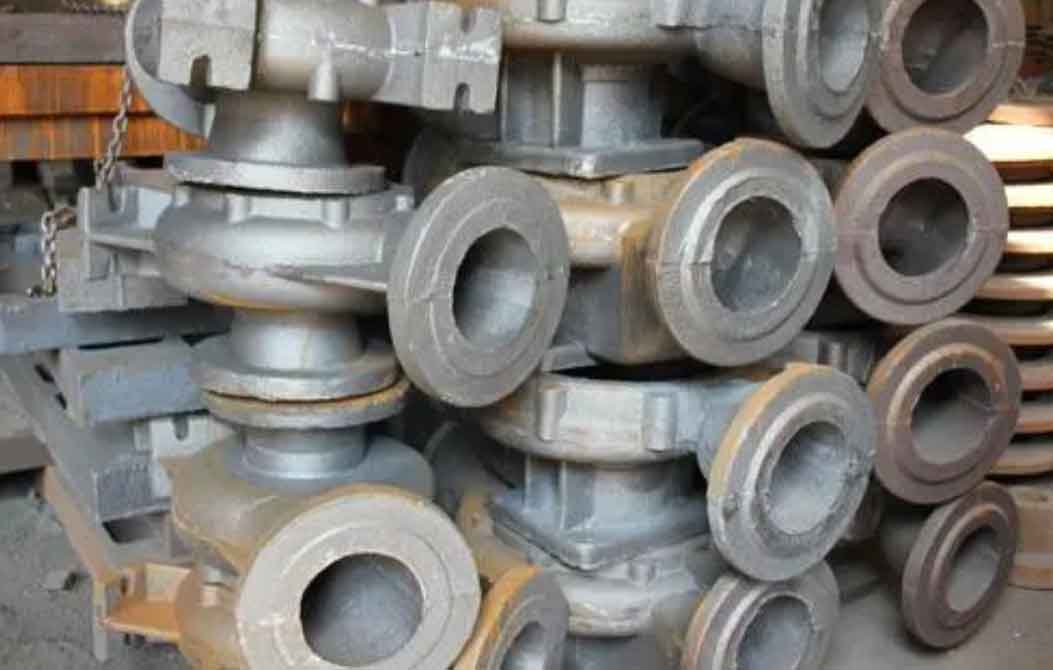
Binders in sand casting processes play a crucial role in ensuring the quality and integrity of the final product. Here’s a breakdown of how binders function and why they are essential in sand casting:
1. What is Sand Casting?
Sand casting is a metal casting process that uses sand as the mold material. The technique involves pouring molten metal into a sand mold, which contains a cavity of the desired shape, and allowing it to solidify.
2. Role of Binders
Binders are substances mixed with the sand to enhance the properties of the mold. Their primary functions include:
- Adhesion: Binders help the sand particles stick together, forming a stable mold that can withstand the pouring and solidification of molten metal.
- Strength: They provide the mold with sufficient strength to maintain its shape and resist the mechanical and thermal stresses during the sand casting process.
- Permeability: Good binders maintain the mold’s permeability, allowing gases formed during the sand casting to escape, which prevents defects in the sand casting.
- Collapsibility: After the metal has solidified, binders should allow the sand mold to collapse easily for easy removal of the sand casting, without causing damage to the cast.
3. Types of Binders
Binders can be organic, inorganic, or a combination of both, and each type has its benefits and applications:
- Organic binders (like resins) are popular for their strength and moldability but can produce more gases during sand casting.
- Inorganic binders (such as clay, silica, or water glass) are chosen for lower gas production and higher thermal stability but might offer less collapsibility.
- Hybrid binders combine the properties of both organic and inorganic types to optimize performance.
4. Selection Criteria
Choosing the right binder depends on several factors:
- Casting metal: Different metals and their melting temperatures can influence the choice of binder due to the different thermal resistances required.
- Mold complexity: More intricate molds may require binders that offer greater detail accuracy and strength.
- Environmental and health considerations: Some binders, particularly certain organic types, can be toxic or environmentally harmful when burned off during sand casting.
5. Current Trends and Innovations
Advancements in binder technology continue to improve their environmental footprint, effectiveness, and cost-efficiency. For example, developments in biodegradable and less toxic binders are becoming more prevalent in response to environmental concerns.
6. Performance Testing and Optimization
To ensure that binders are performing adequately for their intended application in sand casting, rigorous testing and optimization are conducted. This involves:
- Green Strength Testing: Measures the strength of the sand-binder mixture before it is exposed to any heat. This is crucial for handling and maintaining mold integrity during the setup.
- Hot Strength Testing: Evaluates the mold’s ability to withstand the high temperatures of molten metal without deforming or cracking.
- Gas Permeability Testing: Assesses how well gases can escape through the mold. Poor permeability can lead to defects such as blowholes in the final sand casting.
- Collapsibility Testing: Determines how easily the mold can be broken away from the finished sand casting without damaging it. This is particularly important in automated sand casting processes where quick mold removal is necessary.
7. Environmental Impact
The environmental impact of binders is a significant consideration in modern foundries. Traditional organic binders, such as certain phenolic resins, can emit volatile organic compounds (VOCs) and other hazardous substances when heated. Efforts to mitigate these impacts include:
- Development of Low-VOC Binders: New formulations are designed to reduce harmful emissions.
- Recycling of Sand and Binders: Techniques to reclaim and reuse sand and residual binders reduce waste and environmental degradation.
- Regulatory Compliance: Adherence to international standards and environmental regulations ensures that foundries minimize their ecological footprint.
8. Cost Factors
Cost is always a pivotal factor in the selection of binders. Factors affecting the cost include:
- Material Costs: Some high-performance binders can be significantly more expensive than traditional materials.
- Operational Costs: The efficiency of the binder (in terms of required quantities and processing times) can impact overall production costs.
- Waste Disposal Costs: The costs associated with disposing of used binders and sand can vary greatly depending on the type of binder used and local regulatory requirements.
9. Future Directions
The future of binders in sand casting looks toward more sustainable and efficient solutions. Innovations may include:
- Nano-technology Binders: Utilizing nano-scale materials to enhance binder performance and reduce the amount of binder needed.
- Smart Binders: Development of binders that change properties in response to different stages of sand casting process, improving performance and reducing waste.
- Integrated Process Optimization: Advanced simulation tools that integrate binder characteristics into sand casting process design to optimize quality and efficiency from the outset.
Conclusion
Binders are a vital component of the sand casting process, influencing everything from the quality of the final product to the environmental impact of the production process. As the industry continues to evolve, the development of more sophisticated and environmentally friendly binders remains a key area of focus. This ongoing innovation will help ensure that sand casting remains a viable and efficient method for metal forming in various industrial applications.
Understanding the role of binders in sand casting is essential for optimizing sand casting process, improving the quality of the final product, and addressing environmental and safety issues. Binders are selected based on their ability to meet the specific requirements of each sand casting project, balancing factors like strength, gas production, and mold breakdown.