Lost foam casting is indeed a revolutionary approach to precision metal casting, offering unique advantages and capabilities compared to traditional casting methods. Here’s an overview of lost foam casting and its key features:
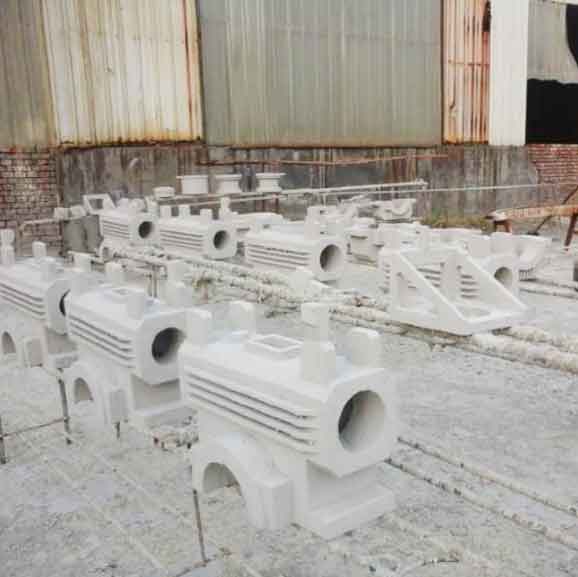
- Process Overview:
- Lost foam casting, also known as evaporative pattern casting, involves creating a foam pattern that serves as a replica of the desired metal part.
- The foam pattern is coated with a refractory material to create a shell, forming the mold.
- The foam pattern is then vaporized or “lost” when the molten metal is poured into the mold, filling the void left by the evaporated foam.
- The metal solidifies and takes the shape of the original foam pattern, resulting in a precise and intricate metal casting.
- Design Flexibility and Complexity:
- Lost foam casting allows for intricate and complex part designs with high precision.
- The foam patterns can be easily formed into intricate shapes, including thin walls, undercuts, and internal features, without the need for complex cores or tooling.
- Design changes can be easily implemented by modifying the foam pattern, reducing the time and cost associated with pattern revisions.
- Dimensional Accuracy and Surface Finish:
- Lost foam casting achieves excellent dimensional accuracy, as the metal solidifies with minimal shrinkage or distortion.
- The absence of parting lines or core shift results in a smoother surface finish, reducing the need for post-casting machining or finishing operations.
- The precision and consistency of lost foam casting contribute to reduced material waste and improved overall part quality.
- Cost and Time Efficiency:
- Lost foam casting offers cost and time savings compared to traditional casting methods.
- The elimination of complex cores and tooling reduces the overall tooling costs.
- Since the foam patterns can be produced rapidly and with minimal material waste, the lead time for pattern production is significantly reduced.
- The absence of core removal, shakeout, and core disposal operations streamlines the casting process, resulting in faster production cycles.
- Material Versatility:
- Lost foam casting can be used with a wide range of metals and alloys, including aluminum, iron, steel, and more.
- The process is suitable for both ferrous and non-ferrous metals, providing flexibility in material selection for specific applications.
- This versatility makes lost foam casting applicable to various industries, including automotive, aerospace, and industrial manufacturing.
- Reduction of Machining and Assembly:
- Lost foam casting produces near-net shape castings, reducing the need for extensive machining or assembly operations.
- Complex features, such as internal cavities and threads, can be cast directly into the part, eliminating the need for additional machining steps.
- This streamlines the manufacturing process, saves time, and reduces overall production costs.
- Environmental Benefits:
- Lost foam casting is an environmentally friendly process with minimal waste generation.
- The foam pattern can be easily recycled or disposed of without causing significant environmental impact.
- The absence of sand molds or binders reduces the amount of waste generated during the casting process.
Lost foam casting has revolutionized precision metal casting by offering design flexibility, dimensional accuracy, cost and time efficiency, material versatility, and reduced machining requirements. Its unique approach to creating intricate patterns and producing high-quality castings has made it a preferred choice for applications that demand complex geometries and precise specifications.