Advancements in sand casting technology have significantly contributed to enhancing the quality and precision of castings. Over the years, improvements in materials, equipment, process control, and simulation techniques have made sand casting a more reliable and efficient manufacturing method. Here are some key advancements that have led to the enhancement of sand casting parts:
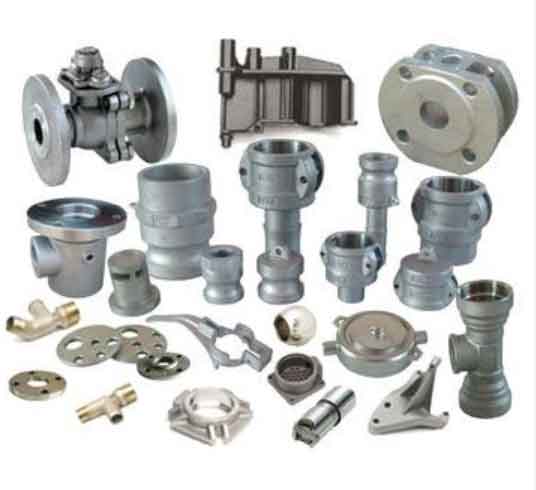
- Digital Simulation and Modeling:
- The use of advanced computer-aided design (CAD) and simulation software allows for virtual modeling and analysis of the casting process.
- Simulation tools can predict potential defects, optimize gating and riser designs, and simulate solidification to improve part quality and reduce the number of iterations.
- Patternless Casting:
- Advancements in 3D printing technology have enabled the creation of intricate sand molds directly from digital designs, eliminating the need for traditional patterns.
- Patternless casting allows for rapid prototyping and reduced lead times, especially for complex geometries.
- Additive Manufacturing in Sand Casting:
- The integration of additive manufacturing (3D printing) with sand casting has further expanded design possibilities.
- Hybrid manufacturing techniques can create complex cores and molds with internal channels and structures that were previously challenging to achieve.
- Improved Sand and Binder Systems:
- The development of high-performance sand and binder systems has improved mold stability, strength, and collapsibility.
- Advanced binders allow for reduced emissions during mold preparation, making the process more environmentally friendly.
- Automated and Robotic Sand Handling:
- Automated sand handling systems have reduced manual labor and improved consistency in sand mixing and mold preparation.
- Robotic systems can handle complex molding operations with high precision and repeatability.
- Innovations in Pouring and Cooling:
- Advanced pouring techniques, such as vacuum-assisted or low-turbulence pouring, ensure uniform metal flow and reduce defects like turbulence-induced defects.
- Improved cooling control techniques result in better solidification and reduce the risk of shrinkage-related defects.
- Non-Destructive Testing (NDT):
- The use of NDT methods like X-ray, ultrasonic testing, and magnetic particle inspection allows for comprehensive inspection of castings without damaging the parts.
- NDT helps identify internal defects and ensures the quality of critical components.
- Metal Alloy Development:
- Advancements in metallurgy have led to the development of new alloys with improved mechanical properties, better fluidity, and reduced susceptibility to defects.
- Quality Control and Traceability:
- Advanced quality control systems, including real-time monitoring, data analytics, and traceability, ensure consistency and compliance with standards.
These advancements have significantly enhanced the quality, precision, and cost-effectiveness of sand casting parts. As a result, sand casting remains a competitive and viable manufacturing method for producing a wide range of components for various industries, including automotive, aerospace, machinery, and more.