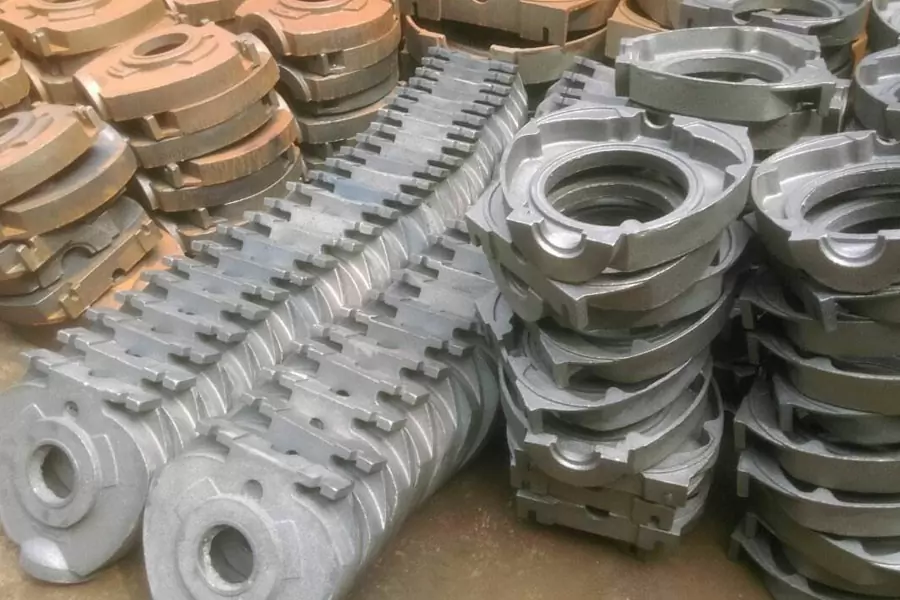
Digital technologies have significantly impacted sand casting services, leading to improvements in efficiency, quality, and cost-effectiveness. Here are some key areas where digital technologies have made a difference:
1. Computer-Aided Design (CAD) and Computer-Aided Manufacturing (CAM)
- Enhanced Design Precision: CAD software allows engineers to create detailed and precise designs, which can be directly used for manufacturing without the need for manual drawing and interpretation.
- Simulation and Testing: CAM software can simulate the sand casting services, predicting potential issues such as shrinkage, porosity, and thermal stresses, allowing for adjustments before actual casting.
2. 3D Printing and Rapid Prototyping
- Pattern Making: 3D printing technology can produce highly accurate patterns for sand casting services, reducing the time and cost associated with traditional pattern making methods.
- Prototyping: Rapid prototyping enables the creation of prototypes quickly and economically, allowing for iterative testing and refinement of designs.
3. Automation and Robotics
- Automated Mold Making: Robotics and automated systems can create molds with high precision and repeatability, improving the consistency of the cast parts.
- Handling and Finishing: Automated systems can also handle post-casting processes such as cleaning, finishing, and quality inspection, reducing labor costs and human error.
4. Data Analytics and Quality Control
- Real-Time Monitoring: Sensors and IoT devices can monitor the sand casting services in real-time, collecting data on temperature, pressure, and other critical parameters.
- Predictive Maintenance: Data analytics can predict equipment failures and maintenance needs, minimizing downtime and extending the lifespan of machinery.
5. Digital Twin Technology
- Process Optimization: Digital twins—virtual replicas of the sand casting services—can be used to simulate and optimize every aspect of manufacturing, from mold design to cooling times.
- Enhanced Collaboration: Digital twins facilitate better communication and collaboration between different teams and stakeholders, ensuring that everyone has access to the same detailed and up-to-date information.
6. Supply Chain Integration
- Inventory Management: Digital technologies enable better tracking and management of raw materials and finished products, reducing waste and ensuring timely delivery.
- Enhanced Traceability: Digital records provide detailed traceability of each component, improving quality control and compliance with industry standards.
Benefits of Digital Technologies in Sand Casting Services
- Reduced Lead Times: Automation and digital tools significantly cut down the time required from design to final product.
- Improved Quality: Enhanced precision and real-time monitoring lead to higher quality castings with fewer defects.
- Cost Savings: Reduction in manual labor, material waste, and downtime result in overall cost savings.
- Flexibility and Customization: Digital technologies allow for greater flexibility in design changes and customization to meet specific client needs.
Overall, the integration of digital technologies in sand casting services has revolutionized the industry, making it more efficient, accurate, and responsive to market demands.