Steel casting is a complex manufacturing process that involves transforming molten metal into high-quality components with exceptional strength and durability. This article provides an overview of the steel casting process, highlighting the key steps involved in producing precise and reliable steel castings.
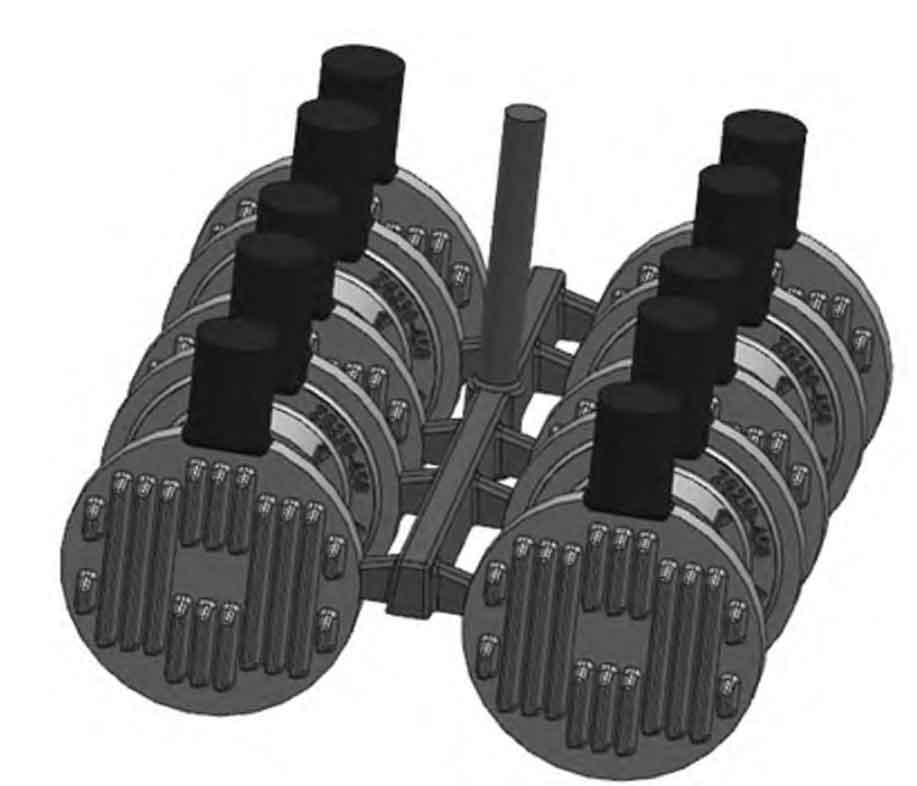
- Pattern Making: The process begins with the creation of patterns, which are replicas of the desired component. Patterns can be made from various materials such as wood, plastic, or metal. They are designed to accommodate shrinkage and allow for the formation of gating and riser systems.
- Mold Preparation: The patterns are used to create molds. In the traditional sand casting method, a mixture of sand and binders is packed around the pattern to create the mold cavity. The mold is then prepared by removing the pattern, leaving behind a cavity in the shape of the desired component.
- Molten Metal Preparation: The next step involves preparing the molten metal. Steel, which is an alloy of iron and carbon, is typically melted in a furnace at high temperatures. Alloying elements may be added to achieve specific material properties.
- Pouring: Once the molten metal reaches the desired temperature and composition, it is poured into the prepared mold cavity. Care must be taken during pouring to ensure proper filling of the cavity and minimize the introduction of impurities.
- Solidification and Cooling: After pouring, the molten metal undergoes solidification and cooling. During this phase, the metal transforms from a liquid state to a solid state, taking the shape of the mold cavity. Proper cooling rates and controlled solidification are crucial to achieve desired metallurgical properties.
- Shakeout and Cleaning: Once the metal has solidified, the mold is removed through shakeout, which involves breaking apart the mold to release the casting. The casting is then cleaned to remove any residual sand, oxide layers, or other contaminants.
- Finishing Operations: Depending on the desired specifications, additional finishing operations may be performed. These operations include trimming excess material, machining, grinding, heat treatment, surface coating, and inspection for dimensional accuracy and quality.
- Quality Assurance: Throughout the casting process, quality control measures are implemented to ensure the production of high-quality components. Non-destructive testing methods, such as X-ray, ultrasound, or magnetic particle inspection, may be employed to detect any defects or irregularities.
The steel casting process combines the art of pattern making, mold preparation, precise pouring, controlled solidification, and post-casting operations to transform molten metal into high-quality steel components. The process requires expertise, careful control of variables, and adherence to strict quality standards to achieve the desired mechanical properties, dimensional accuracy, and surface finish. Steel casting is widely used in various industries, including automotive, construction, aerospace, and power generation, due to its exceptional strength, durability, and versatility.