Die casting and semi-continuous casting are two distinct casting methods used in metal manufacturing. Let’s compare them in terms of their process, capabilities, advantages, and disadvantages:
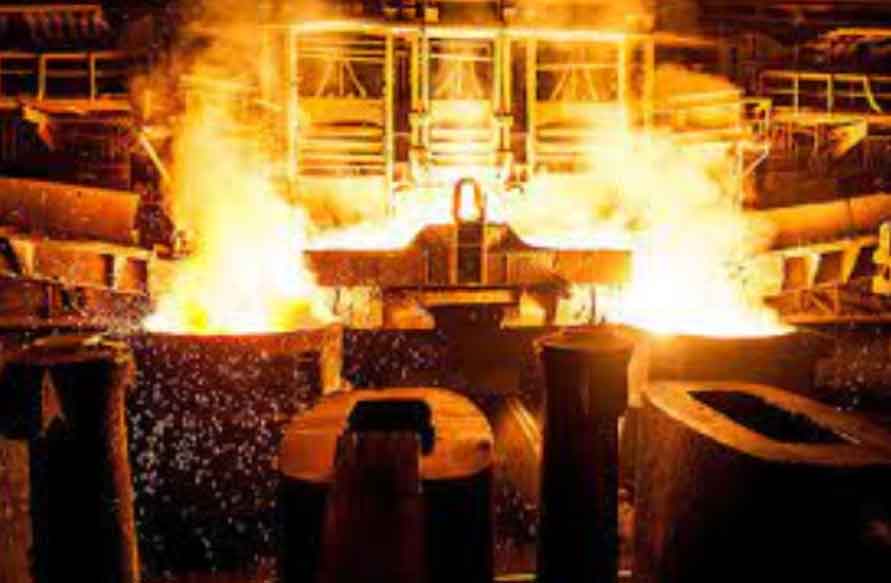
Die Casting:
- Process: Die casting involves injecting molten metal, typically non-ferrous alloys like aluminum, zinc, or magnesium, into a reusable steel mold called a die. The mold is designed with the shape and features of the desired part.
- Complexity: Die casting is suitable for producing parts with intricate details, thin walls, and complex shapes. It allows for tight dimensional tolerances and repeatability.
- Speed: Die casting is a high-speed process as the molten metal is injected under high pressure into the die, enabling rapid solidification.
- Surface Finish: Die casting offers excellent surface finish and can achieve smooth, polished, and visually appealing surfaces without the need for additional post-processing.
- Volume Production: Die casting is well-suited for high-volume production runs. Once the die is made, it can produce a large number of parts with consistent quality and dimensional accuracy.
- Material Options: Die casting is primarily used for non-ferrous alloys such as aluminum, zinc, and magnesium. These materials offer good strength-to-weight ratios and are commonly used in various industries.
Semi-Continuous Casting:
- Process: Semi-continuous casting is a casting method that involves the continuous pouring of molten metal into a series of molds or a water-cooled metal mold. The molten metal solidifies partially in each mold before moving to the next one.
- Complexity: Semi-continuous casting is suitable for producing simple to moderately complex parts with solidification occurring in multiple stages. It is not as capable of producing intricate details as die casting.
- Speed: Semi-continuous casting is generally slower compared to die casting, as the metal solidifies partially in each mold before moving to the next one. However, it can still be faster than other casting methods like sand casting.
- Surface Finish: The surface finish in semi-continuous casting can vary depending on the mold design and process parameters. It may require post-processing to achieve the desired surface smoothness.
- Volume Production: Semi-continuous casting can be used for both small and large production volumes. It offers flexibility in producing batches of parts, making it suitable for a range of production quantities.
- Material Options: Semi-continuous casting is used for various metals and alloys, including both ferrous and non-ferrous materials. It is commonly used for casting metals like steel, aluminum, and copper alloys.
Advantages of Die Casting:
- High production speed and efficiency.
- Excellent dimensional accuracy and repeatability.
- Suitable for high-volume production.
- Wide range of material options.
- Smooth surface finish without additional post-processing.
Disadvantages of Die Casting:
- Limited complexity compared to certain casting methods.
- Higher tooling and setup costs.
- Not ideal for extremely high-temperature alloys.
Advantages of Semi-Continuous Casting:
- Capable of producing simple to moderately complex parts.
- Suitable for both small and large production volumes.
- Flexible batch production for different quantities.
- Supports a wide range of metal materials.
- Less tooling and setup costs compared to die casting.
Disadvantages of Semi-Continuous Casting:
- Slower production compared to die casting.
- Limited to parts with simpler to moderately complex geometries.
- Surface finish may require additional post-processing.
- Less suitable for parts with intricate details and thin walls.
When deciding between die casting and semi-continuous casting, consider factors such as part complexity, production volume, material requirements, surface finish specifications, and cost considerations. Die casting is preferable for high-volume production of complex parts with intricate details, tight tolerances, and superior surface finish. It offers fast production speeds, excellent dimensional accuracy, and is well-suited for non-ferrous alloys.
On the other hand, semi-continuous casting is suitable for producing simpler to moderately complex parts in varying production volumes. It offers flexibility in batch production and supports a wider range of metal materials, including both ferrous and non-ferrous alloys.
Consider the following factors when making a decision:
- Part Complexity: If your parts require intricate details, thin walls, or complex geometries, die casting would be the better choice due to its capability to produce highly complex parts.
- Production Volume: Die casting is advantageous for high-volume production due to its fast cycle times and efficiency. If you require smaller production volumes or flexibility in batch sizes, semi-continuous casting can be a suitable option.
- Material Selection: Die casting is primarily used for non-ferrous alloys such as aluminum, zinc, and magnesium. If your project requires a broader range of metal options, including ferrous alloys like steel, semi-continuous casting would be more appropriate.
- Surface Finish Requirements: Die casting generally provides a superior surface finish without the need for extensive post-processing. However, if your parts have specific surface finish requirements and can tolerate additional post-processing steps, semi-continuous casting can meet those needs.
- Cost Considerations: Die casting typically involves higher tooling and setup costs due to the complexity of the dies. If cost efficiency is a significant factor and your parts can be produced using semi-continuous casting, it may be a more cost-effective option.
It’s crucial to thoroughly assess your project’s requirements and consult with casting experts or manufacturers to determine the most suitable casting method. They can provide insights into factors such as part design, material selection, production volume, and cost-effectiveness to help you make an informed decision.
Furthermore, consider exploring other casting methods like sand casting, investment casting, or precision casting, as they might offer viable alternatives depending on the specific requirements of your project.