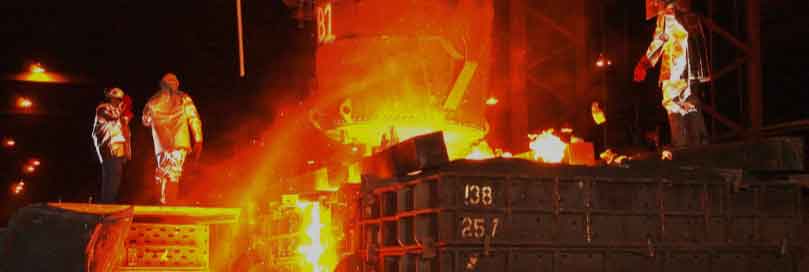
Foundry technology plays a crucial role in optimizing production processes and maximizing productivity in various industries. Foundries are specialized facilities where metal casting takes place, and they employ advanced techniques to transform raw materials into finished products. Here are several ways in which foundry technology optimizes production processes:
Process Automation:
Foundries utilize automation technologies to streamline production processes and reduce manual labor. Automated systems can perform tasks such as mold preparation, material handling, pouring molten metal, and even inspection. By automating repetitive and labor-intensive tasks, foundries can achieve higher production rates, reduce human error, and improve overall productivity.
Advanced Casting Techniques:
Foundry technology employs advanced casting techniques like investment casting, die casting, sand casting, and continuous casting. Each technique has its advantages depending on the specific application. These techniques allow for precise control over the metal flow, cooling rates, and solidification, resulting in higher-quality castings with improved mechanical properties. By leveraging these techniques, foundries can optimize production processes, minimize defects, and enhance productivity.
Improved Material Efficiency:
Foundry technology focuses on maximizing material efficiency by minimizing material waste. Advanced mold design and gating systems help optimize the flow of molten metal, reducing the amount of excess material and scrap. Additionally, techniques like sand reclamation and recycling enable foundries to reuse sand molds, minimizing raw material consumption and reducing costs. By improving material efficiency, foundries can enhance productivity while reducing environmental impact.
Real-time Monitoring and Control:
Foundries employ advanced sensors, data acquisition systems, and control algorithms to monitor and control various parameters during the production process. Real-time monitoring allows operators to identify process deviations and make adjustments promptly, minimizing defects and optimizing production. By leveraging data analytics and machine learning algorithms, foundries can gain valuable insights into process performance, enabling continuous improvement and productivity enhancement.
Energy Optimization:
Foundry technology also focuses on optimizing energy consumption during production processes. Energy-intensive operations, such as melting and heat treatment, can be optimized through efficient furnace design, improved insulation, and optimized process parameters. Foundries may also integrate renewable energy sources, such as solar or biomass, to reduce reliance on conventional energy sources. By optimizing energy usage, foundries can lower production costs, reduce environmental impact, and enhance overall productivity.
Simulation and Virtual Prototyping:
Foundry technology employs computer-aided design (CAD), computer-aided engineering (CAE), and simulation tools to optimize production processes before physical implementation. Virtual prototyping allows for the analysis of mold filling, solidification, and casting defects, enabling foundries to identify potential issues and optimize the process parameters beforehand. By leveraging simulation and virtual prototyping, foundries can minimize trial and error, reduce time to market, and improve productivity.
In summary, foundry technology plays a significant role in maximizing productivity by leveraging process automation, advanced casting techniques, improved material efficiency, real-time monitoring and control, energy optimization, and simulation tools. These advancements enable foundries to enhance production efficiency, reduce costs, minimize defects, and ultimately deliver high-quality products to their customers.