Integrated lightweight design, low-cost batch manufacturing and increasingly complex structural characteristics have become the unified trend of the development of aerospace military equipment at home and abroad. The traditional sand casting can not achieve the precise forming of complex components; Metal mold casting and V-process casting are currently only suitable for mass production of simple components (annular structure, conical structure, frame beam structure, etc.); Although die casting (high pressure) is widely used in the field of rail transit, its internal structure is better than other forming processes. Loose and serious porosity defects; Due to the low thermal conductivity of gypsum mold casting, the overall mechanical properties of the product are not high; Based on the comprehensive mass production cost, product production cycle, and structure precision forming, compared with various solidification forming manufacturing processes, investment casting is the best matching forming process. At the same time, the two-way lightweight design of material weight reduction and structure weight reduction of structural components can be realized through material system selection.
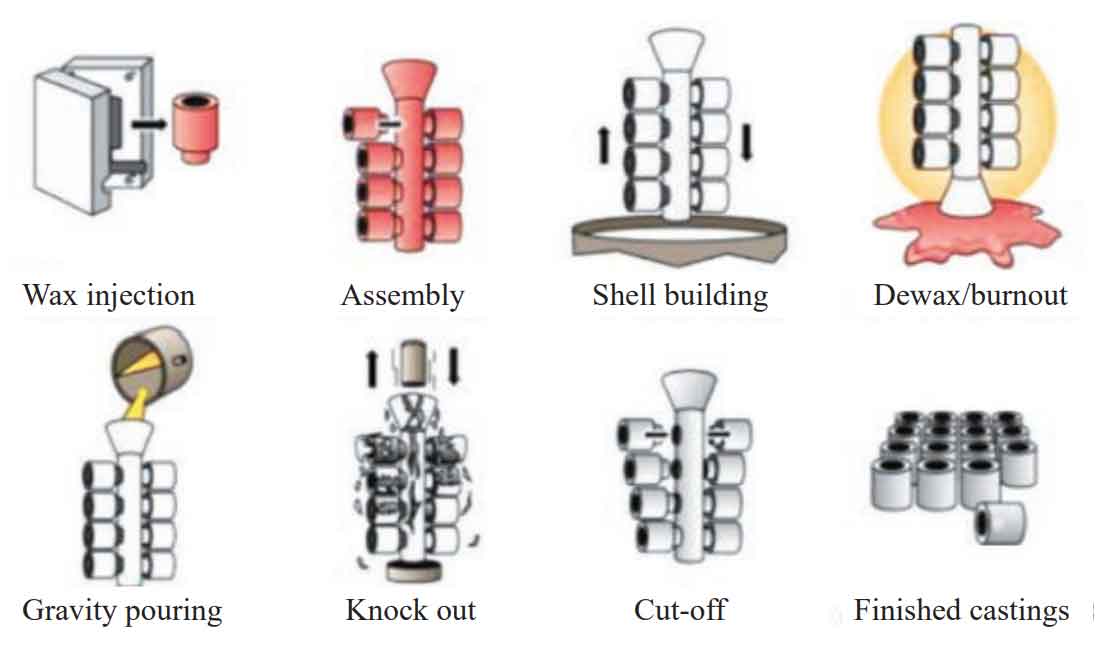
The investment casting process route is shown in the figure. The structure, properties and appearance dimensions of products are controlled by the manufacturing process and precision forming process. On the basis of traditional theories and process methods, the current investment casting technology, combined with advanced technologies such as numerical simulation calculation and analysis, soluble core materials, automatic control of equipment, and laser additive manufacturing, is developing towards the direction of “temperature – tissue – stress and strain” theory guidance, automatic control of production process, and integrated integrated manufacturing precision forming. High-temperature alloy, titanium alloy, aluminum alloy and magnesium alloy are the preferred metal material systems for complex service environment and lightweight manufacturing in the field of aerospace and military equipment, which play a major bearing role. The organizational performance, structural dimension and service life of the manufactured products directly determine the service life, manufacturing cost, structural reliability, weight design coefficient and other performance indicators of the weapon equipment. Therefore, investment casting technology is the technical foundation support for the development direction of long-life, low-cost, lightweight and precision forming of products in advanced aerospace weapons and equipment, commercial aerospace, civil aviation and other fields.
In China, the current development of investment casting technology has important strategic significance for the construction of “two special projects (aero-engine and gas turbine)”. China has clearly put forward the development roadmap of key models such as large bypass ratio turbofan aero-engine, F class and G/H class heavy-duty gas turbine. The development of the corresponding high-temperature turbine blades, large integrally cast casing and other difficult investment precision castings will be an important prerequisite for the success of the model.