Sand casting, with its versatility and adaptability, can unlock the potential for manufacturing complex metal parts. Here are some key considerations for utilizing sand casting to produce complex components:
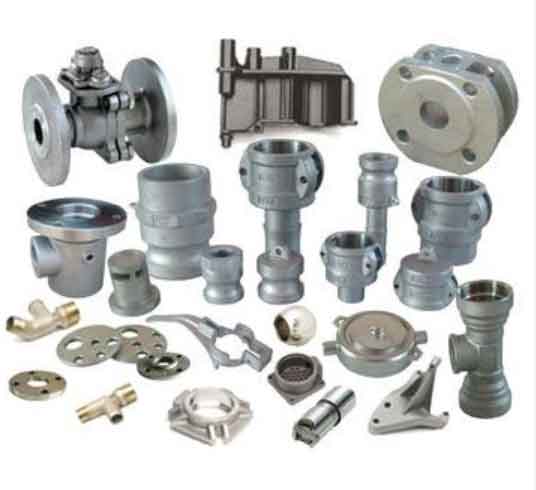
- Advanced Pattern Making Techniques:
- Complex parts often require intricate patterns to capture the desired geometry.
- Advanced pattern making techniques, such as computer-aided design (CAD) and computer-aided manufacturing (CAM), can be employed to create precise patterns with intricate details and complex shapes.
- Utilizing additive manufacturing (3D printing) for pattern production can also facilitate the creation of complex geometries that would be difficult or impossible with traditional pattern-making methods.
- Core Design and Implementation:
- Cores are used to create internal cavities or complex features within the casting.
- Designing and implementing cores accurately is crucial for achieving complex part geometries.
- Advanced core-making techniques, such as shell cores or ceramic cores, can be employed to produce intricate internal passages or undercuts.
- Advanced Mold Preparation:
- Employing advanced molding techniques can enhance the ability to cast complex parts.
- Techniques like vacuum molding or precision sand control can improve mold quality and surface finish, enabling the reproduction of intricate part details.
- The use of binders, coatings, or additives can further enhance mold strength, dimensional stability, and the ability to reproduce fine features.
- Gating and Riser Design Optimization:
- Proper gating and riser design are crucial for casting complex parts without defects.
- Advanced simulation software can be employed to optimize gating and riser systems, ensuring proper metal flow, minimizing turbulence, and avoiding shrinkage or porosity issues.
- Optimization helps achieve balanced filling, reducing the risk of casting defects and ensuring dimensional accuracy.
- Heat Treatment and Post-Casting Processing:
- Complex parts may require heat treatment or post-casting processing to achieve specific material properties or improve dimensional accuracy.
- Proper heat treatment techniques can be applied to enhance the mechanical properties and structural integrity of the casting.
- Machining, surface finishing, or coating processes can be employed to achieve precise dimensions and desired surface characteristics.
- Quality Control and Inspection:
- Implementing robust quality control measures is crucial when casting complex parts.
- Advanced non-destructive testing (NDT) techniques, such as X-ray inspection, ultrasound testing, or 3D scanning, can be utilized to ensure the integrity and quality of the casting.
- In-process inspections and dimensional checks at various stages of the casting process can help identify any deviations and enable corrective actions.
- Collaboration and Expertise:
- Collaborating with experienced foundries, pattern makers, and casting engineers is essential for successfully casting complex parts.
- Leveraging their expertise and knowledge can provide valuable insights into design optimization, process selection, and troubleshooting potential challenges.
By considering these factors and utilizing advanced techniques, sand casting can be effectively leveraged to unlock the potential for manufacturing complex metal parts. The combination of advanced design, mold preparation, gating optimization, post-casting processing, and quality control measures enables the production of intricate and precise components through sand casting.