Gray cast iron casting is a popular and widely used process for shaping molten metal into solid forms, particularly components made from gray cast iron. The casting process involves several steps, and each one is critical to ensuring the final product’s quality and performance. Here’s an overview of the gray cast iron casting process:
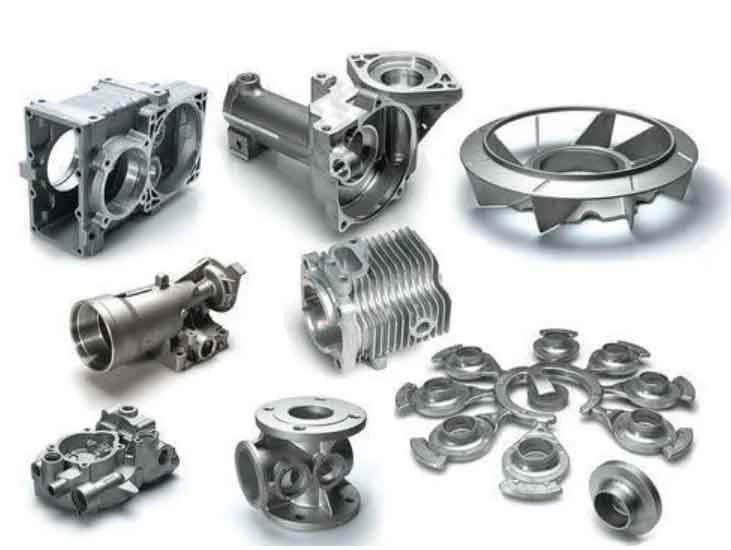
- Pattern Making: The casting process begins with the creation of a pattern. The pattern is a replica of the desired final product, typically made from wood, metal, or plastic. It includes all the details and features of the component to be cast.
- Mold Making: The pattern is used to create a mold, which is the negative impression of the final part. The mold can be made from sand, metal, or ceramic materials. For gray cast iron casting, sand molds are most commonly used due to their cost-effectiveness and flexibility.
- Molding: The mold is prepared by packing sand around the pattern to create the desired cavity shape. Multiple pieces, such as cope and drag, are used to create a complete mold. The mold cavity includes runners, gates, and risers to facilitate the flow of molten metal and prevent defects.
- Melting and Pouring: Gray cast iron, which consists primarily of iron, carbon, and silicon, is melted in a furnace at high temperatures. Once the molten metal reaches the correct temperature and composition, it is poured into the mold through the gating system.
- Solidification: After the molten metal is poured into the mold, it begins to solidify and take the shape of the cavity. Gray cast iron has a unique characteristic called eutectic solidification, where the carbon in the molten metal forms graphite flakes during solidification. These graphite flakes give gray cast iron its characteristic gray color and excellent machinability.
- Cooling and Shakeout: The casting is left to cool and solidify fully. Once it has cooled, the mold is shaken, and the sand is removed, leaving the solidified casting behind.
- Finishing and Inspection: The casting may require additional finishing operations, such as trimming, grinding, or machining, to achieve the desired dimensions and surface quality. After finishing, the casting undergoes inspection to ensure it meets the required specifications and quality standards.
- Heat Treatment (Optional): Some gray cast iron components may undergo heat treatment to improve their mechanical properties, such as hardness and strength.
The gray cast iron casting process is widely used in various industries, including automotive, construction, machinery, and more. It offers several advantages, such as cost-effectiveness, design flexibility, and the ability to create complex shapes and intricate details. With the proper design and manufacturing expertise, gray cast iron casting can produce durable and reliable components for a wide range of applications.