Die casting and investment casting are two commonly used manufacturing processes for producing complex metal parts. While both methods involve the casting of molten metal, there are significant differences between them. Let’s compare die casting and investment casting in terms of their process, capabilities, advantages, and disadvantages:
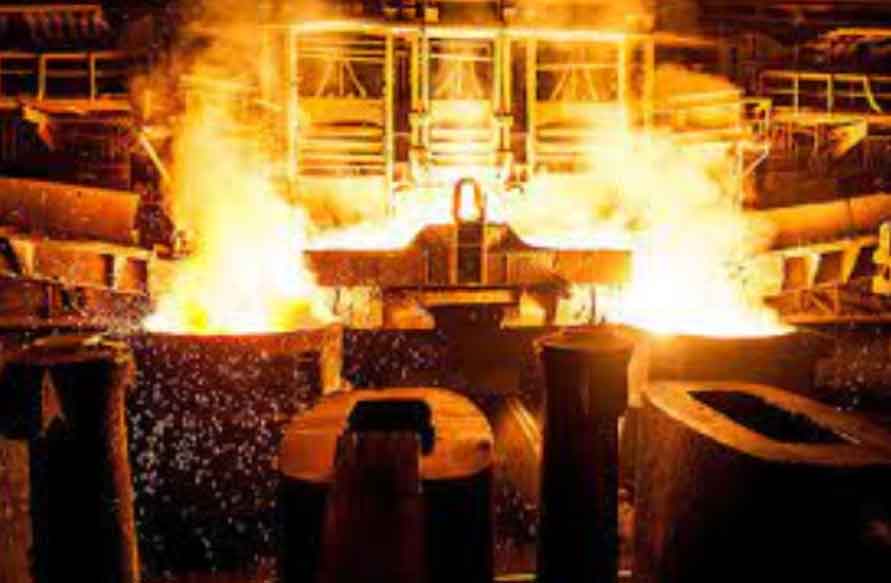
Die Casting:
- Process: Die casting involves injecting molten metal, typically non-ferrous alloys like aluminum, zinc, or magnesium, into a reusable steel mold called a die. The mold is designed with the shape and features of the desired part.
- Complexity: Die casting is suitable for producing parts with intricate details, thin walls, and complex shapes. It allows for tight dimensional tolerances and repeatability.
- Speed: The die casting process is generally faster compared to investment casting, as the molten metal is injected under pressure into the die, which enables rapid solidification.
- Surface Finish: Die casting offers excellent surface finish and can achieve smooth, polished, and visually appealing surfaces without the need for additional post-processing.
- Volume Production: Die casting is well-suited for high-volume production runs. Once the die is made, it can produce a large number of parts with consistent quality and dimensional accuracy.
- Material Options: Die casting is primarily used for non-ferrous alloys such as aluminum, zinc, and magnesium. These materials offer good strength-to-weight ratios and are commonly used in various industries.
Investment Casting:
- Process: Investment casting, also known as lost-wax casting, involves creating a wax pattern of the desired part, coating it with a ceramic shell, and then melting away the wax to leave a hollow mold. Molten metal, usually ferrous or non-ferrous alloys, is poured into the mold to create the final part.
- Complexity: Investment casting is capable of producing highly complex parts with intricate details, undercuts, and thin walls. It allows for near-net-shape production, reducing the amount of machining required.
- Surface Finish: Investment casting provides excellent surface finish and dimensional accuracy. It produces parts with smooth surfaces, and post-processing can achieve even finer finishes if necessary.
- Material Options: Investment casting supports a wide range of materials, including both ferrous and non-ferrous alloys. It is often preferred for casting stainless steel, superalloys, and other high-performance materials.
- Design Flexibility: Investment casting allows for greater design flexibility, as it can produce parts with complex geometries, internal cavities, and thin sections that may be challenging with other casting methods.
- Batch Production: Investment casting is well-suited for small to medium production runs, making it ideal for custom or low-volume manufacturing applications.
Advantages of Die Casting:
- High production speed and efficiency.
- Excellent dimensional accuracy and repeatability.
- Suitable for high-volume production.
- Wide range of material options.
- Smooth surface finish without additional post-processing.
Disadvantages of Die Casting:
- Limited complexity compared to investment casting.
- Higher tooling and setup costs.
- Not ideal for extremely high-temperature alloys.
Advantages of Investment Casting:
- Capable of producing highly complex parts.
- Excellent surface finish and dimensional accuracy.
- Wide range of material options, including high-performance alloys.
- Design flexibility for intricate geometries.
- Suitable for small to medium production runs.
Disadvantages of Investment Casting:
- Longer production cycle compared to die casting.
- Higher costs for tooling and mold-making.
- More labor-intensive process.
- Not as suitable for high-volume production.
Die casting and investment casting are both valuable manufacturing processes but with distinct characteristics. Die casting excels in high-volume production of complex parts with fast cycle times, while investment casting is preferred for producing intricate and complex parts with excellent surface finish and design flexibility, although it is more suitable for small to medium production runs.
The choice between die casting and investment casting depends on various factors, including the complexity of the part, desired production volume, material requirements, and cost considerations. If you need high-volume production of parts with tight tolerances and fast turnaround times, die casting may be the preferred option. On the other hand, if you require intricate and highly detailed parts with superior surface finish and design flexibility, investment casting would be a better choice.
It’s worth noting that advancements in both processes, such as the use of computer-aided design and manufacturing (CAD/CAM), simulation tools, and improved materials, have expanded their capabilities and narrowed the gaps between them. Additionally, alternative casting methods like sand casting, gravity casting, and pressure die casting may be suitable for specific applications, depending on the requirements.
Ultimately, the selection between die casting and investment casting should be based on a comprehensive evaluation of the specific project’s needs, considering factors such as part complexity, volume, material, surface finish requirements, and cost considerations.