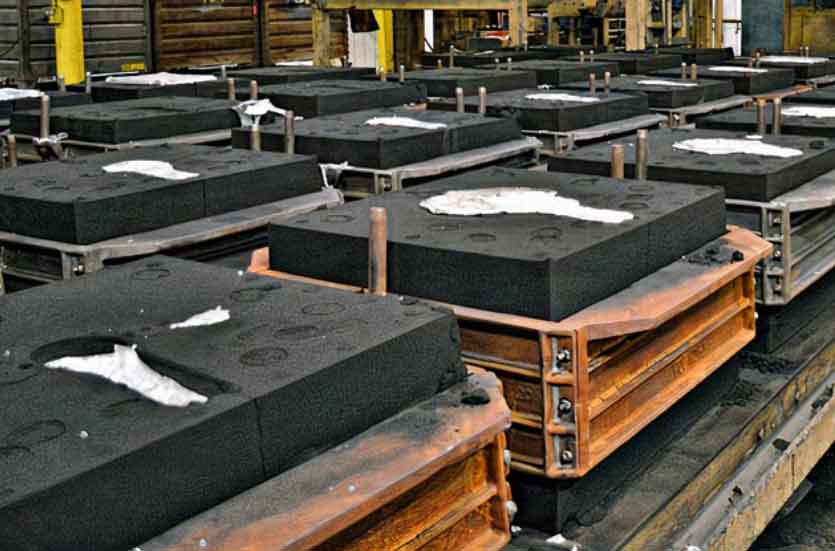
Achieving precision and detail in resin sand casting requires careful attention to best practices and the application of specific techniques. Here are some tips to help you achieve optimal results:
1. Pattern Design and Construction:
- Ensure that the pattern design incorporates the desired precision and detail. Consider using computer-aided design (CAD) software to create accurate and intricate patterns.
- Use high-quality pattern materials such as hardwood, plastic, or metal to achieve precise dimensions and avoid distortion during the molding process.
- Pay attention to draft angles and undercuts to facilitate pattern removal from the sand mold without damaging intricate features.
2. Mold Preparation:
- Use high-quality sand with fine grain size and good flowability to capture the intricate details of the pattern accurately.
- Use high-quality resin binders that provide good strength and ensure the mold maintains its shape during handling and pouring.
- Properly compact the sand mixture around the pattern to ensure uniform density and eliminate air pockets.
3. Venting and Gating:
- Incorporate an effective venting system to allow gases to escape during the casting process. Proper vent placement ensures complete mold filling and reduces the risk of defects.
- Design an efficient gating system to promote smooth and controlled metal flow into the mold cavity. A well-designed gating system helps maintain the desired precision and minimizes turbulence during pouring.
4. Pouring Techniques:
- Maintain the appropriate pouring temperature for the metal being cast to achieve good flowability and minimize the risk of defects.
- Use a controlled pouring rate to ensure a smooth and consistent flow of molten metal into the mold cavity.
- Consider the use of filters or other techniques to remove impurities and ensure clean metal filling, which contributes to better precision and detail.
5. Cooling and Solidification Control:
- Control the cooling rate to ensure proper solidification of the metal and minimize the risk of shrinkage or distortion. This can be achieved through the strategic placement of chills or the implementation of controlled cooling techniques.
- Consider the use of insulating materials or coatings to ensure even cooling and reduce the likelihood of thermal stresses.
6. Post-Casting Processing:
- Perform careful shakeout and cleaning of the casting to remove residual sand and other debris.
- Implement appropriate post-casting processes, such as heat treatment or surface finishing, to enhance the precision and detail of the final product.
- Inspect the castings thoroughly to ensure dimensional accuracy and the desired level of detail.
7. Continuous Improvement and Collaboration:
- Embrace continuous improvement by analyzing the casting process, identifying areas for enhancement, and implementing necessary changes to achieve higher precision and detail.
- Foster collaboration between pattern designers, molders, and metallurgical experts to exchange knowledge and refine techniques for achieving precision and detail.
By following these best practices and tips, you can enhance the precision and detail achieved in resin sand casting. Paying attention to pattern design, mold preparation, venting, gating, pouring techniques, cooling control, post-casting processes, and continuous improvement will help you consistently achieve high-quality castings with intricate and precise features.