Quality assurance and defect prevention are crucial aspects of the lost foam casting process. Here are some techniques and practices to ensure high-quality castings and minimize defects:
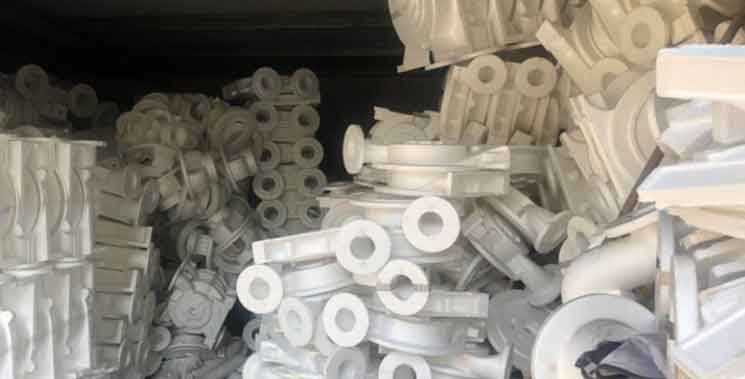
- Pattern Inspection and Quality Control:
- Perform thorough inspection of foam patterns before molding to identify any defects or inconsistencies.
- Use dimensional inspection techniques such as CMM (Coordinate Measuring Machine) to verify pattern accuracy.
- Implement quality control measures at the pattern production stage to ensure consistent foam density, dimensional stability, and surface finish.
- Mold Coating and Surface Preparation:
- Apply a consistent and appropriate mold coating to ensure good surface finish and reduce defects like veining or metal penetration.
- Implement proper mold surface preparation techniques such as cleaning and sandblasting to promote adhesion of the coating and prevent mold-related defects.
- Mold Assembly and Compaction:
- Ensure proper alignment and assembly of mold components to prevent misalignment or shifting during pouring.
- Implement appropriate compaction techniques to achieve uniform and adequate mold density, preventing defects such as blowholes or voids.
- Pouring and Metal Handling:
- Control pouring temperature and rate to avoid overheating or underheating the metal, which can lead to defects like shrinkage or misruns.
- Implement proper metal handling techniques to minimize turbulence and ensure smooth and controlled pouring.
- Gating and Riser Design:
- Optimize gating and riser design to promote proper metal flow, minimize turbulence, and facilitate effective feeding and solidification.
- Use simulation software to analyze and optimize gating and riser systems for improved casting quality and reduced defects.
- Metal Treatment and Degassing:
- Utilize appropriate metal treatment techniques such as alloying, inoculation, and modification to enhance metal quality and minimize defects.
- Implement effective degassing techniques to remove gases and minimize gas-related defects.
- Process Monitoring and Control:
- Implement real-time process monitoring and control systems to ensure consistent and repeatable process parameters.
- Use sensors and data acquisition systems to monitor critical process variables such as mold temperature, metal temperature, and pressure.
- Implement closed-loop control systems to make adjustments in real-time based on process feedback.
- Quality Inspection and Non-Destructive Testing:
- Conduct thorough visual inspections of castings to identify surface defects such as cracks, blowholes, or metal penetration.
- Utilize non-destructive testing methods such as X-ray, ultrasonic testing, or dye penetrant testing to detect internal defects or inconsistencies.
- Documentation and Traceability:
- Maintain comprehensive documentation of process parameters, inspections, and quality control measures for each casting.
- Implement traceability systems to track patterns, molds, and castings, enabling identification of any issues or defects throughout the production cycle.
- Continuous Improvement and Lessons Learned:
- Analyze defects, their root causes, and corrective actions taken to prevent their recurrence.
- Encourage employees to provide feedback and suggestions for process improvement.
- Foster a culture of continuous improvement and implement corrective and preventive actions based on lessons learned.
By implementing these quality assurance techniques and defect prevention practices, manufacturers can enhance the overall quality of lost foam castings, minimize defects, and ensure customer satisfaction.