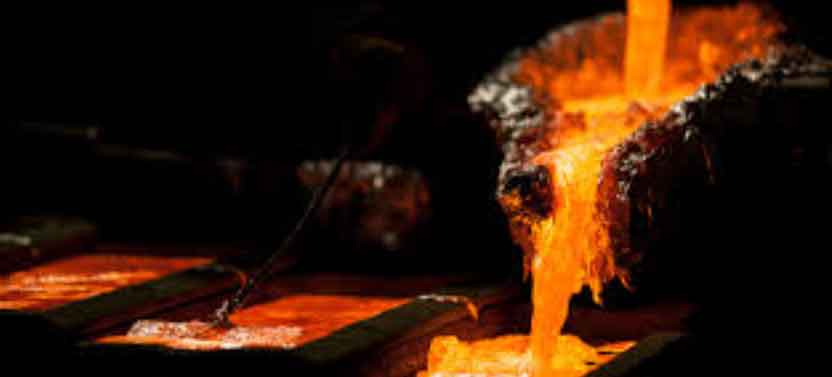
Sand casting is indeed a time-tested technique that has been used for centuries to craft metal components. It is one of the oldest and most versatile casting processes, offering numerous advantages for the production of various objects, from small intricate parts to large industrial components. Here are some key features and benefits of sand casting:
Versatility:
Sand casting is highly versatile and can be used to produce complex shapes with intricate details. It allows for the creation of both small and large components, making it suitable for a wide range of applications across different industries.
Cost-effectiveness:
Sand casting is a relatively cost-effective casting method compared to other processes. The materials used in sand casting, such as sand, clay, and binders, are relatively inexpensive. Additionally, the reusable nature of the molds and patterns reduces production costs in the long run.
Wide Material Selection:
Sand casting supports a wide range of metals and alloys, including aluminum, iron, steel, brass, bronze, and more. This enables manufacturers to select the most suitable material for the desired application, considering factors like strength, durability, and corrosion resistance.
Complex Geometries:
Sand casting can accommodate complex shapes, including undercuts, thin walls, and varying thicknesses. The flexibility of sand molds allows for the production of intricate features and internal cavities, which may be challenging with other casting methods.
Customization and Prototyping:
Sand casting allows for easy modification of patterns and molds, making it ideal for customization and prototyping purposes. Adjustments can be made quickly, enabling manufacturers to iterate designs and refine prototypes before final production.
Reproducibility:
Sand casting offers good reproducibility, meaning that multiple identical castings can be produced from the same pattern and mold. This is especially advantageous for mass production, where consistent quality and dimensional accuracy are essential.
Heat Resistance:
Sand molds have excellent heat resistance, making sand casting suitable for casting high-temperature metals and alloys. It can withstand the extreme temperatures of molten metal during the pouring process without deforming or deteriorating.
Environmental Friendliness:
Sand casting is relatively environmentally friendly compared to other casting processes. The sand used in the molds is reusable, reducing waste generation. Additionally, the binders used in the sand mixture are often derived from organic or eco-friendly sources.
Craftsmanship and Artistry:
Sand casting has an inherent artistry and craftsmanship associated with it. Skilled pattern makers and foundry workers bring their expertise to create intricate patterns, molds, and castings. The process showcases the art of shaping metal and requires a blend of technical skill and creativity.
Despite advancements in other casting methods, sand casting remains widely used in various industries, including automotive, aerospace, machinery, and art foundries. Its time-tested reliability, cost-effectiveness, and ability to produce complex components continue to make it a valuable technique for crafting metal objects.