Steel castings manufacturers are actively transitioning towards green practices to mitigate their environmental impact. This shift is driven by a mix of innovation, market demands, and regulatory pressures, aiming to reduce carbon emissions inherent in traditional steel casting production processes.
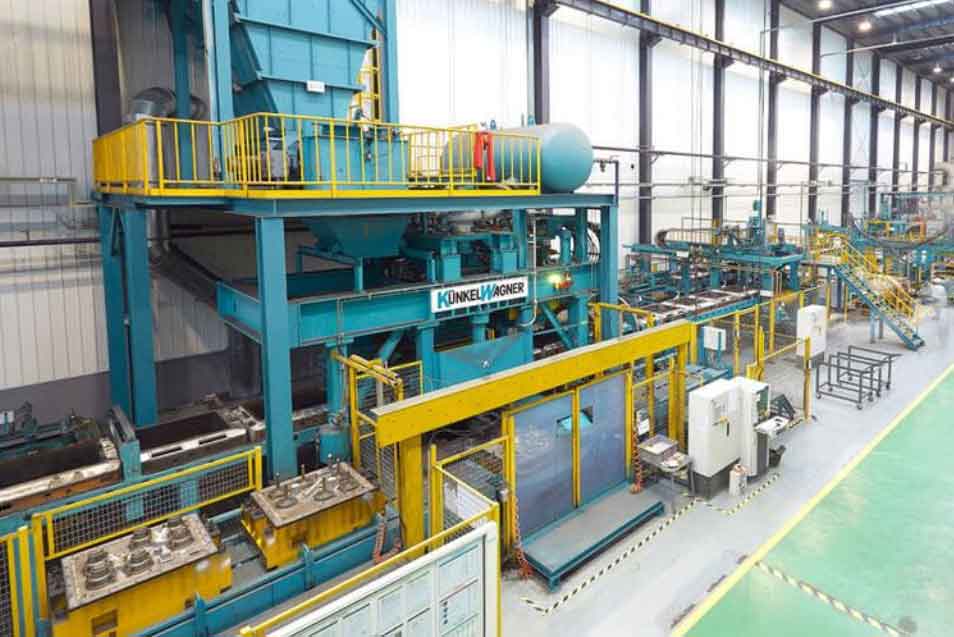
Key strategies being adopted include:
- Recycling and Circular Economy: Companies are emphasizing the use of recycled steel which significantly reduces energy consumption and carbon emissions compared to producing new steel from raw iron ore.
- Hydrogen-Based Steelmaking: Replacing coke with hydrogen in steelmaking processes is another major shift. Hydrogen burns cleanly, producing water instead of carbon dioxide, thus cutting down the carbon footprint of steel casting production.
- Electric Arc Furnaces (EAFs): These are used to melt scrap steel using electricity rather than coke. EAFs are more energy-efficient and produce fewer greenhouse gases compared to traditional blast furnaces.
- Carbon Capture and Storage (CCS): This technology involves capturing carbon dioxide emissions produced during steel manufacturing and storing them safely underground to prevent their release into the atmosphere.
- Energy Efficiency: Steel manufacturers are improving the energy efficiency of their operations by optimizing processes, reducing waste, and incorporating renewable energy sources.
- Sustainable Sourcing: Focusing on the responsible sourcing of raw materials is another critical element, ensuring that the environmental impact is minimized right from the extraction stage.
- Advanced Technologies: The integration of new technologies such as digitalization and automation is helping steel manufacturers optimize their steel casting production processes. This not only improves efficiency but also reduces energy usage and waste, thereby minimizing the environmental footprint.
- Direct-Reduced Iron and Electric Arc Furnaces (DRI-EAF): This method is gaining traction as it allows for the use of renewable energy sources. DRI-EAFs use electric power (potentially from renewable sources) and are capable of operating with hydrogen as a reducing agent, which can lead to significant reductions in carbon emissions compared to traditional methods.
- Collaboration with Iron Ore Suppliers: Steel manufacturers are also working closely with iron ore suppliers to ensure that the raw materials used are sourced sustainably and that they support steel casting production of low-carbon steel. This partnership helps in managing the upstream Scope 3 emissions associated with steel casting production.
- Global Standards and Certifications: To foster sustainability across the global market, steel producers are increasingly adhering to international standards and seeking certifications for green steel. This helps in not only improving their processes but also in maintaining credibility and transparency in the sustainability of their steel casting products .
- Policy and Regulation Compliance: Compliance with new regulations such as the Carbon Border Adjustment Mechanism (CBAM) in the EU, which taxes imported steel based on carbon content, is pushing manufacturers towards greener production practices. Such policies incentivize the reduction of carbon emissions and support the market shift towards sustainable steel casting production.
Additionally, the global market for green steel is expanding, fueled by increasing regulatory requirements and growing demand from sectors such as construction and automotive, which are seeking more sustainable materials.
These sustainable initiatives are not just about reducing emissions but also about improving air quality, conserving resources, and ultimately leading to cost savings and gaining a competitive advantage in the market. The future of green steel casting production appears promising, with technological advances and increasing investments driving the industry towards greater sustainability and efficiency.
The push towards green steel casting production is a comprehensive effort involving technological innovations, regulatory compliance, market adaptations, and collaborative ventures across the supply chain. This holistic approach is essential for achieving significant reductions in carbon emissions and moving towards a sustainable future in steel manufacturing. As these practices become more prevalent and technologically advanced, the steel industry is poised for a transformation that promises economic, environmental, and societal benefits.