Advancements in lost foam casting have indeed transformed the manufacturing landscape, bringing about significant improvements and expanding the possibilities of this casting technique. These advancements have propelled lost foam casting to new heights of efficiency, precision, and versatility. Here are some key advancements that have revolutionized lost foam casting:
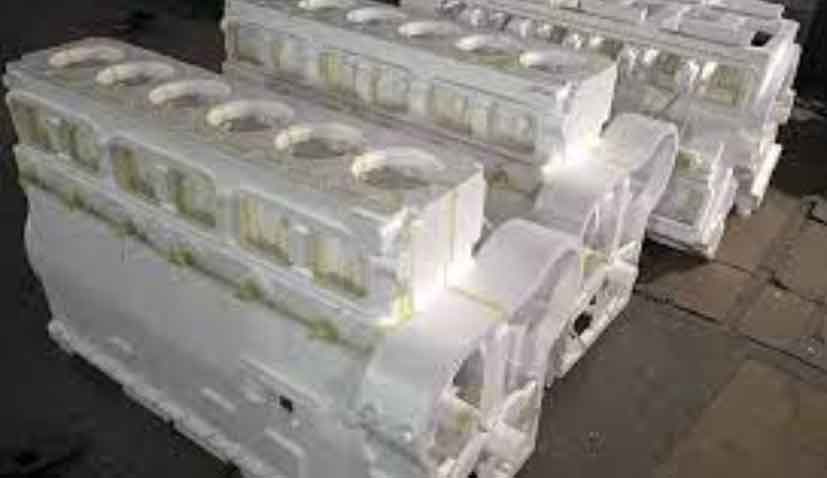
- Digital Design and Simulation:
- The integration of digital design tools and simulation software has greatly enhanced the design and optimization of lost foam castings.
- Advanced 3D modeling and CAD software enable the creation of intricate and complex part designs, taking full advantage of the design freedom offered by lost foam casting.
- Simulation tools allow for virtual testing and optimization of the casting process, predicting potential defects, and optimizing parameters to achieve optimal results.
- This digital integration improves efficiency, reduces the need for physical prototypes, and enhances the overall quality of castings.
- Additive Manufacturing and 3D Printing:
- Additive manufacturing, including 3D printing, has become a valuable asset in the production of foam patterns for lost foam casting.
- 3D printing enables the rapid and cost-effective production of highly intricate and customized foam patterns with excellent dimensional accuracy.
- It provides greater design flexibility, faster pattern iterations, and the ability to create complex internal structures and undercuts that were previously difficult to achieve.
- The combination of additive manufacturing and lost foam casting allows for faster and more efficient pattern production, reducing lead times and enabling quicker time-to-market.
- Improved Foam Pattern Materials:
- Advancements in foam pattern materials have contributed to enhanced performance and accuracy in lost foam casting.
- New foam materials with improved thermal properties, dimensional stability, and surface quality have been developed.
- These materials withstand the high temperatures and pressures of the casting process, resulting in more precise and reliable replication of part geometries.
- Improved foam patterns ensure better surface finish, reduced pattern degradation, and increased dimensional accuracy in the final castings.
- Automated Handling and Robotics:
- Automation and robotics have been increasingly integrated into the lost foam casting process, boosting productivity and efficiency.
- Automated handling systems for foam patterns, molds, and castings streamline material flow and reduce manual labor requirements.
- Robotic systems can be utilized for pattern assembly, coating, pouring, and shakeout, ensuring consistent and precise operations.
- This automation minimizes human error, improves repeatability, and allows for higher production volumes and faster cycle times.
- Advanced Casting Techniques:
- Advanced casting techniques, such as vacuum-assisted casting and pressure casting, have been combined with lost foam casting to further enhance its capabilities.
- Vacuum-assisted casting improves casting integrity by reducing gas-related defects and improving the filling of intricate sections.
- Pressure casting techniques ensure complete mold cavity filling and produce denser castings with improved mechanical properties.
- The integration of these techniques with lost foam casting expands its application range and enables the production of high-quality and high-performance castings.
- Process Control and Quality Assurance:
- Advancements in process control and quality assurance methodologies have enhanced the reliability and consistency of lost foam castings.
- Real-time monitoring and control systems enable precise control over casting parameters, ensuring consistent quality and reducing variability.
- Non-destructive testing techniques, such as X-ray, ultrasonic, and visual inspections, have been refined to detect potential defects and ensure casting integrity.
- Improved quality control measures, including statistical process control and quality management systems, provide traceability and accountability throughout the production process.
These advancements in lost foam casting have transformed the manufacturing landscape by enabling the production of highly complex, precise, and high-quality castings. The integration of digital tools, additive manufacturing, automation, advanced casting techniques, and improved process control has elevated lost foam casting to a cutting-edge technology capable of meeting the demanding requirements of modern industries. With its numerous advantages and continuous innovation, lost foam casting is driving advancements and shaping the future of metal casting.