold and avoid casting defects due to local gas enrichment.