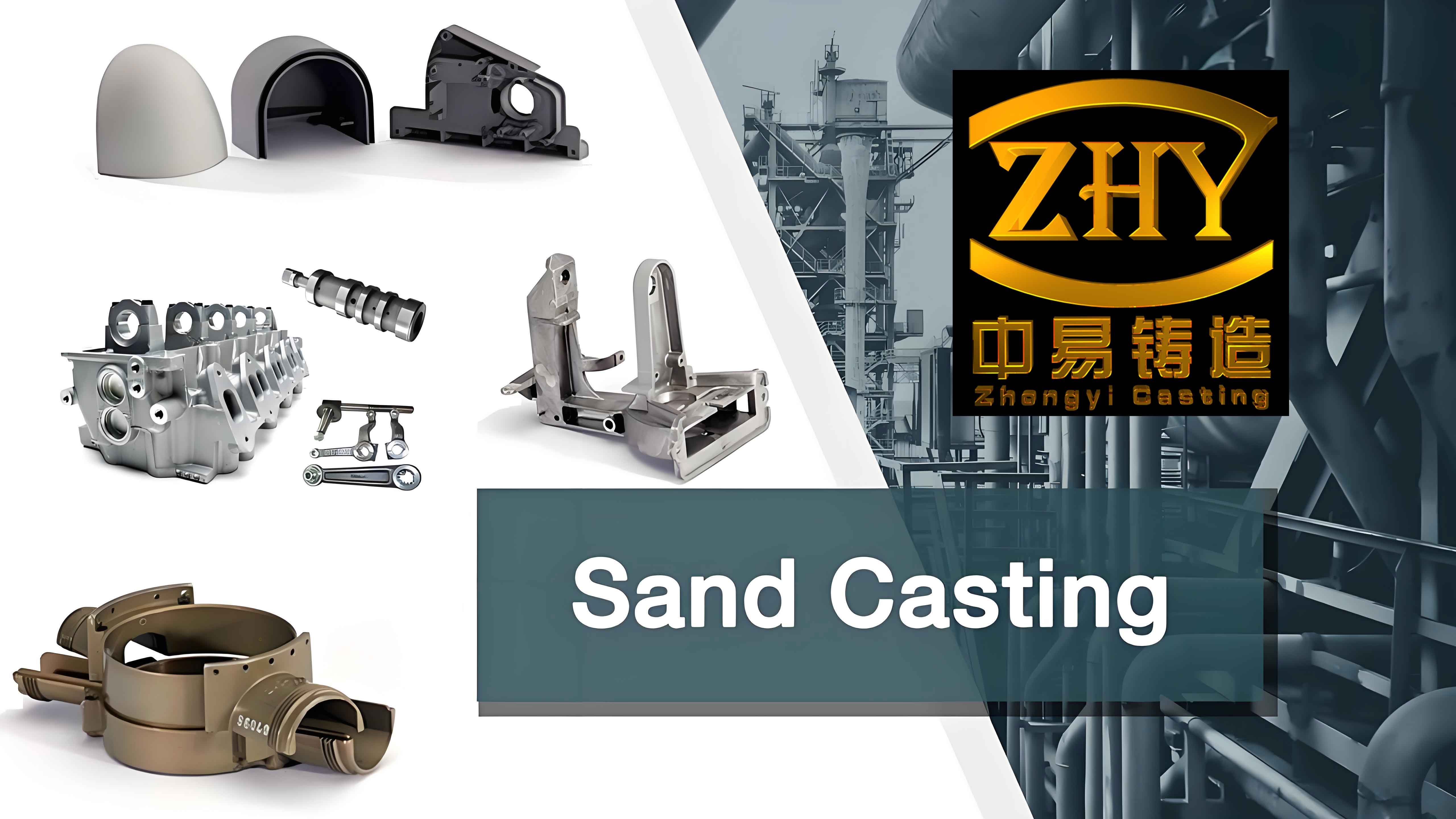
Sand Casting is a widely used method for manufacturing metal components, renowned for its versatility and cost-effectiveness. However, like any casting process, Sand Casting is susceptible to various Casting Defects that can affect the quality and performance of the final product. This article explores the common Casting Defects encountered in Sand Casting and offers strategies to address and mitigate these defects, thereby improving the overall quality of castings.
Understanding Sand Casting Defects
Casting Defects in Sand Casting arise due to numerous factors, including material quality, process parameters, and mold design. Identifying and understanding these defects is the first step toward addressing them effectively. Here are some of the most common Casting Defects found in Sand Casting:
- Porosity: The presence of small voids or cavities within the casting caused by trapped gases or shrinkage during solidification.
- Inclusions: Non-metallic particles, such as sand, slag, or oxides, that become entrapped within the casting.
- Misruns: Occur when the molten metal does not completely fill the mold cavity, resulting in incomplete castings.
- Cold Shuts: Form when two streams of molten metal meet but do not fuse properly, creating a seam or weak point.
- Shrinkage Defects: Caused by the reduction in volume as the metal solidifies, leading to internal or external voids.
- Hot Tears: Cracks that occur in the casting as it cools and contracts.
- Mold Shifts: Misalignment of the cope and drag parts of the mold, resulting in an off-center casting.
Addressing Porosity
Porosity is a common defect that can significantly impact the mechanical properties of the casting. It is essential to identify the causes and implement corrective measures.
Causes of Porosity
- Trapped gases in the molten metal.
- Improper venting in the mold.
- Excessive turbulence during pouring.
- Insufficient degassing of the molten metal.
Solutions for Reducing Porosity
- Improved Venting: Ensure adequate venting in the mold to allow gases to escape during pouring.
- Controlled Pouring: Pour the molten metal at a controlled rate to minimize turbulence and air entrapment.
- Degassing: Use degassing techniques to remove dissolved gases from the molten metal before pouring.
- Optimized Mold Design: Design the mold to promote smooth metal flow and reduce turbulence.
Table 1: Techniques to Address Porosity
Technique | Description | Benefits |
---|---|---|
Improved Venting | Adding vents to the mold | Reduces gas entrapment |
Controlled Pouring | Pouring metal at a steady rate | Minimizes turbulence |
Degassing | Removing gases from molten metal | Reduces porosity |
Optimized Mold Design | Designing for smooth metal flow | Decreases air entrapment |
Mitigating Inclusions
Inclusions are foreign particles within the casting that can weaken the structure and reduce its quality.
Causes of Inclusions
- Contamination of the molten metal.
- Poor quality sand or binders.
- Improper mold handling.
Solutions for Reducing Inclusions
- Clean Melting Practice: Ensure the furnace and crucibles are clean and free from contaminants.
- High-Quality Materials: Use high-quality sand and binders to reduce the likelihood of inclusions.
- Proper Mold Handling: Handle molds carefully to prevent the introduction of foreign particles.
List 1: Steps to Reduce Inclusions
- Use clean melting practices.
- Select high-quality sand and binders.
- Handle molds carefully.
Preventing Misruns
Misruns occur when the molten metal does not fill the mold cavity completely, resulting in incomplete castings.
Causes of Misruns
- Insufficient pouring temperature.
- Poor mold design.
- Low pouring speed.
Solutions for Preventing Misruns
- Proper Pouring Temperature: Maintain the correct pouring temperature to ensure the metal remains fluid.
- Optimized Mold Design: Design the mold to facilitate smooth and complete filling.
- Controlled Pouring Speed: Pour the metal at an appropriate speed to ensure complete filling.
Table 2: Preventing Misruns
Solution | Description | Benefits |
---|---|---|
Proper Pouring Temperature | Maintain correct temperature | Ensures fluidity |
Optimized Mold Design | Design for smooth filling | Prevents misruns |
Controlled Pouring Speed | Pour at appropriate speed | Ensures complete filling |
Avoiding Cold Shuts
Cold shuts are seams or weak points in the casting where two streams of metal did not fuse properly.
Causes of Cold Shuts
- Low pouring temperature.
- High thermal gradients.
- Poor gating system design.
Solutions for Avoiding Cold Shuts
- Adequate Pouring Temperature: Maintain a temperature high enough to keep the metal fluid.
- Uniform Cooling: Ensure uniform cooling to avoid high thermal gradients.
- Effective Gating System: Design an effective gating system to promote smooth metal flow.
List 2: Measures to Avoid Cold Shuts
- Maintain adequate pouring temperature.
- Ensure uniform cooling.
- Design effective gating systems.
Managing Shrinkage Defects
Shrinkage defects are caused by the volume reduction of the metal as it solidifies, leading to voids.
Causes of Shrinkage Defects
- Inadequate feeding of the molten metal.
- Improper riser placement.
- Poor mold design.
Solutions for Managing Shrinkage Defects
- Effective Riser Design: Use risers to feed molten metal into the casting during solidification.
- Directional Solidification: Promote directional solidification by designing the mold to solidify from the farthest point to the sprue.
- Adequate Feeding: Ensure adequate feeding of molten metal to compensate for shrinkage.
Table 3: Managing Shrinkage Defects
Solution | Description | Benefits |
---|---|---|
Effective Riser Design | Use risers to feed metal | Reduces shrinkage voids |
Directional Solidification | Design for directional solidification | Prevents shrinkage defects |
Adequate Feeding | Ensure sufficient metal feeding | Compensates for shrinkage |
Eliminating Hot Tears
Hot tears are cracks that form in the casting as it cools and contracts.
Causes of Hot Tears
- High thermal stresses during cooling.
- Inadequate mold strength.
- Poor mold design.
Solutions for Eliminating Hot Tears
- Controlled Cooling: Implement controlled cooling to reduce thermal stresses.
- Strong Molds: Use strong molds that can withstand the stresses of cooling.
- Optimized Mold Design: Design molds to minimize stress concentration points.
List 3: Steps to Eliminate Hot Tears
- Implement controlled cooling.
- Use strong molds.
- Optimize mold design.
Addressing Mold Shifts
Mold shifts occur when there is misalignment between the cope and drag parts of the mold, resulting in an off-center casting.
Causes of Mold Shifts
- Poor mold assembly.
- Inadequate clamping or alignment.
- Vibrations during pouring.
Solutions for Addressing Mold Shifts
- Proper Mold Assembly: Ensure molds are assembled correctly and aligned properly.
- Secure Clamping: Use secure clamping methods to prevent mold movement.
- Stable Pouring Environment: Minimize vibrations and disturbances during pouring.
Table 4: Addressing Mold Shifts
Solution | Description | Benefits |
---|---|---|
Proper Mold Assembly | Ensure correct assembly | Prevents misalignment |
Secure Clamping | Use secure clamping | Reduces mold movement |
Stable Pouring Environment | Minimize vibrations | Prevents mold shifts |
Conclusion
Addressing common Casting Defects in Sand Casting requires a thorough understanding of the causes and implementing effective strategies to mitigate these issues. By focusing on improved process controls, high-quality materials, and optimized mold designs, foundries can significantly reduce the incidence of defects and enhance the quality of their castings. Continuous monitoring and process improvement are crucial for achieving consistent and high-quality results in Sand Casting. Through these efforts, manufacturers can ensure the production of reliable and high-performance components, meeting the demands of various industries.