Sand casting is a popular method of producing metal parts due to its cost-effectiveness and versatility in creating complex shapes. However, like other casting processes, it is not without its challenges, one of the most common being porosity. This article will explore the causes of porosity in sand casting, its effects on the quality of the final product, and strategies for preventing it.
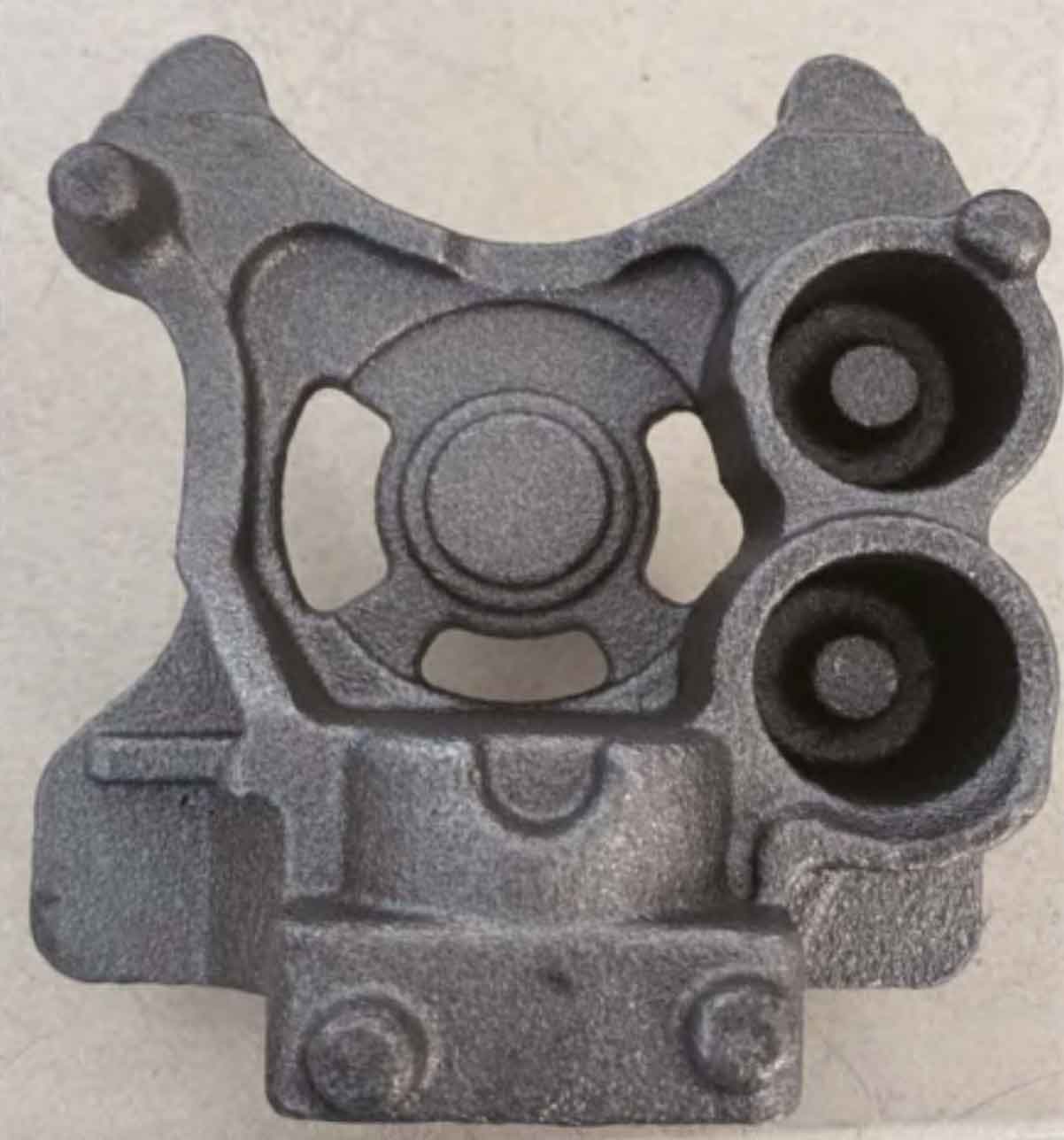
Understanding Porosity: Porosity in sand casting is the formation of small voids or pores within the metal casting. These voids can occur either on the surface or internally, and they can significantly affect the mechanical properties and appearance of the final product. Porosity can lead to reduced strength, fatigue resistance, and can also cause cosmetic defects.
Causes of Porosity:
Several factors can contribute to the formation of porosity in sand castings. These include:
- Gas Entrapment: If the molten metal traps gases during the pouring process, these gases can form bubbles that become pores when the metal solidifies.
- Shrinkage: As the molten metal cools and solidifies, it contracts. If this contraction is not compensated for, it can lead to the formation of voids.
- Inadequate Venting: If the sand mold is not properly vented, gases produced during the casting process can be trapped inside, leading to porosity.
Preventing Porosity:
There are several strategies that can help prevent porosity in sand castings:
- Proper Gating and Venting: Designing the gating system to promote smooth and uninterrupted flow of molten metal can help prevent gas entrapment. Additionally, providing adequate venting in the mold can help gases escape instead of being trapped inside.
- Controlled Pouring: The temperature and speed of pouring can influence gas entrainment. Pouring at the right temperature and at a controlled speed can help minimize turbulence and reduce the risk of porosity.
- Use of Risers: Risers can provide additional molten metal to compensate for shrinkage during solidification. They should be designed and placed correctly to be effective.
- Gas Control: Controlling the gas content of the molten metal and the molding sand can help reduce gas-related porosity. This can involve using degassing agents or methods to reduce gas content in the molten metal, and ensuring the molding sand is not overly moist.
While porosity is a common issue in sand casting, understanding its causes and implementing strategies to prevent it can significantly improve the quality of the final product. By employing proper gating and venting, controlled pouring techniques, effective use of risers, and gas control, manufacturers can produce high-quality, porosity-free sand castings.