While traditional sand casting is a widely used method for gray cast iron casting, there are alternative techniques available that offer unique advantages and possibilities. These alternative techniques include:
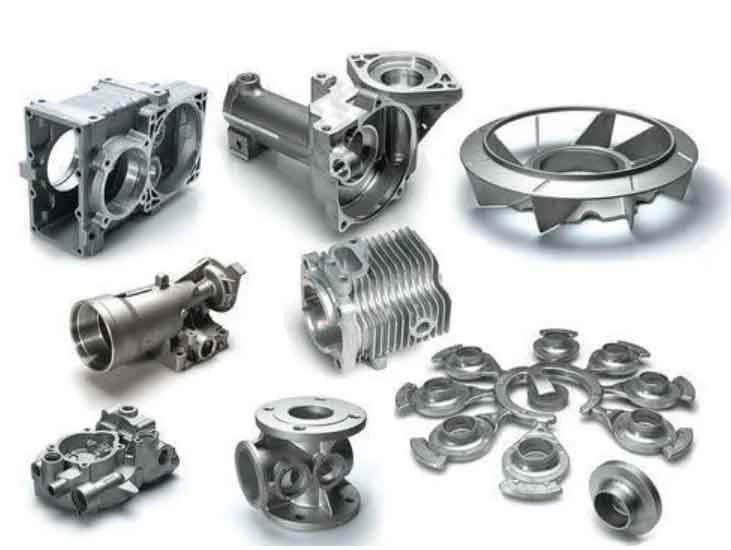
- Shell Molding: Shell molding, also known as shell core casting, is a process that uses resin-coated sand to create the mold. The resin-coated sand is heated and cured to form a thin, rigid shell around the pattern. This method provides improved dimensional accuracy, excellent surface finish, and reduced casting defects compared to traditional sand casting.
- Ceramic Molding: Ceramic molding, also known as precision casting or lost wax casting, involves creating a ceramic mold from a wax pattern. The wax pattern is coated with ceramic slurry, dried, and then heated to remove the wax and harden the ceramic shell. The resulting mold is then used for casting the gray iron. Ceramic molding offers high dimensional accuracy, intricate details, and excellent surface finish, making it suitable for complex and high-precision components.
- Investment Casting: Investment casting, also known as lost wax casting, is a process that uses a wax pattern to create a ceramic mold. The wax pattern is coated with multiple layers of ceramic slurry, which is then hardened and cured. The mold is then heated to remove the wax, leaving behind a cavity that is filled with molten gray iron. Investment casting allows for the production of intricate and complex shapes with high dimensional accuracy and smooth surface finish.
- Die Casting: Die casting involves injecting molten gray iron into a steel mold, also known as a die, under high pressure. The molten metal rapidly solidifies to form the desired component shape. Die casting offers high production efficiency, tight dimensional tolerances, and excellent surface finish. It is particularly suitable for high-volume production of smaller and more complex components.
- Continuous Casting: Continuous casting is a method used for producing long and continuous sections of gray cast iron, such as bars or rods. In this process, molten gray iron is continuously poured into a water-cooled mold, where it solidifies into the desired shape. Continuous casting offers high production rates, reduced material waste, and improved material properties due to the controlled solidification process.
Each of these alternative casting techniques provides unique advantages in terms of dimensional accuracy, surface finish, production efficiency, and the ability to create complex and intricate components. The choice of casting method depends on factors such as the component’s design, required tolerances, production volume, and cost considerations. By exploring these alternative techniques, manufacturers can optimize the casting process for gray cast iron components and achieve the desired results.