Porosity is a prevalent issue in sand casting, characterized by the presence of voids or pores within the cast part. These pores, resulting from gas entrapment or shrinkage during solidification, can compromise the strength, durability, and aesthetics of the casting. This article explores effective strategies for mitigating porosity issues in sand casting.
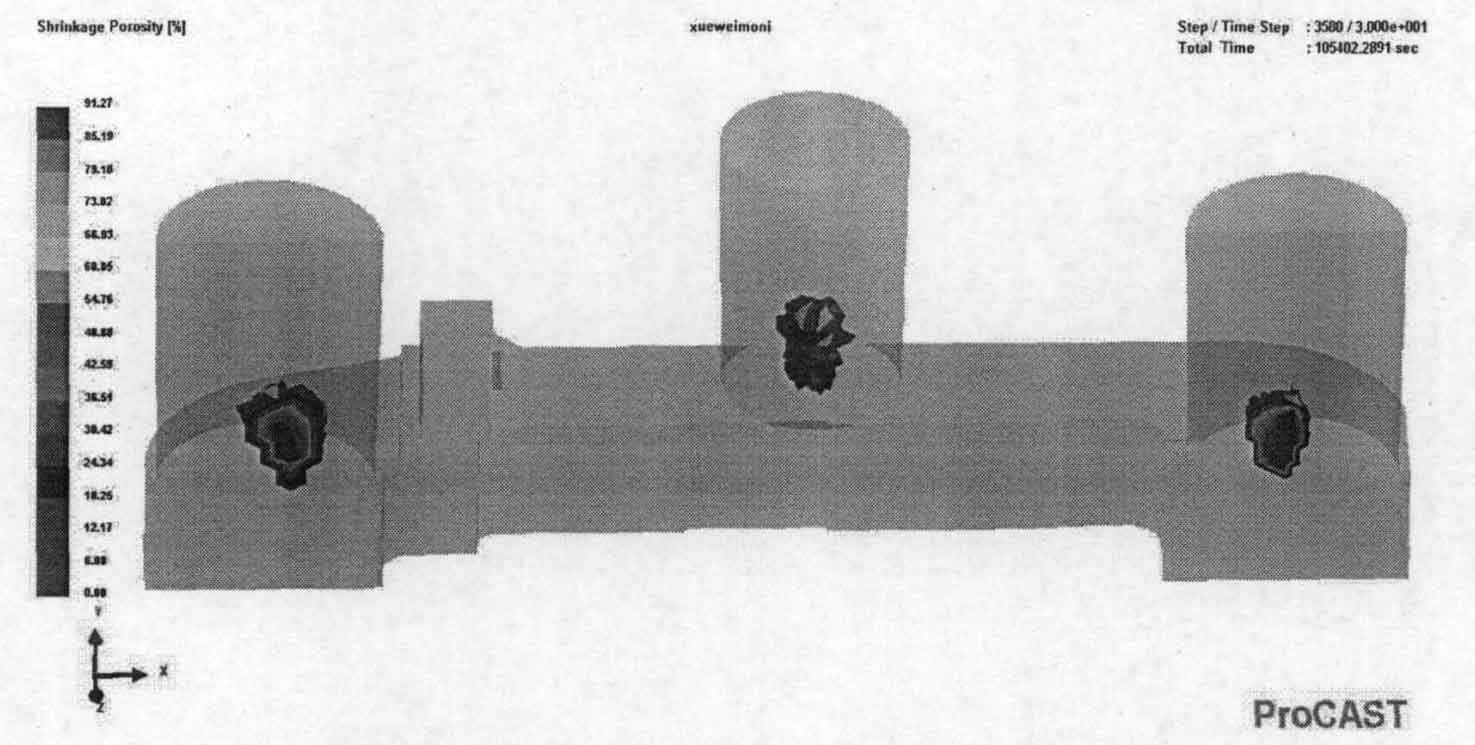
Understanding the Implications of Porosity: The porosity of a cast part can significantly undermine its performance. Porous castings typically exhibit reduced tensile strength, compromised structural integrity, and lower resistance to fatigue and corrosion. Furthermore, porosity can cause cosmetic defects, impacting the casting’s overall appearance and its suitability for certain applications.
Strategies for Mitigating Porosity in Sand Casting:
- Optimized Mold Design: Proper mold design plays a critical role in minimizing porosity. Incorporating an effective gating and venting system ensures smooth, uninterrupted flow of molten metal, preventing gas entrapment. The mold design should also consider shrinkage during solidification, using risers to supply additional molten metal and compensate for volume reduction.
- Controlled Pouring Techniques: The pouring process can directly impact the occurrence of porosity. Pouring molten metal at the appropriate temperature and rate can prevent turbulence that may trap gas within the casting. A steady and calculated pour is crucial in achieving a high-quality, non-porous casting.
- Gas Control: Elevated gas levels in the molten metal or the molding sand can lead to porosity. It’s essential to monitor and control gas content, possibly by using degassing agents or techniques for the molten metal, and ensuring the molding sand’s moisture content is optimal.
- Effective Use of Risers: Risers serve as reservoirs of molten metal, feeding the casting as it solidifies and shrinks. Proper riser design and placement can significantly mitigate shrinkage-related porosity.
- Quality Control and Inspection: Employing rigorous quality control measures can help identify and address porosity issues early. Non-destructive testing methods, such as radiographic or ultrasonic inspection, can detect internal porosity, enabling corrective action before the casting reaches the end-user.
Porosity can pose significant challenges in sand casting, impacting the quality and performance of the cast part. However, by understanding the causes of porosity and implementing effective mitigation strategies, foundries can significantly reduce porosity issues. Through optimized mold design, controlled pouring techniques, gas control, effective use of risers, and stringent quality control measures, it’s possible to produce high-quality, low-porosity sand castings.