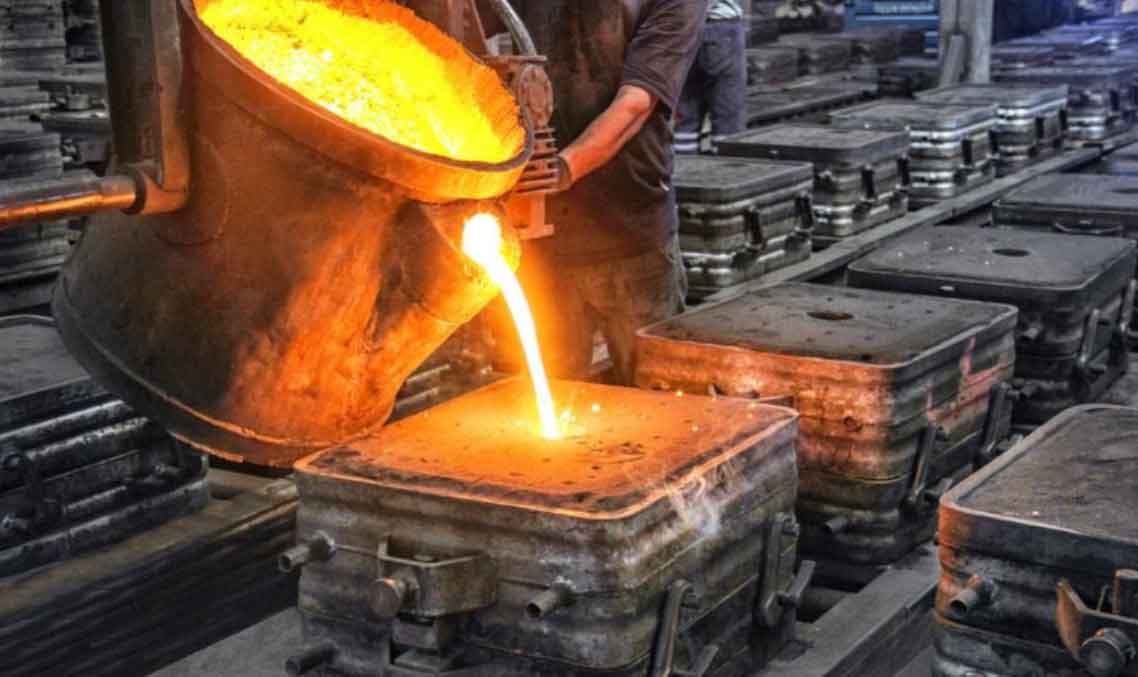
Quality assurance is a critical aspect of sand casting to ensure top-notch products that meet the required specifications and standards. Sand casting manufacturers implement various techniques and practices to maintain quality throughout the casting process. Here are some key ways manufacturers ensure top-notch products in sand casting:
- Process Control and Documentation: Manufacturers establish and follow standardized processes for sand preparation, molding, pouring, and cooling. Process parameters, such as sand mixture proportions, curing time, pouring temperature, and cooling rates, are documented and monitored to ensure consistency and repeatability.
- Material Inspection and Certification: Incoming raw materials, including sand, resin, and metal alloys, undergo thorough inspection and testing to ensure they meet the required quality standards and specifications.
- Pattern Inspection and Maintenance: Patterns used in sand casting are regularly inspected to ensure accuracy and dimensional stability. Any pattern wear or deformation is addressed promptly to maintain casting quality.
- Mold Inspection and Integrity Checks: The integrity of molds is examined before pouring to avoid defects. Visual inspections, ultrasonic testing, or X-ray inspections are employed to detect any mold issues that may compromise the casting quality.
- Casting Simulation: Advanced casting simulation software is used to predict and analyze the filling and solidification of the mold. Simulation helps identify potential defects and optimize the casting process for better quality.
- In-Process Inspection: Quality checks are performed during the casting process to monitor critical parameters and identify any deviations. This includes checking mold compaction, core placement, and pouring conditions.
- Post-Casting Inspection: Once the castings have cooled, they undergo rigorous inspection to verify dimensional accuracy, surface finish, and structural integrity. Non-destructive testing techniques, such as visual inspection, dye penetrant testing, and radiographic testing, are used to detect defects.
- Quality Control Tools: Manufacturers use various quality control tools, such as Statistical Process Control (SPC), Six Sigma, and Failure Mode and Effects Analysis (FMEA), to monitor and improve the casting process continually.
- Certifications and Standards: Sand casting manufacturers often obtain certifications, such as ISO 9001, to demonstrate their commitment to quality and adherence to internationally recognized standards.
- Continuous Improvement: Manufacturers implement continuous improvement initiatives to identify areas for enhancement and implement corrective actions to prevent defects and improve casting quality.
- Training and Skill Development: Employees involved in the casting process undergo regular training to enhance their skills and ensure they follow the best practices for quality assurance.
- Traceability: Comprehensive record-keeping and traceability systems are maintained to track each casting through the production process, enabling quick identification of any quality issues.
By integrating these quality assurance practices into their processes, sand casting manufacturers can deliver top-notch products that meet customer expectations and comply with industry standards. Continuous monitoring, inspection, and improvement efforts are essential for achieving consistent quality and ensuring customer satisfaction.