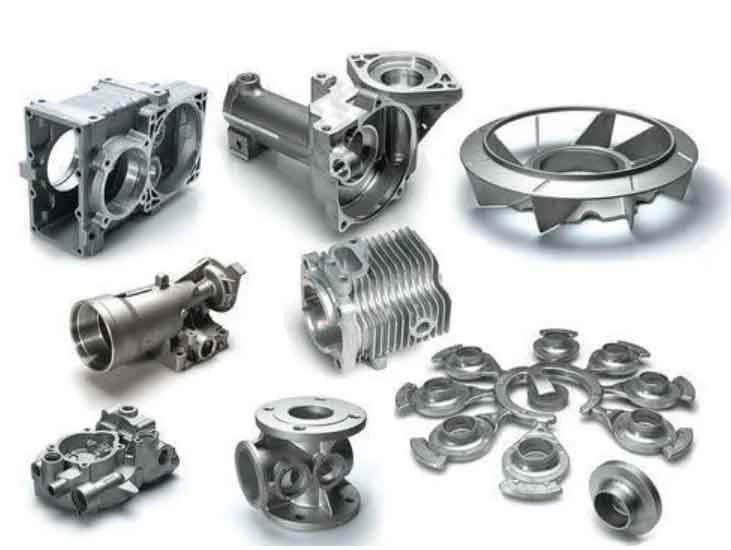
The casting process for grey cast iron components involves several steps to create intricate shapes and structures with the desired microstructure. It is a versatile and widely used method for producing a wide range of industrial components. Let’s take a closer look at the casting process for grey cast iron:
1. Pattern Making:
The process begins with pattern making. A pattern is a replica of the final component and is typically made from wood, metal, or plastic. The pattern is used to create the mold cavity and represents the shape and features of the grey cast iron component.
2. Mold Preparation:
The pattern is placed in a flask, and a molding material is packed around it to create the mold. For grey cast iron, molding materials such as green sand or resin-coated sand are commonly used. Green sand consists of silica sand mixed with a binder and moisture, while resin-coated sand has a layer of resin to improve mold strength and dimensional accuracy.
3. Mold Assembly:
The mold is assembled in a two-part flask to form the cope (upper part) and the drag (lower part). The cope and drag are separated by a parting line, and the gating system is integrated into the mold to facilitate the flow of molten metal.
4. Molten Iron Pouring:
Molten grey cast iron is poured into the mold through the gating system. The metal fills the mold cavity, including all the intricate details present in the pattern. The mold is designed to accommodate shrinkage as the molten metal cools and solidifies.
5. Solidification and Cooling:
After pouring, the molten metal begins to solidify in the mold. As the metal cools, the graphite flakes form due to the presence of silicon in the alloy. The cooling rate and the mold material influence the size and shape of the graphite flakes, which, in turn, affect the material’s properties.
6. Shakeout and Cleaning:
Once the metal has completely solidified, the mold is removed, and the grey cast iron component is extracted. This process is known as shakeout. The component is then cleaned to remove any residual sand, mold coatings, or other impurities.
7. Heat Treatment (Optional):
In some cases, grey cast iron components undergo heat treatment to modify their microstructure and properties. Heat treatment processes like annealing, normalizing, or stress relieving may be employed to achieve specific mechanical characteristics.
8. Machining and Finishing (Optional):
Depending on the complexity of the component and the required tolerances, some grey cast iron components may undergo additional machining and finishing processes to achieve the final dimensions and surface characteristics.
9. Inspection and Quality Control:
Each grey cast iron component is thoroughly inspected to ensure it meets the required specifications and quality standards. Dimensional accuracy, surface finish, and mechanical properties are checked to verify the component’s integrity and suitability for its intended application.
The casting process for grey cast iron components is a well-established and efficient method for producing a wide variety of industrial parts. Its versatility and ability to create intricate shapes with excellent wear resistance and damping capacity have contributed to its widespread usage in diverse industries.