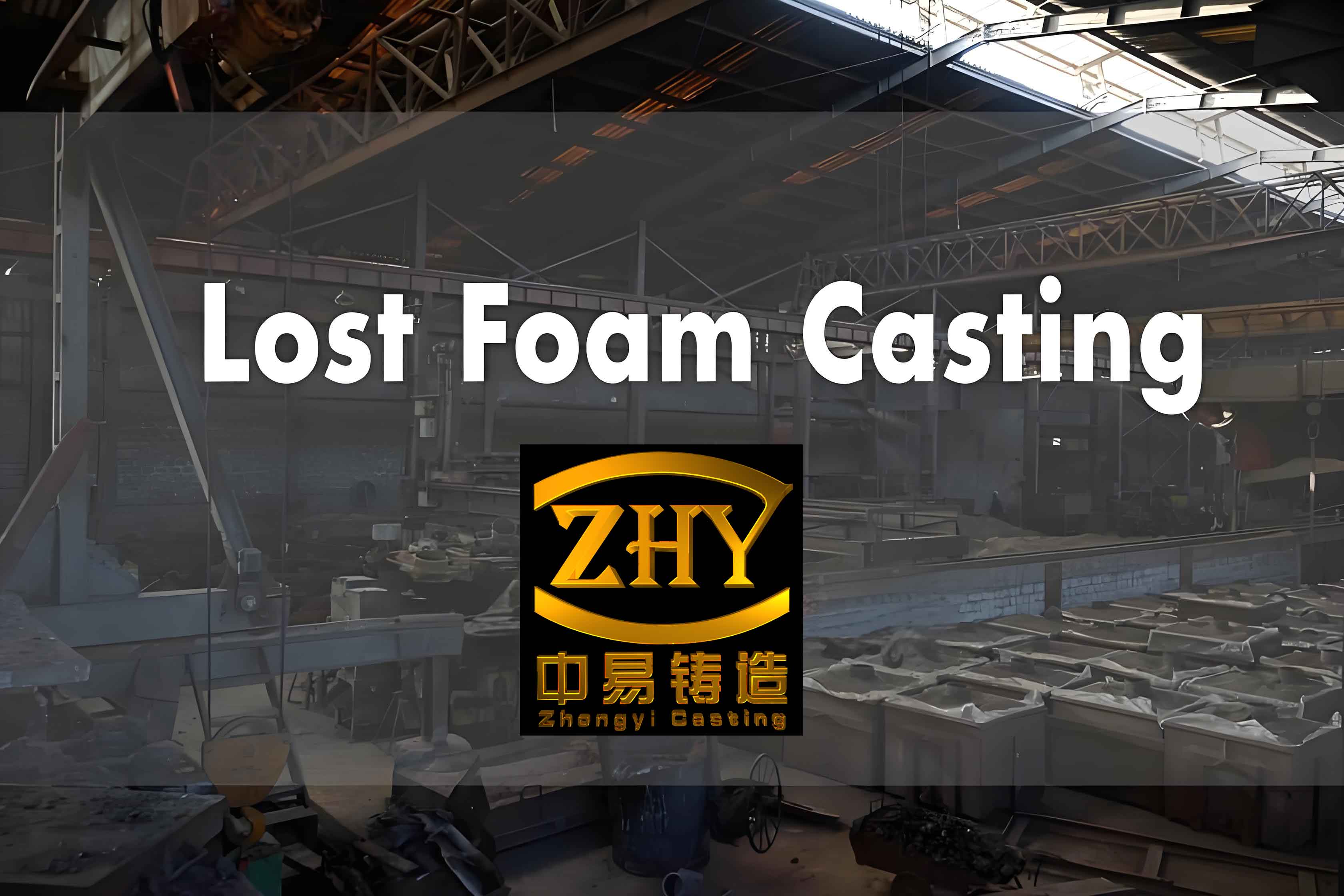
Lost foam casting is a versatile and precise casting method that produces complex metal components with high dimensional accuracy and excellent surface finish. However, to further enhance the mechanical properties and performance of lost foam cast components, heat treatment processes are often applied. These processes can improve the strength, hardness, ductility, and toughness of the cast components, making them suitable for demanding applications. This article explores various heat treatment processes for lost foam cast components, detailing their principles, benefits, and applications.
Introduction to Lost Foam Casting
Lost foam casting involves creating a foam pattern that replicates the final metal part, coating it with a refractory material, and embedding it in a sand mold. When molten metal is poured into the mold, the foam pattern vaporizes, leaving behind a detailed metal casting. This process is particularly well-suited for producing intricate geometries with high precision and minimal need for post-casting machining.
Key Steps in Lost Foam Casting
- Foam Pattern Creation: A foam model of the desired component is created using suitable foam materials.
- Pattern Assembly: The foam pattern is assembled with gating systems if needed.
- Coating: The foam pattern is coated with a refractory material to form a thin shell.
- Mold Preparation: The coated foam pattern is placed in a sand mold, and sand is packed around it.
- Metal Pouring: Molten metal is poured into the mold, causing the foam pattern to vaporize and be replaced by the metal.
- Mold Breakout: Once the metal has solidified, the sand mold is broken away to reveal the metal casting.
- Finishing: The casting is cleaned, and any excess material is removed to achieve the final product.
Importance of Heat Treatment for Lost Foam Cast Components
Heat treatment processes are applied to lost foam cast components to alter their microstructure and enhance their mechanical properties. The benefits of heat treatment include:
- Increased Strength: Enhances the load-bearing capacity of the cast components.
- Improved Hardness: Provides better wear resistance for components exposed to abrasive conditions.
- Enhanced Ductility: Increases the ability of the material to deform without fracturing.
- Better Toughness: Improves the material’s ability to absorb energy and resist impact.
Common Heat Treatment Processes
Several heat treatment processes can be applied to lost foam cast components, each offering specific advantages depending on the desired properties and applications.
Annealing
Annealing involves heating the casting to a specific temperature, holding it at that temperature for a period, and then slowly cooling it. This process relieves internal stresses, refines the grain structure, and improves ductility.
- Process: Heating to 600-900°C, holding for several hours, followed by slow cooling.
- Benefits: Reduces internal stresses, increases ductility, refines grain structure.
- Applications: Improves machinability and reduces hardness for components such as gears and engine blocks.
Property | Impact of Annealing |
---|---|
Internal Stress | Reduces internal stresses |
Ductility | Increases ductility |
Grain Structure | Refines grain structure |
Applications | Gears, engine blocks |
Normalizing
Normalizing involves heating the casting to a temperature above its critical range, followed by air cooling. This process produces a uniform microstructure, enhances mechanical properties, and increases toughness.
- Process: Heating to 850-950°C, holding for a period, followed by air cooling.
- Benefits: Produces a uniform microstructure, enhances mechanical properties, increases toughness.
- Applications: Suitable for components requiring improved mechanical properties and structural uniformity, such as machine frames and crankshafts.
Property | Impact of Normalizing |
---|---|
Microstructure | Produces uniform microstructure |
Mechanical Properties | Enhances mechanical properties |
Toughness | Increases toughness |
Applications | Machine frames, crankshafts |
Quenching and Tempering
Quenching involves rapidly cooling the casting from a high temperature by immersing it in a quenching medium such as water, oil, or air. This process increases hardness and strength. Tempering follows quenching and involves reheating the casting to a lower temperature to reduce brittleness and improve toughness.
- Process:
- Quenching: Heating to 850-950°C, followed by rapid cooling in a quenching medium.
- Tempering: Reheating to 250-500°C, holding for a period, followed by air cooling.
- Benefits: Increases hardness and strength, reduces brittleness, improves toughness.
- Applications: Suitable for components that require high hardness and wear resistance, such as wear plates and cutting tools.
Property | Impact of Quenching and Tempering |
---|---|
Hardness | Increases hardness |
Strength | Increases strength |
Brittleness | Reduces brittleness |
Toughness | Improves toughness |
Applications | Wear plates, cutting tools |
Solution Treatment and Aging
Solution treatment involves heating the casting to a high temperature to dissolve alloying elements into a solid solution, followed by rapid cooling to retain the solution. Aging is then performed at a lower temperature to precipitate fine particles, enhancing strength and hardness.
- Process:
- Solution Treatment: Heating to 500-550°C, followed by rapid cooling.
- Aging: Reheating to 150-200°C, holding for a period, followed by air cooling.
- Benefits: Enhances strength and hardness, improves wear resistance.
- Applications: Suitable for aluminum and other non-ferrous alloys used in aerospace and automotive components.
Property | Impact of Solution Treatment and Aging |
---|---|
Strength | Enhances strength |
Hardness | Enhances hardness |
Wear Resistance | Improves wear resistance |
Applications | Aerospace components, automotive components |
Advanced Heat Treatment Techniques
In addition to traditional heat treatment processes, several advanced techniques can further enhance the properties of lost foam cast components.
Induction Hardening
Induction hardening involves using an induction coil to heat the surface of the casting rapidly, followed by immediate quenching. This process increases surface hardness and wear resistance while maintaining a tough core.
- Process: Rapid heating using induction coils, followed by immediate quenching.
- Benefits: Increases surface hardness, improves wear resistance, maintains core toughness.
- Applications: Suitable for components subjected to high surface wear, such as gears and shafts.
Property | Impact of Induction Hardening |
---|---|
Surface Hardness | Increases surface hardness |
Wear Resistance | Improves wear resistance |
Core Toughness | Maintains core toughness |
Applications | Gears, shafts |
Carburizing
Carburizing involves diffusing carbon into the surface layer of the casting at high temperatures, followed by quenching. This process produces a hard, wear-resistant surface while maintaining a ductile core.
- Process: Diffusing carbon into the surface layer at 850-950°C, followed by quenching.
- Benefits: Increases surface hardness, improves wear resistance, maintains core ductility.
- Applications: Suitable for components that require a hard surface and a tough core, such as gears and camshafts.
Property | Impact of Carburizing |
---|---|
Surface Hardness | Increases surface hardness |
Wear Resistance | Improves wear resistance |
Core Ductility | Maintains core ductility |
Applications | Gears, camshafts |
Cryogenic Treatment
Cryogenic treatment involves cooling the casting to extremely low temperatures, typically using liquid nitrogen, followed by slow warming to room temperature. This process enhances wear resistance, dimensional stability, and fatigue strength.
- Process: Cooling to -196°C using liquid nitrogen, followed by slow warming.
- Benefits: Enhances wear resistance, improves dimensional stability, increases fatigue strength.
- Applications: Suitable for high-performance components, such as aerospace parts and cutting tools.
Property | Impact of Cryogenic Treatment |
---|---|
Wear Resistance | Enhances wear resistance |
Dimensional Stability | Improves dimensional stability |
Fatigue Strength | Increases fatigue strength |
Applications | Aerospace parts, cutting tools |
Applications of Heat-Treated Lost Foam Cast Components
Heat-treated lost foam cast components are used in various industries where enhanced mechanical properties are essential.
Automotive Industry
- Engine Blocks: Improved strength and durability through annealing and normalizing.
- Crankshafts: Enhanced toughness and wear resistance through quenching and tempering.
- Brake Discs: Increased hardness and wear resistance through induction hardening.
Aerospace Industry
- Turbine Blades: Enhanced strength and hardness through solution treatment and aging.
- Landing Gear Components: Improved toughness and dimensional stability through cryogenic treatment.
Industrial Machinery
- Gears and Shafts: Increased surface hardness and wear resistance through carburizing and induction hardening.
- Cutting Tools: Enhanced hardness and toughness through quenching and tempering.
Industry | Applications | Heat Treatment Processes |
---|---|---|
Automotive | Engine blocks, crankshafts, brake discs | Annealing, normalizing, quenching and tempering, induction hardening |
Aerospace | Turbine blades, landing gear components | Solution treatment and aging, cryogenic treatment |
Industrial Machinery | Gears, shafts, cutting tools | Carburizing, induction hardening, quenching and tempering |
Conclusion
Heat treatment processes are essential for enhancing the mechanical properties and performance of lost foam cast components. By applying various heat treatment techniques such as annealing, normalizing, quenching and tempering, solution treatment and aging, induction hardening, carburizing, and cryogenic treatment, manufacturers can produce castings with superior strength, hardness, ductility, and toughness. These advancements ensure that lost foam cast components meet the stringent requirements of modern engineering and manufacturing, providing reliable and high-performance solutions for various industries, including automotive, aerospace, and industrial machinery.
Heat Treatment Process | Benefits | Applications |
---|---|---|
Annealing | Reduces internal stresses, increases ductility | Gears, engine blocks |
Normalizing | Produces uniform microstructure, increases toughness | Machine frames, crankshafts |
Quenching and Tempering | Increases hardness and strength, improves toughness | Wear plates, cutting tools |
Solution Treatment and Aging | Enhances strength and hardness, improves wear resistance | Aerospace components, automotive components |
Induction Hardening | Increases surface hardness, improves wear resistance | Gears, shafts |
Carburizing | Increases surface hardness, maintains core ductility | Gears, camshafts |
Cryogenic Treatment | Enhances wear resistance, improves dimensional stability | Aerospace parts, cutting tools |
By focusing on these heat treatment processes, manufacturers can achieve superior results, ensuring high-quality, reliable, and cost-effective lost foam cast components for a wide range of applications.