Steel castings manufacturers have to constantly adapt to changing industry demands in order to remain competitive and meet the evolving needs of their customers. Here are some ways in which steel castings manufacturers adapt to changing needs:
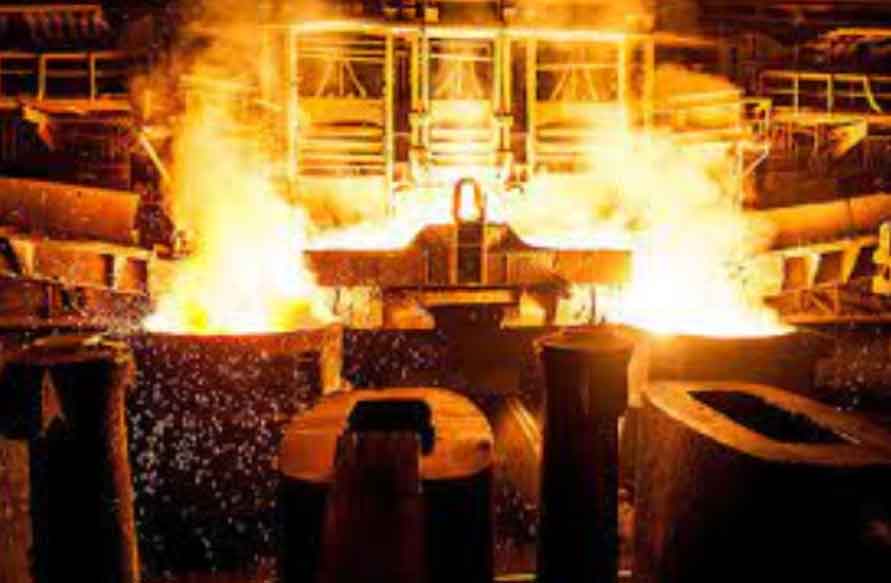
- Advanced Manufacturing Technologies: Manufacturers invest in advanced technologies such as computer-aided design (CAD), computer-aided manufacturing (CAM), and simulation software to optimize their casting processes. These technologies enable faster product development, improved accuracy, and reduced lead times.
- Customization and Flexibility: Steel castings manufacturers understand the importance of customization to meet specific customer requirements. They offer flexible solutions and work closely with customers to develop castings that meet their unique needs. This may involve creating new molds, modifying existing ones, or developing specialized alloys.
- Material Development: As industry demands change, steel castings manufacturers invest in research and development to develop new materials or improve existing ones. This could involve the development of high-strength alloys, corrosion-resistant materials, or materials with specific characteristics like heat resistance or wear resistance.
- Process Optimization: To meet changing demands, manufacturers focus on optimizing their casting processes. They invest in process automation, implement lean manufacturing principles, and employ statistical process control techniques to improve efficiency, reduce waste, and ensure consistent quality.
- Collaborative Approach: Steel castings manufacturers collaborate with their customers and other stakeholders in the supply chain to better understand market trends and customer needs. This collaborative approach helps them align their capabilities and resources to meet the changing demands effectively.
- Continuous Training and Skill Development: Manufacturers invest in training and skill development programs for their employees to keep them updated with the latest technologies, techniques, and industry trends. This ensures that the workforce is equipped to handle changing demands and adopt new manufacturing methods.
- Quality Assurance and Certifications: Steel castings manufacturers focus on maintaining stringent quality control measures to meet industry standards and customer expectations. They obtain relevant certifications such as ISO 9001 to demonstrate their commitment to quality. Additionally, they may invest in in-house testing facilities or collaborate with third-party testing labs to ensure the quality of their castings.
- Sustainability and Environmental Responsibility: With increasing emphasis on sustainability, manufacturers adapt their processes to minimize waste, reduce energy consumption, and lower their environmental impact. They may adopt cleaner production technologies, implement recycling programs, and work towards achieving sustainable certifications.
- Market Diversification: Manufacturers explore new markets and industries to diversify their customer base and reduce dependence on a single sector. This enables them to adapt to changing demands in specific industries and mitigate risks associated with market fluctuations.
By adopting these strategies, steel castings manufacturers can effectively adapt to changing industry demands and remain competitive in the market.