Lost foam casting is widely recognized for its ability to achieve superior quality in castings. The process offers several factors that contribute to precision and perfection in the final products. Here’s a closer look at how lost foam casting enables the production of high-quality castings:
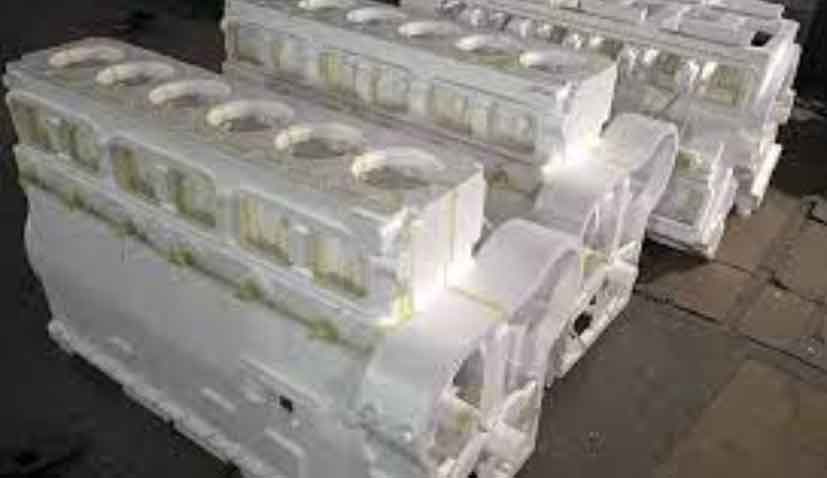
- Accurate Reproduction of Complex Geometries:
- Lost foam casting allows for the accurate reproduction of complex and intricate part geometries.
- The foam patterns used in the process are designed to replicate the final part shape with precision.
- This capability enables the production of castings with intricate features, thin walls, and complex internal structures, ensuring the exact replication of the intended design.
- Dimensional Accuracy and Consistency:
- Lost foam casting achieves excellent dimensional accuracy and consistency.
- The foam patterns, which accurately represent the final part geometry, contribute to precise casting replication.
- The absence of core-related factors, such as core expansion or shrinkage, minimizes dimensional variations, ensuring consistent and accurate castings.
- Elimination of Core Shift and Mismatch:
- Lost foam casting eliminates the risk of core shift and mold mismatch that can occur in traditional casting methods.
- The foam patterns serve as temporary molds, allowing for better control over the casting process.
- This eliminates the need for complex core-making techniques and ensures that the casting precisely conforms to the desired shape, minimizing casting defects.
- Improved Surface Finish:
- Lost foam castings often exhibit excellent surface finish quality.
- The smooth and precise foam patterns result in high-quality mold surfaces, which are transferred to the castings.
- The absence of sand molds or binders reduces the likelihood of surface defects, such as sand inclusions or mold-related imperfections.
- Reduced Porosity and Defects:
- Lost foam casting helps minimize the occurrence of porosity and other casting defects.
- The controlled evaporative process of the foam patterns ensures clean and well-defined mold cavities.
- The absence of binders or sand-related factors reduces the potential for gas entrapment, resulting in sound castings with minimal defects.
- Improved Metallurgical Properties:
- Lost foam casting can result in improved metallurgical properties of the castings.
- The rapid heat transfer from the molten metal to the foam pattern mold promotes fine grain structure formation, enhancing mechanical properties.
- The absence of sand molds reduces the risk of sand-related inclusions or impurities in the casting, contributing to improved material integrity.
- Quality Control and Inspection:
- Lost foam casting allows for efficient quality control and inspection processes.
- The use of precise foam patterns and near-net shape castings reduces the need for extensive post-casting machining or rework.
- Non-destructive testing techniques, such as visual inspection, ultrasonic testing, or X-ray inspection, can be performed to ensure casting integrity.
- Continuous Process Improvement:
- Lost foam casting encourages continuous process improvement and optimization.
- By closely monitoring and analyzing the casting process, foundries can identify areas for enhancement and refine their techniques to achieve even higher quality standards.
- Simulation software and data analytics can be employed to optimize casting parameters and predict potential defects, leading to improved quality control.
Lost foam casting excels in achieving precision and perfection in castings through accurate reproduction of complex geometries, dimensional accuracy, elimination of core shift and mismatch, improved surface finish, reduced porosity and defects, improved metallurgical properties, efficient quality control, and continuous process improvement. With its ability to produce high-quality castings, lost foam casting has become a preferred choice for applications where precision and superior quality are paramount.