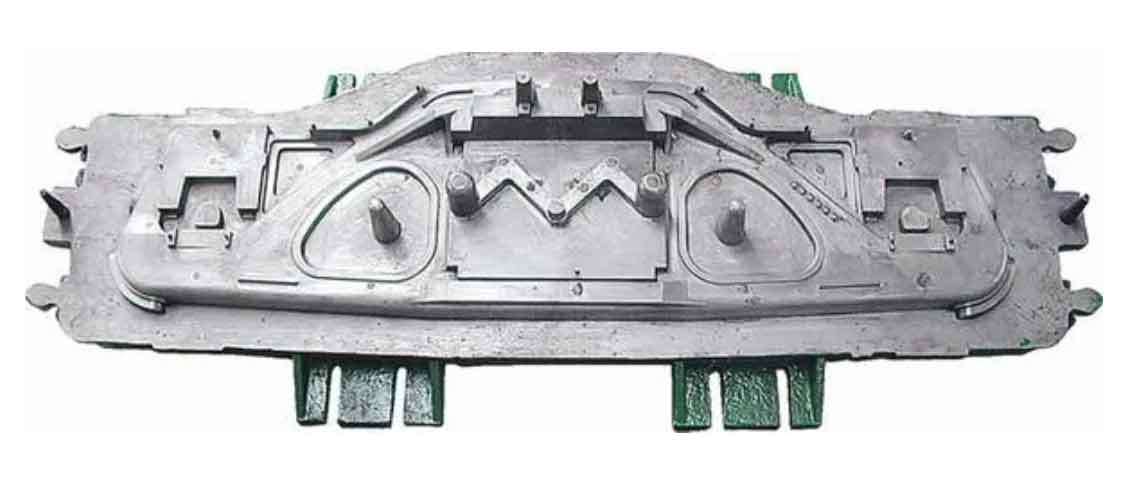
Improving the quality of castings through advanced sand casting techniques involves several innovative approaches and practices that can significantly enhance the properties of the final cast products. Here’s an overview of some key methods and their benefits:
- Optimized Sand Composition and Additives:
- High-quality sand: Using finer and more uniform sand grains can reduce flaws like porosity and surface roughness in the final sand casting.
- Binders and additives: Modern binders and additives can improve the sand’s strength and thermal stability, which helps in producing more accurate and detailed sand casting.
- Advanced Molding Techniques:
- Precision molding: Techniques like 3D printing of sand molds allow for creating complex geometries with high precision that were not feasible with traditional sand casting methods.
- Controlled filling and solidification: Advanced methods to control the metal filling and cooling processes can minimize defects like air entrapment and uneven texture.
- Improved Mold and Core Making Technologies:
- Core stability and gas permeability: Using advanced core making technologies that ensure the cores are stable and have good gas permeability can reduce common defects such as gas porosity and shrinkage.
- Thermal and Mechanical Reclamation of Sand:
- Reclamation systems: Modern sand reclamation systems not only reduce the cost by recycling the sand but also maintain the consistency of sand properties, which is crucial for achieving high-quality sand casting.
- Simulation and Modeling:
- Predictive modeling: Utilizing computer simulations to predict mold filling, cooling, and solidification can help in pre-identifying potential problem areas and adjusting the parameters to optimize the quality of sand casting.
- Quality Control and Testing:
- Real-time monitoring: Technologies such as sensors and real-time imaging can monitor sand casting process closely and allow for immediate adjustments to improve the outcome.
- Post-casting analysis: Advanced imaging and scanning technologies can assess the internal and external quality of sand casting without destructive testing.
- Enhanced Environmental Controls:
- Humidity and temperature control: Maintaining a controlled environment around sand casting area can greatly influence the behavior of the sand and metal. Proper humidity and temperature controls prevent the sand from drying out or becoming too moist, which can affect the mold’s integrity.
- Clean environment: Keeping sand casting environment clean and free from contaminants ensures that the sand and metal are not adulterated, which helps in producing higher-quality sand casting.
- Automation and Robotics:
- Robotic sand handling and mold making: Automation in the form of robotics can be used for sand mixing, mold making, and core setting, which increases consistency and precision while reducing human error and labor costs.
- Automated pouring systems: These systems can control the rate and volume of metal poured into molds, reducing turbulence and the potential for air entrapment and other defects.
- Metallurgical Enhancements:
- Alloy composition: Adjusting the metallurgical composition of sand casting material can improve its properties, such as strength, ductility, and resistance to wear and corrosion.
- Treatment of the molten metal: Techniques such as degassing, filtration, and modification of the melt before pouring can remove impurities and enhance the metal’s quality.
- Post-Processing Treatments:
- Heat treatment: Applying various heat treatments can alter the microstructure of the metal, enhancing its mechanical properties and performance.
- Surface finishing: Techniques like shot blasting, grinding, and polishing not only improve the aesthetic appearance of sand casting but also remove surface imperfections, increasing fatigue strength and overall durability.
- Personnel Training and Development:
- Skill development: Regular training programs for workers on the latest sand casting technologies and quality control methods can ensure high standards are maintained throughout sand casting process.
- Safety training: Adequate training in handling materials and equipment safely is essential to prevent accidents and ensure the consistent quality of sand casting.
- Collaborative Research and Development:
- Industry partnerships: Collaborating with universities and research institutions can lead to innovations in sand casting processes and materials.
- Continuous improvement: A focus on continuous improvement through research can help in discovering new methods and technologies that can further refine sand casting process and improve the quality of the final products.
- Integration of IoT and Data Analytics:
- Smart sensors and IoT devices: Embedding sensors in molds and equipment can provide real-time data on various parameters like temperature, pressure, and humidity. This data can be analyzed to optimize processes and predict maintenance needs.
- Data-driven decision making: Using analytics to process the vast amounts of data collected during sand casting process can help in identifying patterns and predicting potential defects before they occur, allowing for preemptive adjustments.
- Use of Sustainable Materials and Practices:
- Eco-friendly binders and additives: Shifting towards more environmentally friendly materials for binders and other mold additives can reduce harmful emissions and waste.
- Recycling and waste management: Implementing robust recycling programs for sand and metal scraps and optimizing the use of materials can minimize environmental impact and reduce costs.
- Enhanced Quality Assurance Protocols:
- Standardization of processes: Establishing standardized procedures across all stages of the sand casting process ensures consistency and reliability in the quality of sand casting.
- Certification and compliance: Achieving certifications like ISO and adhering to industry standards can not only improve process quality but also enhance market credibility and customer trust.
- Advanced Defect Detection Techniques:
- Non-destructive testing (NDT): Techniques such as ultrasonic testing, X-ray, and magnetic particle inspection provide in-depth insights into the internal integrity of sand casting without damaging them.
- Machine learning for defect recognition: Implementing machine learning algorithms to analyze images and data from NDT can quickly identify defects that might not be visible to the human eye.
- Optimized Design for Manufacturing:
- Simulation-driven design: Utilizing simulations to assess the manufacturability of designs can help in modifying them to optimize material usage and minimize defects during sand casting.
- Collaboration between design and manufacturing teams: Encouraging early and ongoing collaboration between these teams ensures that designs are practical to manufacture and meet quality standards.
- Customer-Centric Innovations:
- Customization options: Offering customized mold designs and material choices can meet specific customer needs and open up new market opportunities.
- Feedback loops: Establishing direct channels for customer feedback on sand casting products can help in continuous product improvement and customer satisfaction.
Implementing these advanced sand casting techniques can significantly enhance the efficiency of sand casting process and the performance characteristics of the cast products, making them suitable for more demanding applications. By embracing these advanced strategies, the sand casting industry can not only achieve superior quality in its products but also drive innovation, efficiency, and sustainability in its operations. This comprehensive approach ensures that sand casting remains a competitive and valuable process in the modern manufacturing landscape.
These advanced techniques and practices in sand casting not only aim to improve the quality and performance of sand casting but also contribute to more sustainable and cost-effective manufacturing processes. By integrating these advancements, foundries can meet higher standards and expand into new markets with more complex and high-performance products.