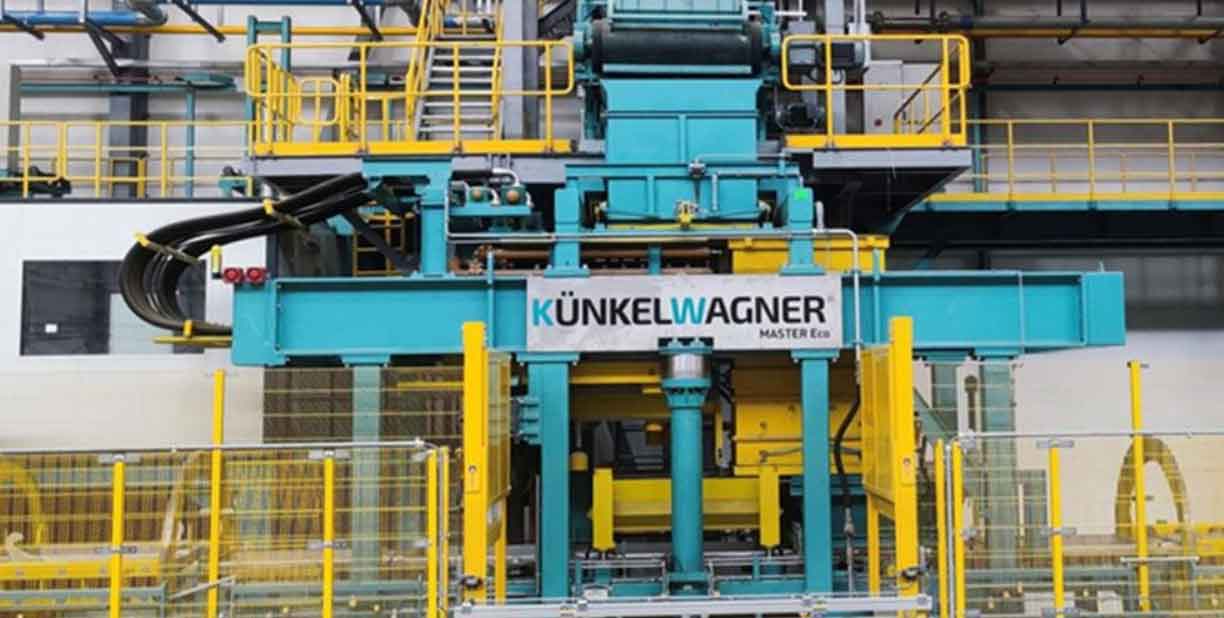
Casting China’s industry has made substantial progress in adopting and developing advanced technologies that enhance the efficiency, quality, and environmental sustainability of its manufacturing processes. Here’s an overview of some of the key technological advancements that are shaping the casting China’s industry:
1. Automation and Robotics
- Increased Automation: China has significantly invested in automating its casting China processes. This includes the use of robotic arms for tasks like mold making, pouring, and finishing, which improves precision and reduces human error.
- Integration with IoT: The incorporation of the Internet of Things (IoT) within automation technologies allows for real-time monitoring and control of the casting China processes. This integration helps in optimizing operations, reducing waste, and maintaining consistent quality.
2. Additive Manufacturing (3D Printing)
- Rapid Prototyping: 3D printing is increasingly used for rapid prototyping in the casting China industry, which speeds up the development process and testing of new cast designs.
- Complex Castings: Additive manufacturing enables the production of complex casting China molds that are difficult or impossible to create using traditional methods. This capability allows for the design and production of intricate parts required in industries like aerospace and medical devices.
3. High-Pressure Die Casting (HPDC)
- Enhanced Precision and Speed: High-pressure die casting technology is widely adopted for producing high-volume, net-shaped components with excellent surface finish and dimensional accuracy. HPDC is particularly prevalent in automotive applications where large quantities of durable components are required.
- Lightweight Materials: Advances in HPDC technology have also facilitated the increased use of lightweight alloys, such as aluminum and magnesium, which are essential for reducing vehicle weight to improve fuel efficiency and lower emissions.
4. Simulation and Modeling
- Process Optimization: Simulation software is extensively used to model and optimize casting China processes before actual production begins. These tools help predict how molten metals will behave within molds, identifying potential issues like air entrapment or incomplete filling.
- Reduced Development Time and Costs: By using simulation to predict outcomes and refine processes, manufacturers can significantly reduce material wastage, development time, and associated costs.
5. Advanced Materials Development
- New Alloy Formulations: Chinese researchers and manufacturers are at the forefront of developing new metal alloys with enhanced properties, such as increased strength, heat resistance, and corrosion resistance. These materials are increasingly critical in high-performance applications across various industries.
- Nano-materials and Composites: There’s growing interest in integrating nano-materials and composites into traditional casting China processes to enhance the mechanical properties and functionality of cast products.
6. Environmental Technologies
- Emission Reduction: In response to both domestic and international environmental regulations, casting China manufacturers are adopting technologies that reduce harmful emissions from foundries. This includes improvements in furnace designs and the adoption of cleaner fuel sources.
- Waste Minimization and Recycling: Technologies that allow for greater recycling of waste products and by-products of the casting China process are being implemented to make operations more sustainable.
7. Quality Control Technologies
- Automated Inspection Systems: Advanced imaging and scanning technologies are increasingly being used for the quality inspection of cast parts. These systems provide high accuracy in detecting surface and subsurface defects, ensuring that only parts meeting stringent quality standards are delivered.
These technological advancements have not only enhanced the capabilities and competitiveness of casting China’s industry but have also allowed it to better meet the increasing demands of global markets for higher quality, more complex, and environmentally friendly products.