Steel casting, a vital manufacturing process in various industries, has witnessed significant advancements over the years. These innovations and improvements have enhanced the quality, efficiency, and capabilities of steel casting, making it a preferred choice for producing complex components. This article explores some of the key advancements in steel casting technology that have revolutionized the industry.
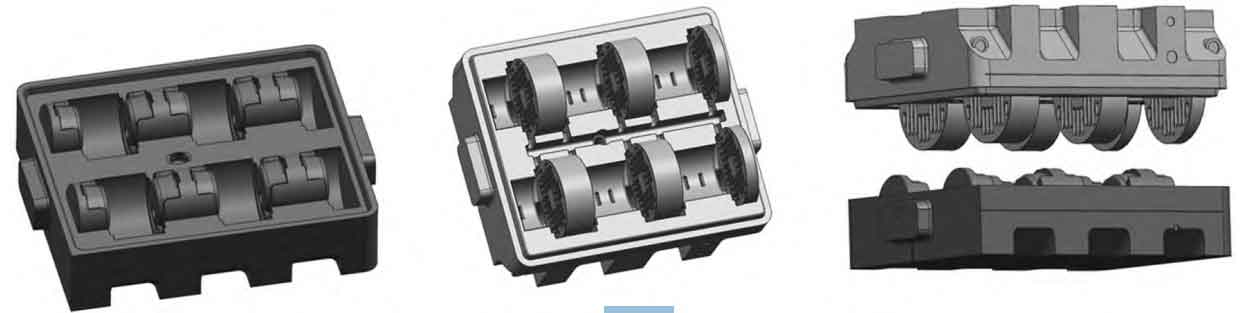
- Computer-Aided Design and Simulation: Computer-aided design (CAD) software and advanced simulation tools have revolutionized the steel casting process. Engineers can now create detailed digital models of castings, simulate the entire casting process, and analyze factors like solidification, cooling rates, and microstructural development. This enables optimization of casting designs, gating systems, and process parameters, resulting in improved casting quality and reduced production time.
- Additive Manufacturing (3D Printing): Additive manufacturing, also known as 3D printing, has made significant strides in steel casting. With the advent of metal 3D printing technologies, complex steel components with intricate geometries and internal features can be directly printed, eliminating the need for traditional pattern-making and tooling. This allows for rapid prototyping, customization, and the production of one-off or small-batch castings with reduced lead times.
- Advanced Materials and Alloys: Innovations in steel alloys and materials have expanded the capabilities of steel casting. New alloy compositions, including high-strength and corrosion-resistant steels, are being developed to meet the increasingly demanding requirements of various industries. These advanced materials offer improved mechanical properties, wear resistance, and durability, enabling the production of components for critical applications.
- Improved Molding and Core-Making Techniques: Advancements in molding and core-making techniques have contributed to higher precision and better surface finishes in steel castings. The use of advanced molding materials, such as ceramic and sand with improved properties, enables intricate details and finer surface finishes. Additionally, the development of innovative core-making processes allows for the creation of complex internal geometries, such as cooling channels and hollow sections.
- Automation and Robotics: Automation and robotics have revolutionized steel casting by enhancing process efficiency, consistency, and safety. Automated systems are employed for tasks like mold handling, pouring, shakeout, and cleaning. Robotics and advanced sensing technologies enable precise and repeatable operations, reducing human error and improving overall productivity.
- Quality Control and Inspection Techniques: Advanced inspection techniques, including non-destructive testing (NDT) methods such as X-ray, ultrasound, and 3D scanning, have become more sophisticated and accurate. These technologies enable comprehensive inspection of steel castings, detecting defects, and ensuring conformity to specified standards. Real-time monitoring and data analysis tools further aid in process optimization and quality control.
- Sustainable Practices: The steel casting industry is embracing sustainable practices to reduce environmental impact. This includes the adoption of energy-efficient furnaces, waste reduction and recycling programs, and the use of eco-friendly binders and additives in mold and core-making processes. Sustainable casting practices contribute to resource conservation and promote a greener and more environmentally responsible manufacturing approach.
These advancements in steel casting technology have transformed the industry, enabling the production of high-quality, complex steel components with improved properties, dimensional accuracy, and efficiency. As technology continues to evolve, the future of steel casting holds exciting possibilities, including further advancements in materials, process optimization, digitalization, and sustainable practices.