When it comes to sand casting, industry-leading manufacturers understand the importance of providing custom solutions to meet specific project requirements. Here are some key aspects to consider when seeking tailored sand casting services:
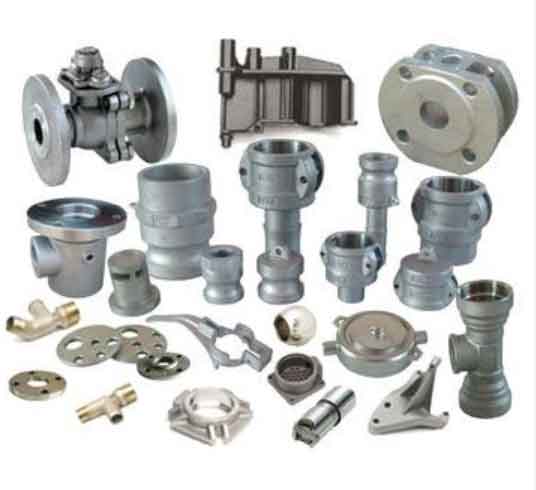
- Design and Engineering Support: Look for manufacturers that offer design and engineering support to optimize your casting design for manufacturability. They should have experienced engineers who can provide input on design feasibility, material selection, and casting process optimization. Collaborating with a manufacturer that can assist in the design phase ensures that your final casting meets your performance and cost requirements.
- Flexibility in Size and Complexity: Consider the manufacturer’s capability to produce sand castings of various sizes and complexities. They should have the expertise and resources to handle both small and large-scale projects, as well as intricate geometries. This ensures that your custom casting needs can be met, regardless of the size or complexity of the component.
- Material Selection: Custom sand casting services should include a wide range of material options to suit your specific application requirements. The manufacturer should have expertise in working with different alloys, including various types of steel, iron, aluminum, and more. They should be able to provide guidance on material selection based on the desired properties and performance of the final casting.
- Prototyping and Rapid Tooling: Rapid prototyping and tooling capabilities are crucial for custom sand casting. Manufacturers that offer in-house prototyping services can help validate designs before proceeding to production. Additionally, having the ability to quickly produce molds and patterns using advanced technologies reduces lead times and allows for faster iterations during the development stage.
- Quality Assurance: Quality control is paramount in custom sand casting. Reputable manufacturers should have robust quality assurance processes in place to ensure the consistent production of high-quality castings. They should perform rigorous inspections, testing, and documentation throughout the manufacturing process to meet the required specifications and industry standards.
- Project Management and Communication: Effective project management and communication are essential for successful custom sand casting. Look for manufacturers that assign dedicated project managers who will serve as your main point of contact. They should provide regular updates on the progress of your project, address any concerns or questions promptly, and ensure smooth coordination between design, production, and delivery.
- Value-added Services: Consider additional services that the manufacturer can offer to enhance the overall value of their custom sand casting services. This may include secondary operations such as machining, surface finishing, assembly, and testing. Having these services available in-house can streamline the production process and reduce the need for multiple suppliers.
- Track Record and Customer Satisfaction: Evaluate the manufacturer’s track record in delivering custom sand casting projects and their customer satisfaction levels. Request references or review testimonials from previous clients to gauge their performance and reliability in meeting custom requirements. Positive feedback and successful case studies demonstrate the manufacturer’s ability to provide tailored solutions.
By partnering with a sand casting manufacturer that specializes in custom solutions, you can ensure that your specific project requirements are met with precision and efficiency. Through close collaboration and expert guidance, you can achieve the desired casting design, quality, and performance for your unique application.