Ductile iron casting, also known as nodular or spheroidal graphite iron casting, is a manufacturing process that offers numerous benefits in terms of efficiency and durability. This article explores how ductile iron casting enhances efficiency and durability in component production, highlighting its advantages and applications in various industries.
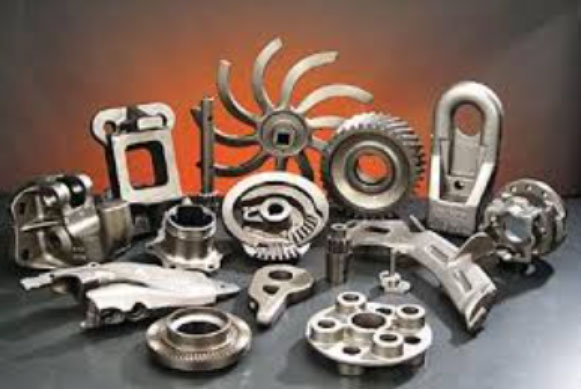
- Design Flexibility: Ductile iron casting allows for greater design flexibility compared to other materials. Its ability to be cast into complex shapes and intricate geometries provides engineers and designers with the freedom to create components that meet specific requirements. This flexibility enables the production of optimized designs that maximize performance and functionality.
- High Efficiency in Mass Production: Ductile iron casting is a highly efficient method for mass production. It allows for the simultaneous production of multiple components using reusable molds, reducing production time and cost per unit. The ability to produce large quantities of components efficiently makes ductile iron casting suitable for industries with high production demands, such as automotive, machinery, and construction.
- Excellent Strength-to-Weight Ratio: Ductile iron casting offers a high strength-to-weight ratio, providing a balance between strength and weight reduction. This advantage is particularly valuable in industries where weight reduction is critical, such as automotive and aerospace. Components made from ductile iron casting can be lighter without sacrificing strength, leading to improved fuel efficiency and overall performance.
- Superior Durability and Longevity: Ductile iron casting exhibits exceptional durability and longevity, making it suitable for demanding applications. It can withstand harsh operating conditions, including high temperatures, heavy loads, and corrosive environments. The inherent strength and toughness of ductile iron casting ensure that components have a longer service life, reducing the need for frequent replacements and maintenance.
- Resistance to Fatigue and Fracture: Ductile iron casting has excellent resistance to fatigue and fracture. The presence of graphite nodules in the microstructure acts as stress relievers, preventing the propagation of cracks and enhancing the material’s resistance to cyclic loading. This property makes ductile iron casting ideal for applications subjected to repeated stresses or dynamic loads.
- Cost-Effective Production: Ductile iron casting offers cost-effective production compared to alternative manufacturing processes. The lower material and production costs, combined with its high efficiency in mass production, contribute to overall cost savings. This cost-effectiveness is a significant advantage for manufacturers aiming to optimize their production processes and reduce expenses without compromising on quality.
- Versatile Applications: Ductile iron casting finds diverse applications across industries. It is commonly used in automotive components such as engine blocks, transmission parts, and suspension components. It is also utilized in machinery, pumps, valves, pipes, and structural elements in industries such as construction, mining, agriculture, and more.
Ductile iron casting enhances efficiency and durability in component production through its design flexibility, high efficiency in mass production, strength-to-weight ratio, durability, resistance to fatigue and fracture, and cost-effectiveness. Its versatile applications in various industries highlight its importance in enhancing the performance, reliability, and longevity of components. Manufacturers can leverage the benefits of ductile iron casting to achieve efficient and durable component production, contributing to the overall success of their operations.