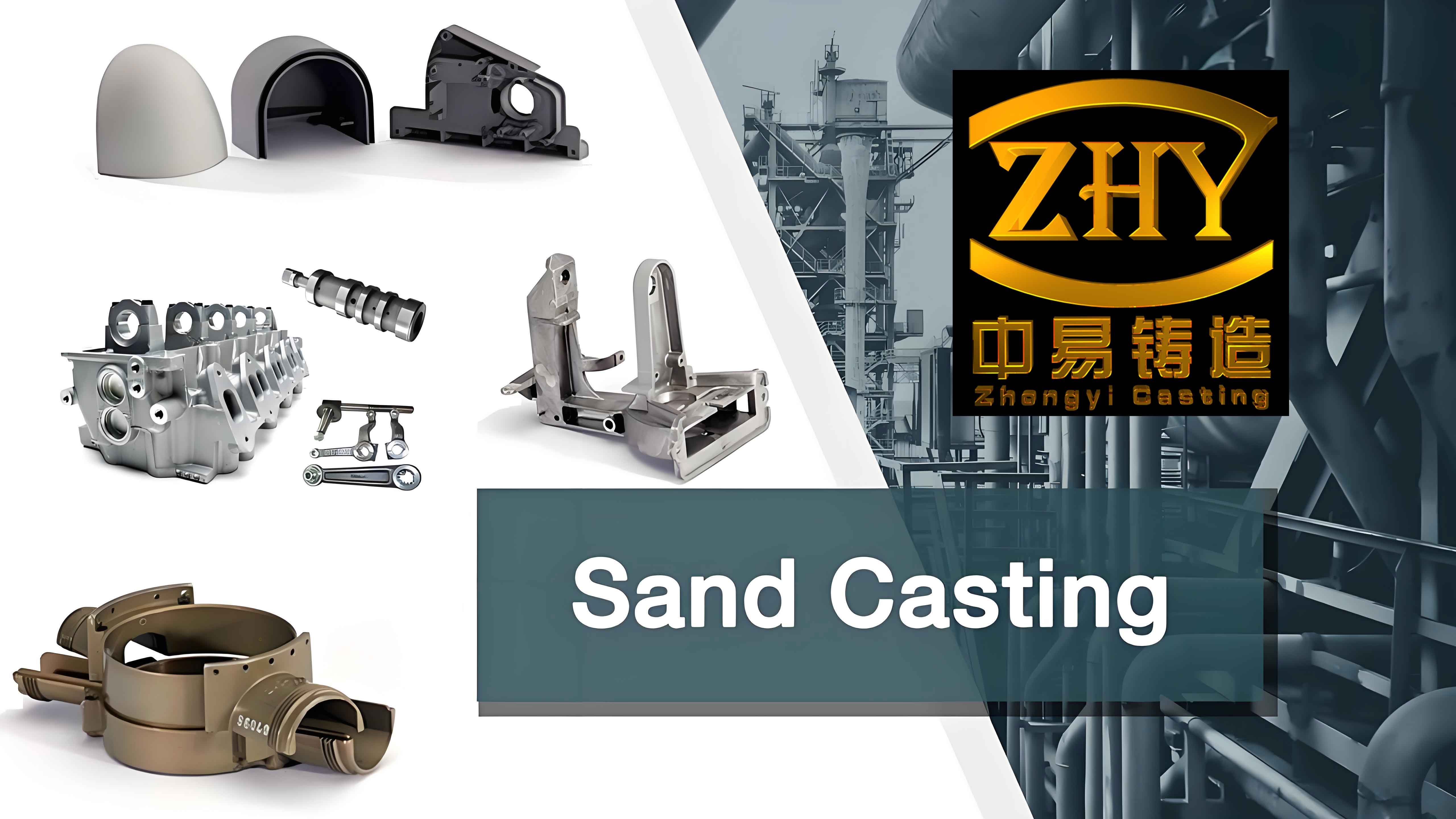
1. Introduction
Sand casting remains one of the most widely used manufacturing processes for producing complex metal components, especially sand casting parts such as automotive wheel hubs, clutch assemblies, and industrial valve bodies. Despite its versatility, traditional sand casting methods face challenges like unstable mold transportation, low recycling efficiency of auxiliary equipment, high labor intensity, and suboptimal production line integration. To address these issues, this article presents the design and implementation of a fully automated horizontal parting molding line tailored for sand casting parts, focusing on structural simplicity, high productivity, and resource efficiency.
2. Design Objectives
The primary goals of the automated molding line include:
- Improved Production Efficiency: Achieve an annual output of 12,000 tons (440,000 molds/year) for sand casting parts.
- Enhanced Precision: Ensure a 90%+ yield rate by minimizing mold misalignment and sand defects.
- Automation: Reduce manual intervention from 32 workers to 4 per shift through PLC-controlled operations.
- Resource Optimization: Enable 100% recycling of sand and reusable flasks.
- Flexibility: Accommodate sand molds with variable heights (280–560 mm) and weights (20–40 kg).
3. System Layout and Workflow
3.1 Production Line Layout
The automated horizontal parting molding line comprises four conveyor tracks and six core subsystems:
- Molding System: Dual horizontal parting machines with adjustable sand thickness.
- Flask & Weight Transfer Unit: Ensures precise positioning and recycling of flasks.
- Pallet Clamping & Transfer Mechanism: Facilitates stable mold transportation.
- Sand Recycling System: Collects and reuses residual sand via belt conveyors.
- Pouring & Cooling Zone: Automated pouring machines and dual cooling conveyors.
- Shakeout & Casting Extraction: Vibratory feeders separate sand casting parts from molds.
Table 1: Key Components of the Molding Line
Component | Function | Key Features |
---|---|---|
Horizontal Parting Machine | Forms upper/lower mold halves | Adjustable sand thickness; PLC-controlled |
Flask Transfer Device | Cycles flasks between stations | Dual升降气缸; Precision sensors |
Pallet Clamping Unit | Secures pallets during transport | Adaptive gripping force; 4-axis alignment |
Sand Recycling Belt | Collects and transports waste sand | 15 m³/h capacity; Dust suppression |
3.2 Workflow Overview
The fully automated process involves 10 cyclic steps:
- Sand Supply: Level sensors trigger sand delivery to molding machines.
- Mold Formation: Compressed air injects sand into flasks, followed by compaction.
- Pallet Transfer: Clamped pallets move to the pouring station.
- Flask & Weight Attachment: Automated arms secure flasks and weights.
- Metal Pouring: Robotic ladles fill molds with molten metal.
- Cooling: Conveyors transport molds through a 30-minute cooling zone.
- Flask Removal: Weights and flasks are detached for reuse.
- Shakeout: Vibratory feeders separate sand casting parts from sand.
- Sand Recycling: Collected sand is filtered and returned to storage.
- Part Extraction: Castings are cleaned and inspected.
4. Critical Mechanical Designs
4.1 Horizontal Parting Machine
The molding system employs dual射砂头 (sand shooters) to fill flasks, followed by hydraulic compaction (force F=P×AF=P×A, where PP = pressure, AA = piston area). Key parameters:
- Sand Injection Pressure: 0.6–0.8 MPa
- Compaction Force: 120 kN
- Cycle Time: 45 seconds/mold
Table 2: Performance Metrics of Molding Machine
Parameter | Value |
---|---|
Max. Mold Size (L×W×H) | 670×610×560 mm |
Sand Consumption/Mold | 18–22 kg |
Energy Consumption | 15 kW/h |
4.2 Flask & Weight Transfer Unit
This subsystem uses servo-driven升降气缸 to position flasks with ±0.5 mm accuracy. The mechanism includes:
- Clamping Force: Fc=2×μ×NFc=2×μ×N (μ = friction coefficient, N = normal force)
- Cycle Time: 20 seconds/flask
Table 3: Flask Transfer Specifications
Metric | Value |
---|---|
Flask Weight Capacity | 80 kg |
Positioning Accuracy | ±0.5 mm |
Motor Power | 3 kW |
4.3 Pallet Clamping Mechanism
A four-arm gripper with adaptive force control ensures pallet stability during high-speed transfers. The grip force is adjusted based on pallet weight (WW):
Fg=k×WFg=k×W
where kk = safety factor (1.2–1.5).
5. Control System Architecture
5.1 PLC-Based Automation
The Mitsubishi FX5U PLC coordinates all subsystems via a CC-Link network. Key I/O modules include:
- Inputs: 32 sensors (proximity, optical, pressure)
- Outputs: 24 actuators (servo motors, valves, conveyors)
Table 4: PLC I/O Configuration
Module | Function | Address Range |
---|---|---|
AJ65SBTB1-16D | Digital Inputs (sensors) | X0–X37 |
AJ65SBTB2N-16R | Digital Outputs (actuators) | Y0–Y37 |
FX5U-80MT | Central Processing Unit | — |
5.2 Hydraulic & Pneumatic Systems
- Hydraulic Circuits: 6 independent loops for mold clamping, ejection, and compaction.
- Pneumatic Actuators: 3 cylinders for sand injection, controlled via proportional valves.
Table 5: Hydraulic System Parameters
Component | Pressure (MPa) | Flow Rate (L/min) |
---|---|---|
Mold Clamping Cylinder | 12 | 25 |
Ejection Cylinder | 8 | 18 |
6. Performance Analysis
6.1 Production Metrics
After implementing the automated line, significant improvements were observed:
Table 6: Comparison of Manual vs. Automated Production
Metric | Manual Process | Automated Line | Improvement |
---|---|---|---|
Labor per Shift | 16 | 2 | 87.5% ↓ |
Daily Output (Parts) | 640 | 1,040 | 61.1% ↑ |
Defect Rate | 5.2% | 0.6% | 88.5% ↓ |
Energy Consumption | 220 kWh | 180 kWh | 18.2% ↓ |
6.2 Economic Benefits
- Labor Cost Reduction: Annual savings of 320,000(assuming320,000(assuming15/hour wage).
- Space Utilization: 22.1% smaller footprint compared to manual lines.
- ROI: Payback period < 2 years due to higher throughput and lower scrap rates.
7. Challenges and Solutions
7.1 Sand Reclamation Efficiency
Initial trials showed 12% sand loss due to incomplete recycling. This was mitigated by:
- Installing a secondary筛分机 (screening machine) with 0.5 mm mesh.
- Optimizing conveyor speeds to reduce spillage.
7.2 Mold Misalignment
Occasional flask shifts (±1.2 mm) were resolved by:
- Adding laser alignment sensors to the transfer unit.
- Redesigning flask定位孔 (dowel holes) for tighter tolerances.
8. Future Enhancements
- AI-Driven Predictive Maintenance: Integrating vibration sensors to forecast equipment wear.
- Hybrid Energy Systems: Solar panels to offset 30% of energy demand.
- IoT Integration: Real-time monitoring of sand casting parts quality via thermal cameras.
9. Conclusion
The fully automated horizontal parting molding line demonstrates remarkable efficacy in producing high-quality sand casting parts with minimal human intervention. By integrating precision mechanics, PLC controls, and optimized workflows, the system achieves a 61.1% boost in productivity, 88.5% lower defect rates, and significant cost savings. This design not only addresses the limitations of traditional sand casting but also sets a benchmark for smart foundry solutions in the Industry 4.0 era.