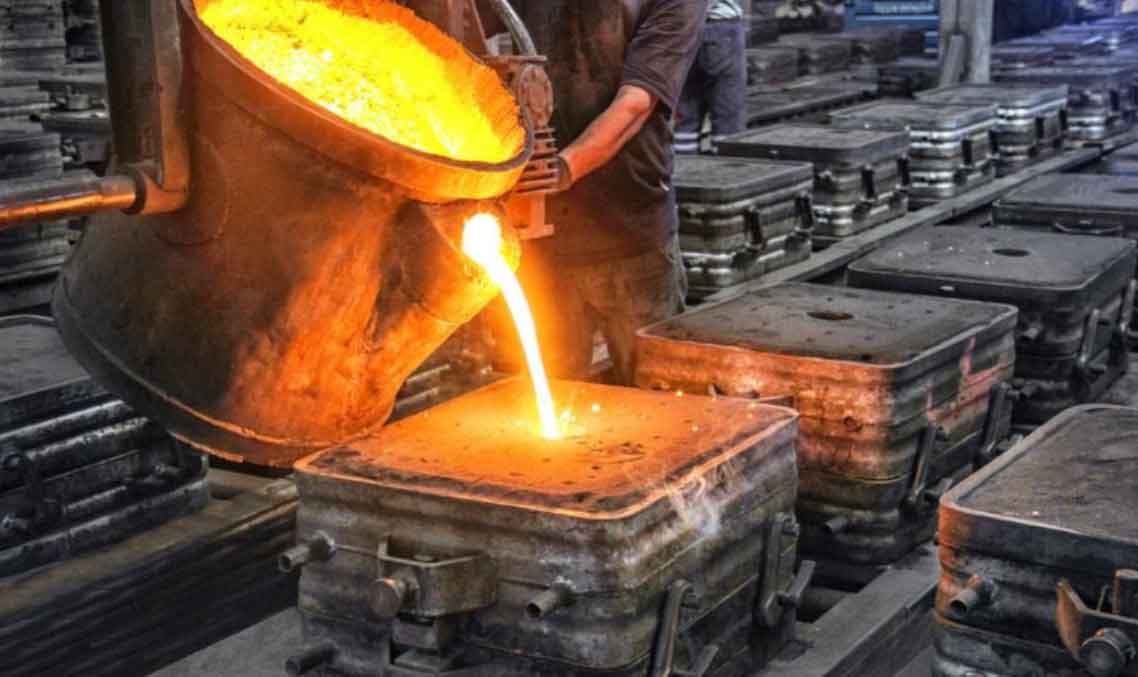
Advancements in mold and core making techniques have significantly improved sand casting processes, enabling foundries to produce complex and high-quality castings with greater efficiency and accuracy. These advancements address challenges such as dimensional accuracy, mold complexity, and surface finish. Here are some key advancements in mold and core making techniques in sand casting:
1. 3D Printing for Patterns and Cores:
- Additive manufacturing, specifically 3D printing, is revolutionizing mold and core making in sand casting. 3D printing allows for the rapid production of intricate patterns and complex cores, enabling faster prototyping and reduced lead times for tooling.
2. Shell Molding:
- Shell molding, also known as the Croning process, is a semi-automated mold-making technique that uses resin-coated sand to create thin and precise molds. This process provides excellent surface finish and dimensional accuracy for castings.
3. Ceramic Cores:
- Advanced ceramics are used to create cores with high dimensional stability and resistance to thermal stresses during casting. Ceramic cores enable the production of intricate internal features in castings that would be difficult to achieve with traditional sand cores.
4. Vacuum Molding:
- Vacuum molding is a method that uses a vacuum to draw the molding sand into the pattern cavity, resulting in precise and uniform mold density. This technique reduces defects and ensures better surface finish.
5. Lost Foam Casting:
- Lost foam casting, also known as evaporative pattern casting, utilizes foam patterns that vaporize when molten metal is poured into the mold, leaving behind the cast shape. This process allows for complex geometries and eliminates the need for pattern removal.
6. Hybrid Mold and Core Making:
- Hybrid mold and core making methods combine various techniques to leverage their individual advantages. For instance, using 3D-printed patterns combined with traditional sand molding for specific parts of a casting to optimize the process.
7. Digital Mold Design and Simulation:
- Advanced computer-aided design (CAD) and simulation software allow foundries to digitally design molds and analyze the flow of molten metal during casting. This helps optimize mold designs and gating systems, leading to improved casting quality.
8. Real-Time Monitoring and Feedback:
- Advanced sensors and monitoring systems are employed during mold and core making processes to provide real-time data on mold properties, allowing for immediate adjustments and quality control.
9. Automated Core Assembly and Placement:
- Robotics and automation are used to handle and assemble cores within molds with high precision and speed, ensuring accurate positioning and reducing manual labor.
10. Sustainable Binders and Additives:
- Foundries are exploring eco-friendly binder systems and additives for molds and cores to reduce environmental impact and emissions during the casting process.
By adopting these advancements, sand casting foundries can enhance mold and core making processes, resulting in improved casting quality, reduced lead times, and increased competitiveness in the manufacturing industry.