Abstract:
This comprehensive article delves into the complexities of sand adhesion during the wet sand casting process, focusing specifically on wet sand casting parts. Through detailed analysis and practical solutions, we aim to provide insights into the root causes of sand adhesion and present effective measures to mitigate this issue. Tables and visual aids are utilized throughout to enhance clarity and readability.
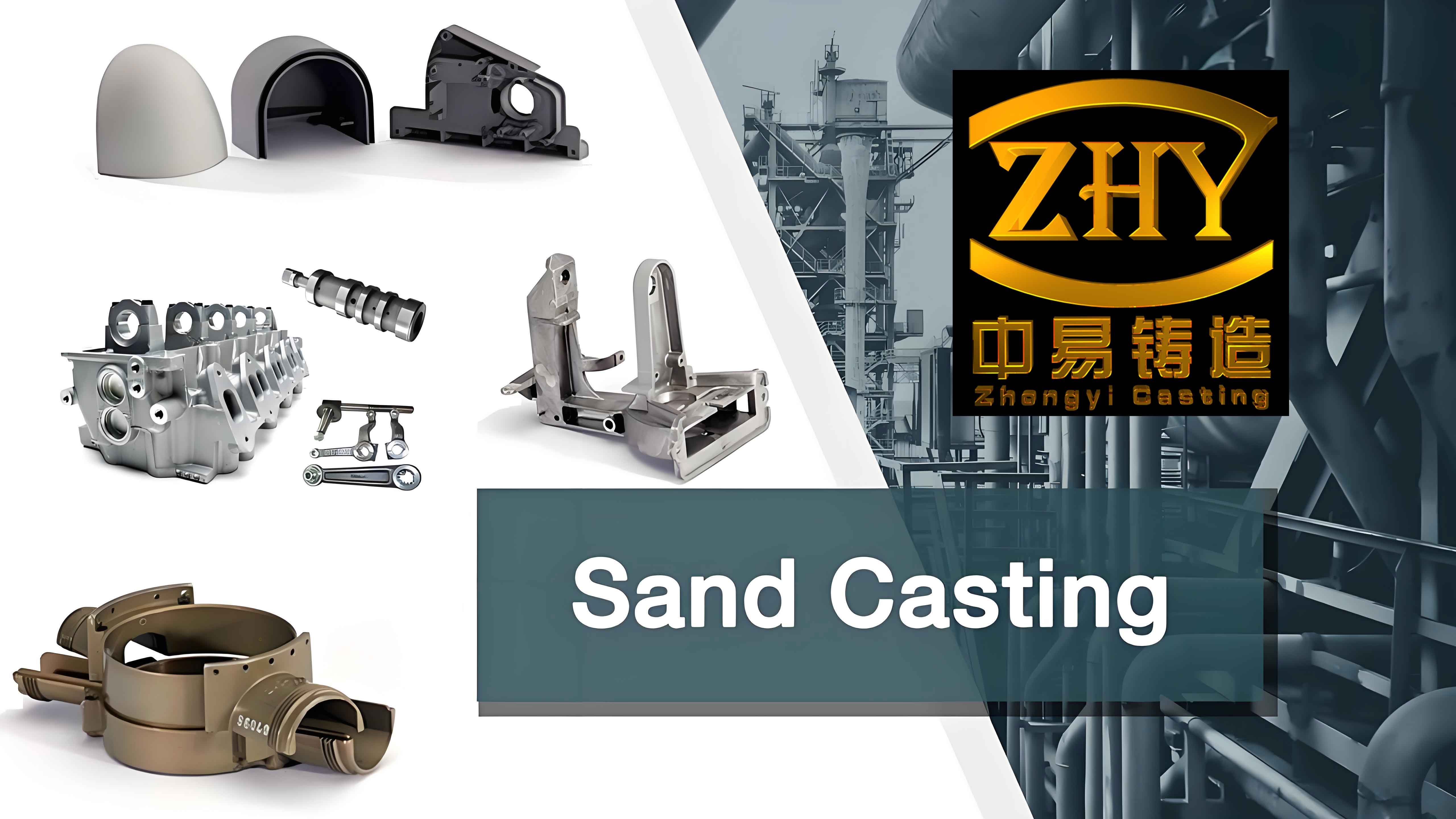
1. Introduction
Wet sand casting is a widely used manufacturing process for producing metal parts, particularly in the automotive and engineering industries. Despite its numerous advantages, sand adhesion remains a significant challenge that can compromise the surface quality and dimensional accuracy of castings. This article explores the underlying mechanisms of sand adhesion in wet sand casting parts and outlines various strategies for mitigating this issue.
1.1 Background on Wet Sand Casting
Wet sand casting involves pouring molten metal into a mold made from a mixture of sand, clay, and water. The process is versatile and cost-effective, allowing for the production of complex-shaped parts. However, sand adhesion, a phenomenon where molten metal adheres to the sand mold, can significantly impact the quality and performance of the final product.
1.2 Importance of Addressing Sand Adhesion
Sand adhesion not only increases the post-processing effort required to clean the casting surface but also reduces the overall quality and dimensional accuracy of the part. In severe cases, it can even lead to scrap, resulting in financial losses and production delays. Therefore, it is imperative to understand the causes of sand adhesion and implement effective preventive measures.
2. Causes of Sand Adhesion
Sand adhesion in wet sand casting parts can be attributed to various factors, including the properties of the sand mix, the casting process parameters, and the design of the mold.
2.1 Properties of Sand Mix
- Particle Size Distribution: Coarse-grained sand with large pore spaces increases the risk of metal penetration and adhesion.
- Refractoriness: Insufficient refractoriness can lead to early breakdown of the sand mold under the high temperatures of the molten metal.
- Moisture Content: Excess moisture can cause steam explosions within the mold, forcing metal into the pores and promoting adhesion.
- Binder Content: The type and quantity of binder used affect the mold’s strength and permeability, influencing the likelihood of adhesion.
Table 1: Key Properties of Sand Mix Affecting Adhesion
Property | Impact on Adhesion |
---|---|
Particle Size | Coarse grains ↑ adhesion risk |
Refractoriness | Low refractoriness ↑ mold breakdown, ↑ adhesion risk |
Moisture Content | High moisture ↑ steam explosions, ↑ metal penetration, ↑ adhesion |
Binder Content | Insufficient binder ↓ mold strength, ↑ adhesion risk |
2.2 Casting Process Parameters
- Pouring Temperature: Higher pouring temperatures can enhance metal flowability but also increase the likelihood of sand adhesion due to higher thermal stresses and longer metal contact times.
- Metal Superheat: Excessive superheat can lead to increased metal turbulence and penetration into the sand mold.
- Gating and Riser Design: Poor gating and riser design can result in uneven metal flow and localized hot spots, promoting sand adhesion.
Table 2: Casting Process Parameters Affecting Adhesion
Parameter | Impact on Adhesion |
---|---|
Pouring Temperature | High temperature ↑ metal flowability, ↑ thermal stresses, ↑ adhesion |
Metal Superheat | Excessive superheat ↑ metal turbulence, ↑ penetration, ↑ adhesion |
Gating & Riser Design | Poor design ↓ metal flow control, ↑ hot spots, ↑ adhesion risk |
2.3 Mold Design and Construction
- Mold Complexity: Highly complex molds with intricate undercuts and thin walls are more prone to sand adhesion.
- Exhaust System: Inefficient exhaust systems can trap gases within the mold, causing steam explosions and promoting adhesion.
- Sand Compaction: Inadequate compaction reduces mold strength and increases porosity, leading to higher adhesion risks.
Table 3: Mold Design and Construction Factors Affecting Adhesion
Factor | Impact on Adhesion |
---|---|
Mold Complexity | High complexity ↑ adhesion risk due to undercuts, thin walls |
Exhaust System | Inefficient system ↑ gas trapping, ↑ steam explosions, ↑ adhesion |
Sand Compaction | Inadequate compaction ↓ mold strength, ↑ porosity, ↑ adhesion risk |
3. Strategies to Mitigate Sand Adhesion
To effectively address sand adhesion in wet sand casting parts, a multifaceted approach that considers sand mix optimization, process parameter adjustment, and mold design improvements is necessary.
3.1 Optimizing Sand Mix Properties
- Multi-Screened Sand: Use multi-screened sand with a finer particle size distribution to reduce pore spaces and penetration risks.
- High-Refractoriness Sand: Incorporate high-refractoriness sand to enhance mold stability under high temperatures.
- Controlled Moisture Content: Maintain optimal moisture levels to prevent steam explosions without compromising mold compaction.
- Binder Selection and Quantity: Select appropriate binders and optimize their quantity to balance mold strength and permeability.
Table 4: Optimized Sand Mix Properties
Optimized Property | Recommended Guidelines |
---|---|
Particle Size | Use multi-screened sand with finer particle distribution |
Refractoriness | Incorporate high-refractoriness sand |
Moisture Content | Maintain optimal moisture levels (e.g., 3-5%) |
Binder Selection | Use appropriate binders based on casting requirements |
Binder Quantity | Optimize quantity to balance strength and permeability |
3.2 Adjusting Casting Process Parameters
- Optimized Pouring Temperature: Determine the optimal pouring temperature based on the metal’s properties and casting design to balance flowability and adhesion risks.
- Controlled Metal Superheat: Maintain metal at the required superheat level to ensure smooth flow without excessive turbulence.
- Efficient Gating and Riser Design: Design effective gating and riser systems to control metal flow and minimize hot spots.
Table 5: Adjusted Casting Process Parameters
Parameter | Recommended Approach |
---|---|
Pouring Temperature | Optimize based on metal properties and casting design |
Metal Superheat | Maintain at required level for smooth flow without turbulence |
Gating & Riser Design | Design effective systems for controlled metal flow |
3.3 Improving Mold Design and Construction
- Simplified Mold Geometry: Where possible, simplify mold geometry to reduce adhesion risks associated with undercuts and thin walls.
- Efficient Exhaust System: Design and implement efficient exhaust systems to prevent gas trapping and steam explosions.
- Adequate Sand Compaction: Ensure thorough sand compaction to improve mold strength and reduce porosity.
Table 6: Improved Mold Design and Construction Factors
Factor | Recommended Approach |
---|---|
Mold Complexity | Simplify geometry where feasible to reduce adhesion risks |
Exhaust System | Design and implement efficient exhaust systems |
Sand Compaction | Ensure thorough compaction for improved mold strength and reduced porosity |
4. Case Study: Mitigating Sand Adhesion in Engine Block Casting
To illustrate the effectiveness of the proposed strategies, let’s consider a case study involving the production of an engine block casting using wet sand casting.
4.1 Initial Challenges
The initial production runs experienced significant sand adhesion issues, particularly in the complex undercut regions of the casting. This resulted in extended post-processing times, increased scrap rates, and customer complaints regarding surface quality.
4.2 Applied Strategies
To address these challenges, the following strategies were implemented:
- Optimized Sand Mix: Multi-screened sand with a finer particle size distribution was used, along with high-refractoriness sand to enhance mold stability. Moisture content was maintained at optimal levels, and an appropriate binder selection and quantity were determined.
- Adjusted Casting Parameters: Pouring temperature was optimized based on the casting metal’s properties, and metal superheat was carefully controlled. Effective gating and riser systems were designed to improve metal flow control.
- Improved Mold Design: The mold geometry was simplified where possible, and an efficient exhaust system was implemented to prevent gas trapping and steam explosions. Adequate sand compaction was ensured during mold construction.
4.3 Results
After implementing the proposed strategies, the engine block casting process experienced a significant reduction in sand adhesion. Post-processing times decreased, scrap rates dropped, and customer satisfaction improved significantly. The optimized sand mix, adjusted casting parameters, and improved mold design collectively contributed to the successful mitigation of sand adhesion in this case study.
5. Conclusion
Sand adhesion in wet sand casting parts is a complex issue influenced by various factors, including sand mix properties, casting process parameters, and mold design. By optimizing sand mix properties, adjusting casting process parameters, and improving mold design, it is possible to effectively mitigate sand adhesion and enhance the quality and performance of castings. This comprehensive approach ensures that wet sand casting remains a viable and cost-effective manufacturing process for producing high-quality metal parts.