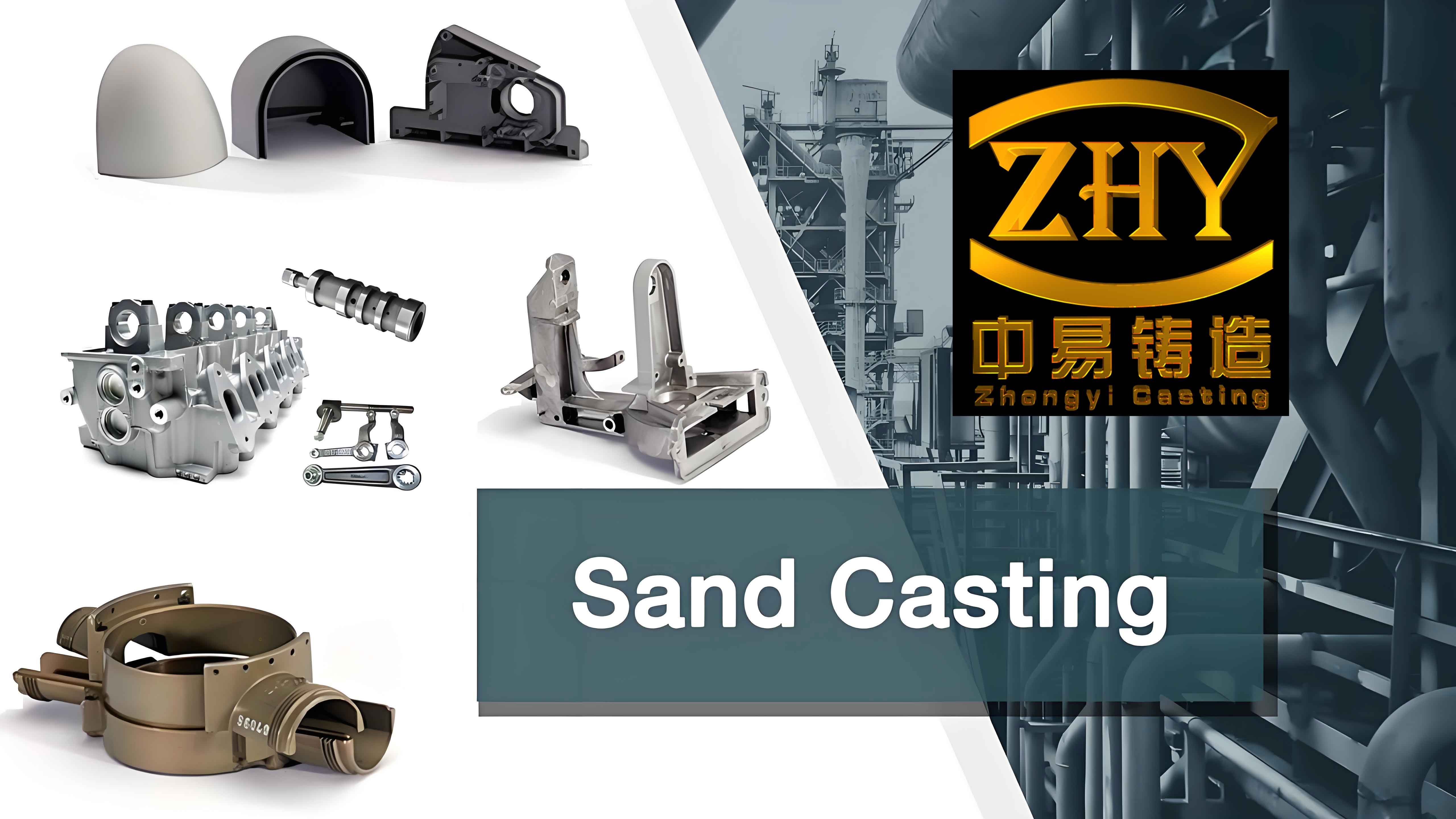
Sand casting is widely used manufacturing process that involves creating a mold from a sand mixture and pouring molten metal into the mold to form the desired shape. Despite its versatility and cost-effectiveness, sand casting parts often results in parts with a rough surface finish, which may necessitate additional machining and finishing operations. Improving the surface finish of sand casted parts is crucial for enhancing the quality and performance of the final products. This article explores various innovative techniques for improving the surface finish in sand casting parts.
Importance of Surface Finish in Sand Casting Parts
A good surface finish in sand casted parts is essential for several reasons:
- Aesthetic Appeal
- A smooth surface finish enhances the visual appeal of the final product, which is particularly important for consumer-facing components.
- Performance and Functionality
- Surface finish affects the performance of mechanical parts, including their friction, wear resistance, and fatigue strength.
- Dimensional Accuracy
- Improved surface finish often correlates with better dimensional accuracy, reducing the need for extensive post-processing.
- Cost Efficiency
- Reducing the roughness of sand casted parts can lower the costs associated with additional machining and finishing operations.
Innovative Techniques for Improving Surface Finish
1. Enhanced Sand Mold Materials
Using high-quality sand mold materials can significantly improve the surface finish of sand casted parts.
Types of Enhanced Sand Mold Materials:
- Resin-Coated Sand
- Resin-coated sand provides a smoother surface compared to traditional green sand molds, resulting in a finer finish on the casted parts.
- Silica Sand with Additives
- Adding fine particles and binders to silica sand can improve the mold’s surface texture and reduce roughness.
Material | Advantages | Disadvantages |
---|---|---|
Resin-Coated Sand | Smoother surface, finer finish | Higher cost |
Silica Sand with Additives | Improved texture, reduced roughness | Potential increase in production time |
2. Mold Coatings
Applying coatings to the sand mold can create a barrier that enhances the surface finish of the casted part.
Types of Mold Coatings:
- Graphite Coating
- Graphite coatings provide a smooth surface and reduce metal penetration into the mold, resulting in a better finish.
- Zircon-Based Coating
- Zircon-based coatings offer excellent thermal resistance and smooth surface properties, improving the final part’s quality.
Coating | Advantages | Disadvantages |
---|---|---|
Graphite Coating | Smooth surface, reduced metal penetration | Additional application step |
Zircon-Based Coating | Thermal resistance, improved surface | Higher cost |
3. Vibration and Compaction Techniques
Utilizing vibration and compaction techniques during mold preparation can enhance the density and uniformity of the sand mold, leading to a better surface finish.
Techniques:
- Vibration Compaction
- Applying vibration during mold preparation helps achieve a more uniform sand density, reducing surface roughness.
- Compaction with Presses
- Using mechanical presses to compact the sand mold ensures a consistent and smooth surface.
Technique | Advantages | Disadvantages |
---|---|---|
Vibration Compaction | Uniform sand density, smoother finish | Requires specialized equipment |
Compaction with Presses | Consistent surface, improved finish | Potential increase in mold preparation time |
4. Improved Pouring Techniques
Optimizing the pouring process can minimize defects and improve the surface finish of sand casted parts.
Methods:
- Controlled Pouring Rate
- Maintaining a consistent and controlled pouring rate reduces turbulence and the risk of defects, resulting in a better surface finish.
- Directional Solidification
- Designing the mold to promote directional solidification ensures uniform cooling and reduces surface roughness.
Method | Advantages | Disadvantages |
---|---|---|
Controlled Pouring Rate | Reduced defects, smoother surface | Requires precise control mechanisms |
Directional Solidification | Uniform cooling, improved surface finish | Complex mold design |
5. Post-Casting Surface Treatments
Applying surface treatments after casting can further enhance the surface finish of sand casted parts.
Treatments:
- Shot Blasting
- Shot blasting involves propelling abrasive materials at the casted part to smooth the surface and remove any residual sand.
- Electropolishing
- Electropolishing is an electrochemical process that removes a thin layer of material from the surface, resulting in a mirror-like finish.
Treatment | Advantages | Disadvantages |
---|---|---|
Shot Blasting | Smooth surface, sand removal | Additional processing step |
Electropolishing | Mirror-like finish, precise control | Higher cost |
6. Advanced Mold Design
Incorporating advanced mold design techniques can also contribute to an improved surface finish.
Design Techniques:
- Fillets and Radii
- Incorporating fillets and radii in the mold design reduces sharp corners and stress concentrations, leading to a better surface finish.
- Venting Systems
- Proper venting systems prevent gas entrapment and defects, resulting in a smoother surface.
Technique | Advantages | Disadvantages |
---|---|---|
Fillets and Radii | Reduced stress, improved surface finish | Complex mold design |
Venting Systems | Prevents gas entrapment, smoother surface | Requires precise design |
Conclusion
Improving the surface finish of sand casted parts is essential for enhancing the quality, performance, and aesthetics of the final products. By adopting innovative techniques such as using enhanced sand mold materials, applying mold coatings, utilizing vibration and compaction techniques, optimizing pouring methods, implementing post-casting surface treatments, and incorporating advanced mold design, manufacturers can achieve significant improvements in surface finish. These advancements not only improve the overall quality of sand casted parts but also contribute to cost savings and increased efficiency in the production process. By continually exploring and implementing innovative techniques, the sand casting industry can meet the evolving demands for high-quality casted components in various applications.